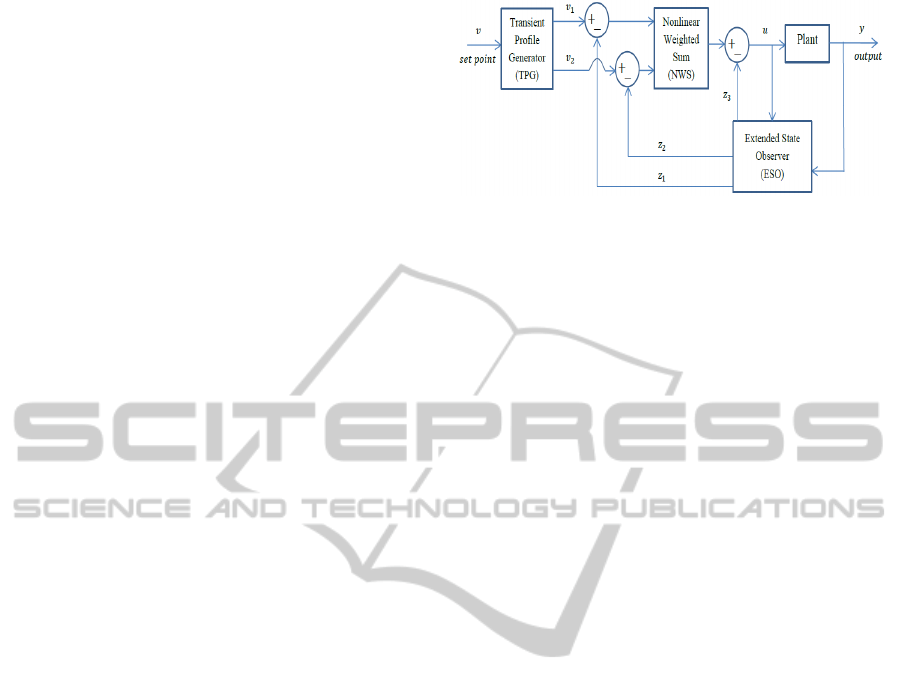
models. Both static and dynamic PCR models are
developed. In dynamic PCR models, tray
temperature measurements at the current and past
sampling times are used as model inputs in order to
account for dynamic relationship between tray
temperatures and product compositions. To the
authors’ knowledge, the integration of ADRC and
dynamic inferential control has not been reported in
the literature.
This paper is organised in five sections. Section
2 presents an overview of ADRC and inferential
control. Section 3 presents the development of static
and dynamic estimator using PCR. The inferential
feedback control of distillation compositions based
on these software sensors is represented in Section 4.
Finally, the last section draws some concluding
remarks.
2 OVERVIEW OF ADRC AND
INFERENTIAL CONTROL
Disturbances and uncertainties are the main issues in
control system synthesis especially in engineering
applications. Dealing with disturbances and
uncertainties has attracted the attention of engineers
and scientists. There have been many control
methods suggested for dealing with uncertainties
such as adaptive control, robust control, variable
structure control, intelligent control, etc. However,
due to their dependence and complexity on advanced
analytical methodologies, these methods have
certain limitations in engineering applications.
PID control is still widely used in process control
because of its simplicity and robustness. The main
limitations of PID control are the error computation,
noise degradation due to the derivative control,
oversimplification and the loss of performance in the
control law in the form of linear weighted sum and
complication associated to the integral control.
2.1 Overview of ADRC
ADRC, derived the essence from PID control and
observer, was pioneered over ten years ago by
Jingqing Han (Han, 2009). The basic principle of
ADRC is that it uses the extended state observer
(ESO) to estimate the existing total disturbances,
and cancel it or remove it from the system. The main
advantage of ADRC is the disturbance rejection
(Gao et al, 2011). Fig. 1 shows the structure of
ADRC, which consists of three main components:
transient profile generator (TPG), non-linear
weighted sum (NWS), and ESO.
Figure 1: Structure of ADRC.
A. Transient Profile Generator
The control signal with TPG can rapidly track the
setpoint signal without overshoot with strong
adaptability and robustness (Wang and Miao, 2010).
TPG can smooth out sudden changes in setpoints.
B. Non-linear Weighted Sum of Control Errors
Over-simplification of PID control law is the major
limitation of the conventional PID controller that
consists of present, predictive and accumulative
errors. This over-simplification ignores other
complex parameters that can make the PID control
performance more robust to the error signal. As a
result, Han (2009) presented an alternative non-
linear function which depends on the magnitude of
error signal to produce the control signal.
C. Extended State Observer
The main idea of ESO is to online estimate the
variables that are usually inapproachable
instrumentation-wise such as internal non-linear
dynamics, external disturbance and model errors.
Then, the undesired disturbances are then effectively
compensated in the control effort. ADRC can
successfully drive the controlled output signal to its
required value if the ESO has a precise estimation
for the internal non-linear dynamics, external
disturbances and model error of the plant (Xia et al,
2007).
2.2 Overview of Inferential Control
In the product composition control in distillation
columns, it is really challenging to get reliable and
accurate product composition measurements without
long time delay in the sampling and analysis
process. Numerous composition analysers such as
gas chromatography regularly introduce significant
time delays. The overall time delay in composition
measurements normally between 10 to 20 minutes
(Mejdell and Skogested, 1991). Such amount of time
delay substantially reduces the achievable
performance of composition controllers. Moreover,
InferentialActiveDisturbanceRejectionControlofaDistillationColumnusingDynamicPrincipalComponentRegression
Models
359