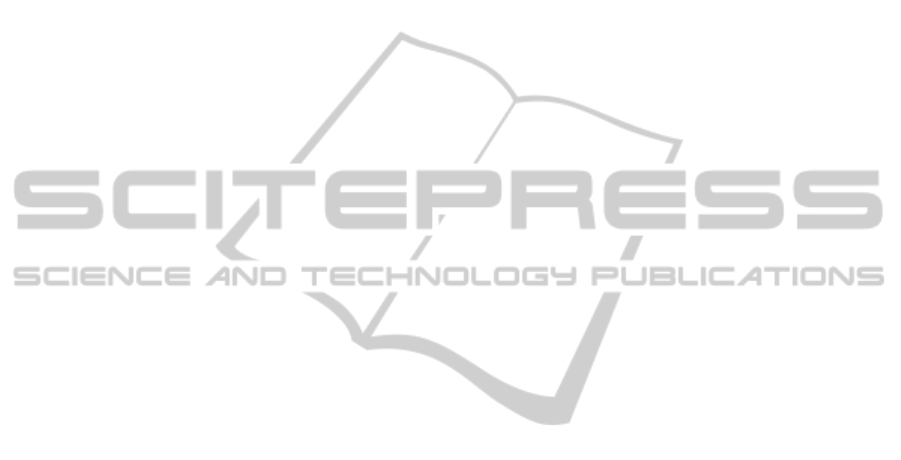
5 CONCLUSIONS
In validation process for simulated impact of FIS,
measured data of bore pressure resultant force of a
howitzer 1 living firing is taken as truth value.
Simulation effect of FIS can be established via
comparisons of 2 simulated impact force values.
The following conclusions can be obtained from
measured test data and calculated results in Table 1:
Comparison results of selected three key
parameters as impulse, duration of shock pulse
and maximal impact force can be used as
simulation credibility assessment basis of FIS;
Maximum error of total impulse is 2.94 %,
maximal value error of impact force is 4.89 %,
which meet design requirements of 15% on
simulation error;
Maximum error for impulse duration is -62.15 %,
which do not meet design requirement of 15% on
simulation error;
The shape of bore pressure resultant force curve
in live firing is basically in accord with impact
force curve of FIS.
Maximum error for two impulse durations all exceed
50 %, the main reason is that live firing data include
20ms after pill's getting out of gun bore, namely
after-effect period. If after-effect period is
subtracted, maximum error for impulse duration
satisfies required simulation precision of 15%.
There are several advantages of the FIS over live
fire testing. For example, FIS is easily operated
indoors, not weather dependent. It also enables test
engineers to examine any failure repeatedly during
weapon approval test. FIS can be operated
approximately two to three times per minute thereby
enabling test engineers to examine the recoil
systems' response to repeated rapid firing. However,
the most important benefit of FIS is reduction in the
cost associated with live fire testing of large caliber
tank and howitzer cannons, which averages $500 to
$2K per round.
REFERENCES
Aberdeen Test Center, 1994. Report of Survey Conducted
at U. S. ARMY COMBAT SYSTEMS TEST ACTIVITY,
Center of Excellence for Best Manufacturing Practices
ABERDEEN, MD.
Aberdeen Test Center, 2010. Firing Impulse Simulator
[online]. DoD TechMatch. Available from
http://www. dodtechmatch.com/DOD/Lab/View
Facility.aspx?id=71348. [Accessed on 7
th
February,
2015].
Cast, M., 2001. Army test move to ‘virtual proving
ground’. National Defense, (11), 62-64.
Di, C. C., Liu, L., Zheng, J., and Chen, Y. C., 2012a.
Numerical simulation on dynamic recoil test with gun
muzzle subjected to high-velocity impact. Explosion
and Shock Waves, 32 (3), 323-327.
Di, C. C., Yang, Y. L., Qin, J. Q., and Cui, K. B., 2012b.
Influences research of impact factors on gun recoil
tester. Chinese Journal of Gun Launch & Control, (2),
25-28.
Faller, J. G., 1997. Simulating firing loads provides
flexibility and test repeatability [online]. Available
from http://www.thermotekusa.com. [Accessed on 7
th
February, 2015].
Gao, T., He, C., Fan, Z. J., and Guo, H. L., 2014. Analysis
and evaluation of artillery fire simulation test. Key
Engineering Material, (620), 632-637.
Lang, F. Y., and Li, W. J., 2012. Design of a Large
Caliber Self-Propelled Gun Shooting Simulation
device. Chinese Journal of Gun Launch & Control,
(3), 52-54.
Liu, L., Di, C. C., Pan, B. Q., and Yao, J. J., 2011. Design
and research on gun dynamic recoil simulation test
mechanism. Chinese Journal of Gun Launch &
Control, (1), 36-40.
Sanders, P., and Patenaude, A., 1996. Study on the
Effectiveness of Modeling and Simulation in the
Weapon System Acquisition Process, Final Report of
Department of Defense of America, Washington D.C.
Yao, Y. W., 2001. Simulation test system of gun recoil
and numerical calculations. Acta Armamentarii, 22(2),
152- 155.
Zhao, F. Q., Hua, L., and Yang, Z. J., 2003. Study on test
and measurement for recoil mechanism of a tank gun.
Chinese Journal of Gun Launch & Control, (s), 94-96.
SIMULTECH2015-5thInternationalConferenceonSimulationandModelingMethodologies,Technologiesand
Applications
460