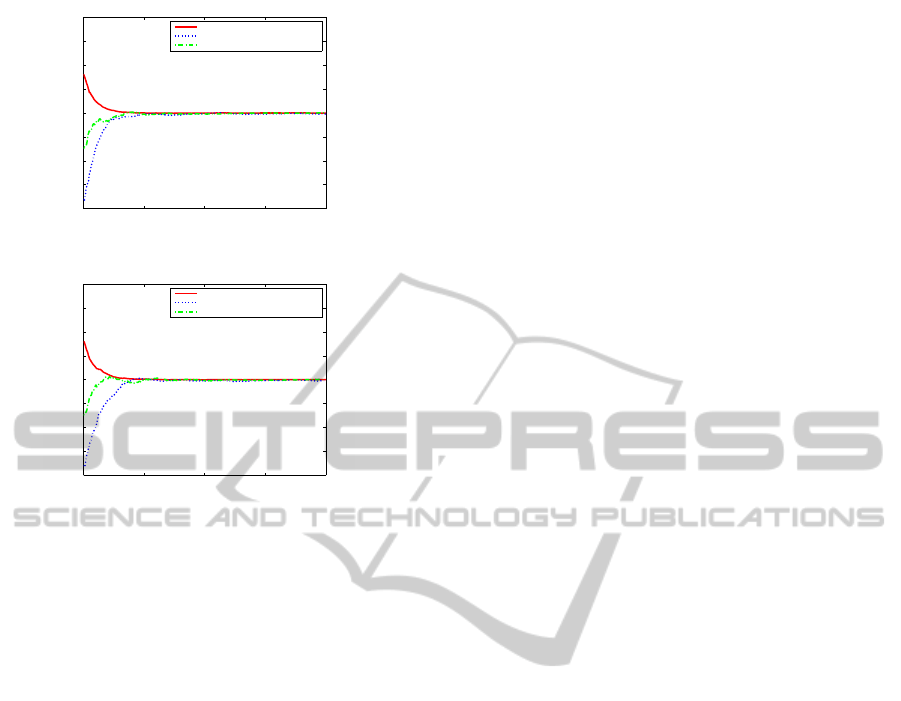
0 5 10 15 20
−20
−15
−10
−5
0
5
10
15
20
time/s
Angle/rad
Synchronization joint position error 1
Synchronization joint position error 2
Synchronization joint position error 3
Figure 8: Synchronized joint position error (β 6= 0).
0 5 10 15 20
−20
−15
−10
−5
0
5
10
15
20
time/s
Angle/rad
Synchronization joint position error 1
Synchronization joint position error 2
Synchronization joint position error 3
Figure 9: Synchronized joint position error (β = 0).
verge to the neighbourhood in advance. While, syn-
chronized joint position errors ε
1
(t), ε
2
(t) and ε
3
(t)
will converge simultaneously in Fig. 8.
5 CONCLUSIONS
We have proposed a novel adaptive sliding mode con-
troller for synchronized joint position tracking con-
trol of robotic manipulator. The proposed algorithm
does not require the precise dynamic model, and is
very practical than the traditional sliding mode con-
troller. On one hand, the proposed one addresses
a better convergence to zero of both joint position
tracking errors and joint position velocity tracking er-
rors. On the other hand, it ensures the transient re-
sponse and performance of synchronized joint posi-
tion tracking. And, the proposed controller maintain
the synchronized joint position errors will converge
to the neighbourhood simultaneously. Simulation re-
sults obtained from a 3-link non-linear planer robot
manipulator demonstrate the effectiveness of the ap-
proach under various disturbances.
ACKNOWLEDGEMENTS
The work here is supported by the National Sci-
ence and Technology Supporting Plan (Grant No.
2015BAF01B04), Collaborative Innovation Center
of High-End Manufacturing Equipment, the State
Key Basic Research Program of China (Grant No.
2011CB706903), the National Natural Science Foun-
dation of China (Grant No. 51175208), the Funda-
mental Research Funds for the Central Universities
(Grant Nos. 2013ZZGH001 and 2014CG006).
REFERENCES
Ge, M. and Guan, Z. H. (2012). Robust mode-free slid-
ing mode control of multi-fingered hand with position
synchronization in the task space. In Proceeding of the
5th International Conference on Intelligent Robotics
and Applications.
Guo, Y. Z. and Woo, P. Y. (2003). Adaptive fuzzy sliding
mode control for robotic manipulators. In Proceeding
of 42nd IEEE Conference on Decision and Control,
pages 149–159, Hawaii. IEEE.
Ho, H. F. and Wong, Y. K. (2007). Robust fuzzy track-
ing control for robotic manipulators. Simulation Mod-
elling Practice and Theory, 15(7):801–816.
Hu, Y. M. and Liu, J. (2014). Seam tracking control of weld-
ing robotic manipulators based on adaptive chattering-
free sliding-mode control technology. In Proceed-
ing of 11th International Conference of Informatics in
Control, Automation and Robotics. INSTICC.
Koren, Y. (1980). Cross-coupled biaxial computer con-
trols for manufacturing systems. ASME Journal
of Dynamic Systems, Measurement and Control,
102(4):265–272.
Liu, Y. C. and Chopra, N. (2012). Controlled synchroniza-
tion of heterogeneous robotic manipulators in the task
space. IEEE Transactions on Robotics, 28(1):268–
275.
Sage, H. G. and Mathelin, M. F. (1999). Robust control of
robot manipulators: a survey. International Journal of
control, 72(16):1498–1522.
Slotine, J. E. and Li, W. (1989). Composite adaptive control
of robot manipulators. Automatica, 25:509–519.
Slotine, J. E. and Li, W. P.(1987). On the adaptive control of
robot manipulators. International Journal of Robotics
Research, 6(3):49–59.
Slotine, J. E. and Li, W. P. (1991). Applied Nonlinear Con-
trol. Prentice Hall, Englewood Cliffs.
Spong, M. W. and Hutchinson, S. (2006). Robot Modeling
and Control. John Wiley & Sons, New York.
Sun, D. (2003). Position synchronization of multiple mo-
tion axes with adaptive coupling control. Automatica,
39:997–1005.
Sun, D. and Mills, J. K. (2002). Adaptive synchronized
control for coordination of two robot manipulators.
In Proceeding of IEEE International Conference on
Robotics and Automation, pages 976–981, Washing-
ton DC. IEEE.
Sun, D. and Shao, X. (2007). A model-free cross-coupled
control for position synchronization of multi-axis mo-
tions: theory and experiments. IEEE Transaction on
Control Systems Technology, 15(2):306–314.
ICINCO2015-12thInternationalConferenceonInformaticsinControl,AutomationandRobotics
244