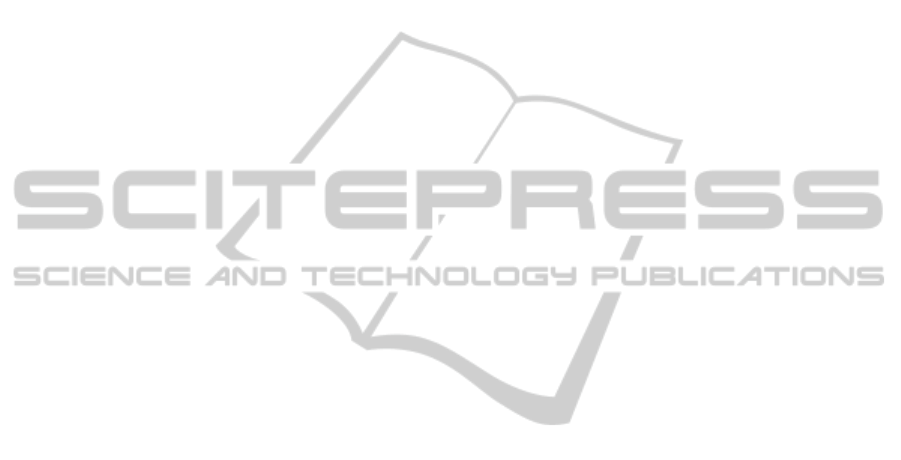
2 LITERATURE REVIEW
2.1 BIM Quantity Takeoffs
While traditional estimation methods conduct
quantity takeoffs from 2D CAD drawings, a BIM
tool can obtain the required data and measurements
for quantity takeoff from a 3D model (Rundell 2006;
Shen and Issa 2010). Recently, many researchers in
Taiwan have developed BIM-based tools to support
quantity takeoffs. For example, Chen (2011) used
Autodesk Revit to perform quantity takeoffs for a
twelve-story reinforced concrete office building. His
study showed that the quantities of concrete and
steel extracted from BIM were 0.5% and 3.7% less
than the conventional estimation, respectively. Chai
(2012) developed a Revit API program to
automatically calculate the quantities of forms.
Regarding the quantities of forms, for instance, the
BIM generates the results were close to the ones
calculated manually, with only 1% difference.
2.2 BIM and Cost Estimates
Eastman et al. (2011) pointed out that although there
are BIM-based quantity takeoffs tools available to
assist the cost estimates, there is no BIM software
with full estimation functions. Therefore, a cost
estimator must either export the BIM quantities into
the cost estimation software, Link the BIM tool
(software) to the cost estimation software through an
API, or export BIM model data into a BIM-based
cost estimation software (Rundell 2006; Eastman et
al. 2011).
3 MODEL FOR ESTABLISHING A
S-CURVE
This study proposes a model to establish S-curves of
construction projects. The proposed model consists
of four steps, as shown in Fig. 1: (1) developing a
BIM model associated with cost items, (2)
conducting searching algorithms to perform quantity
takeoffs in Autodesk QTO, (3) mapping contractual
unit prices from cost estimation software, and (4)
converting to Excel to build a S-curve. These four
steps are described in the following subsections.
Step 1: Developing a BIM Model Associated
With Cost Items.
In the proposed model, first, a BIM model with the
level of detail (LOD) 300 must be built. This BIM
model is composed of physical components and
information parameters. Physical components are
such as columns, beams, walls, slabs, doors,
windows and rooms.
The information parameters in each physical
component are divided into two parts: additional
geometric parameters and cost-item parameters.
Besides to the geometric data (such as length, width,
height, area, and volume) of a physical component,
additional geometric parameters are required to
conduct quantity takeoffs. For instance, the
information required to conduct the quantity takeoffs
for the steels of a wall include: the data of length and
height of the wall from the common geometric
parameters; and, the data of spacing of horizontal
bar, spacing of vertical bar, steel unit weight, and the
number of bar layer for this wall from the additional
geometric parameters.
To add the cost items associated with each
physical component, this study uploads the
contractual cost items to the Revit using the
"keynotes", "assembly codes", and "family type
catalogs" functions in Revit. This step sets a base to
enable each physical component to map the cost
items that specify the construction materials used in
erecting the component.
Step 2: Conducting Searching Algorithms to
Perform Quantity Takeoffs
in Autodesk QTO.
The model proposes to apply the search takeoff tool
in Autodesk QTO to create takeoff objects (that is,
cost items associated with each activity) and then
quantify the objects. To specify the takeoff objects
needs to set search criteria first. The proposed search
algorithm defines various search criteria (floor,
physical object, cost item, and area) with respect to
different types of scheduling activities (structure,
site work, and finishes activities).
For example, the structure activities are such as
setting steel of 1st floor columns/walls, setting steel
of 1st floor beams/slabs, setting form of 1st floor
columns/walls, setting forms of 1st floor
beams/slabs, etc. Thus, in the structure activities, the
search criteria are floor (1st, 2nd, 3rd, etc.), physical
object (column, wall, beam, and slab), and cost item
(involved construction materials).
Specifically, for instance, activity “setting steel
of 1st floor columns/walls” includes two physical
components: columns and walls. Each component is
associated with two cost items, namely, “steel,
SD420, labor and material included” and “steel,
SD420W, labor and material included”. The takeoffs
of steel in this activity are performed in four steps:
ICSOFT-EA2015-10thInternationalConferenceonSoftwareEngineeringandApplications
140