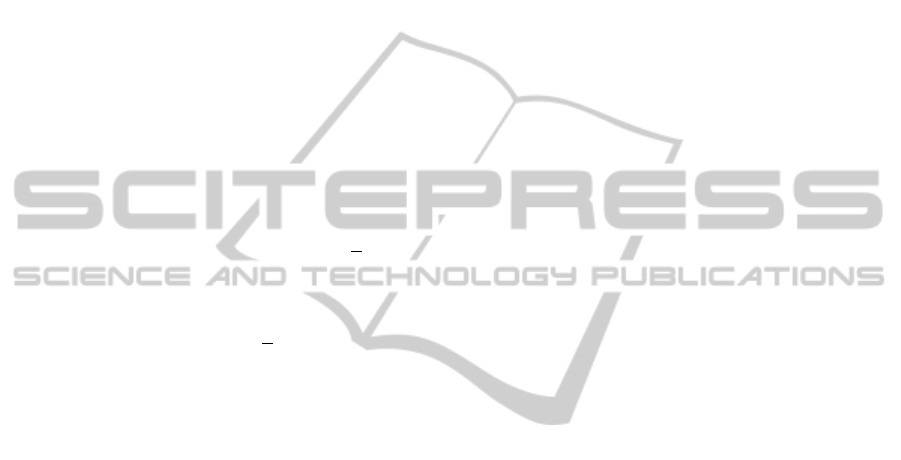
ular robot whose number of DOF can be increased
connecting more modules in series. Finally, (Yoon
and Rus, 2007) present 3-DOF robots that can indi-
vidually explore 3-D trusses or can be combined with
other robots to form more complex kinematic chains
with higher maneuverability.
Parallel climbing robots are less common, but they
have also been studied. These architectures offer a
higher payload-to-weight ratio than serial robots, but
their workspace is more limited. (Aracil et al., 2006)
propose using a Gough-Stewart platform as the main
body of a robot for climbing truss structures, pipelines
and palm trees. The robot remains fixed to the struc-
ture using grippers or embracing it with its annular
platforms.
Finally, hybrid climbing robots are composed of
some serially connected parallel mechanisms, and
they have the advantages of both architectures: high
maneuverability, rigidity and load capacity. A hy-
brid robot for climbing 3-D structures is proposed
by (Tavakoli et al., 2005), who combine a 3-RPR par-
allel robot with a rotation module connected in series.
Another hybrid robot is proposed in (Figliolini et al.,
2010). In this case, the robot is biped and each leg is
the serial combination of two 3-RPS parallel robots.
Hence, the complete robot has 12 DOF.
In this paper, we present a novel 10-DOF redun-
dant hybrid robot for climbing 3-D truss structures.
The robot is biped and its legs are connected to a hip
through revolute joints. Each leg is the serial combi-
nation of two parallel mechanisms that possess linear
hydraulic actuators, which provide a high load capac-
ity and stiffness. The design of the robot makes it
specially suitable to maneuver in 3-D truss structures
and perform transitions between planes with different
orientations. In this paper, we focus on the forward
and inverse kinematic problems of the robot, which
are necessary to plan trajectories in 3-D structures.
We also present a Java simulation tool that allows us
to verify the kinematic models obtained in this paper
and demonstrate the ability of the robot to explore 3-
D trusses.
This paper is organized as follows. The architec-
ture of the robot is described in detail in Section 2.
Next, the forward kinematic problem of the complete
robot when one foot remains fixed is solved in Sec-
tion 3. In Section 4, a simplified yet useful version
of the inverse kinematic problem is solved. Then,
Section 5 presents a tool that simulates the forward
kinematics of the robot. This tool is used to demon-
strate the execution of some example trajectories by
the robot in a 3-D structure. Finally, the conclusions
and future work are exposed in Section 6.
2 DESCRIPTION OF THE ROBOT
Figure 1a shows a 3-D model of the biped climbing
robot. The robot has two identical legs (A and B)
connected to the hip through revolute joints driven by
motors (angles θ
A
and θ
B
). Each leg has three links:
a core link and two platforms. The lower platform is
the foot of the leg and carries the gripper that fixes
the robot to the structure (the grippers are not consid-
ered in the kinematic analysis presented in this paper).
The upper platform is connected to the hip through
the aforementioned revolute joint. Each platform is
connected to the core link by means of two prismatic
actuators and a passive slider.
The mechanism composed of the core link, one
platform, and the two prismatic actuators that con-
nect these two elements, is a closed-loop linkage that
will be called hereafter “parallel module”. The paral-
lel modules are planar mechanisms that can be repre-
sented schematically as shown in Figure 1b. Hence,
each leg is the serial combination of the parallel mod-
ules 1 (which is connected to the foot) and 2 (which is
connected to the hip). The prismatic actuators of each
parallel module lie in opposite sides of the plane Π
j
,
which is one of the planes of symmetry of the core
link of the leg j (see the side view in Figure 1a). This
is indicated with dashed lines in Figure 2.
Figure 1a also shows some reference frames at-
tached to different parts of the robot. In this paper,
the X, Y , and Z axes of reference frames will be rep-
resented in red, green, and blue colors, respectively.
The frames H
A
and H
B
are fixed to the hip of the robot,
whereas the frames A and B are respectively attached
to the feet of the legs A and B.
The robot has 10 DOF: the rotation angles θ
A
and
θ
B
, and the four prismatic actuators of each leg. In
the next sections, the forward and inverse kinematic
problems of the robot will be analyzed. After that, we
will simulate the forward kinematics to demonstrate
its ability to explore 3-D structures.
3 FORWARD KINEMATICS
In this section, the forward kinematic problem (FKP)
of the robot is solved. The problem considered here
consists in calculating the position and orientation of
one foot with respect to the other foot when the joint
coordinates are known: the angles θ
A
and θ
B
and the
lengths (l
ij
,r
ij
) of the linear actuators of the parallel
modules (i ∈
{
1,2
}
, j ∈
{
A,B
}
). First, the forward
kinematics of the parallel modules is analyzed.
KinematicAnalysisandSimulationofaHybridBipedClimbingRobot
25