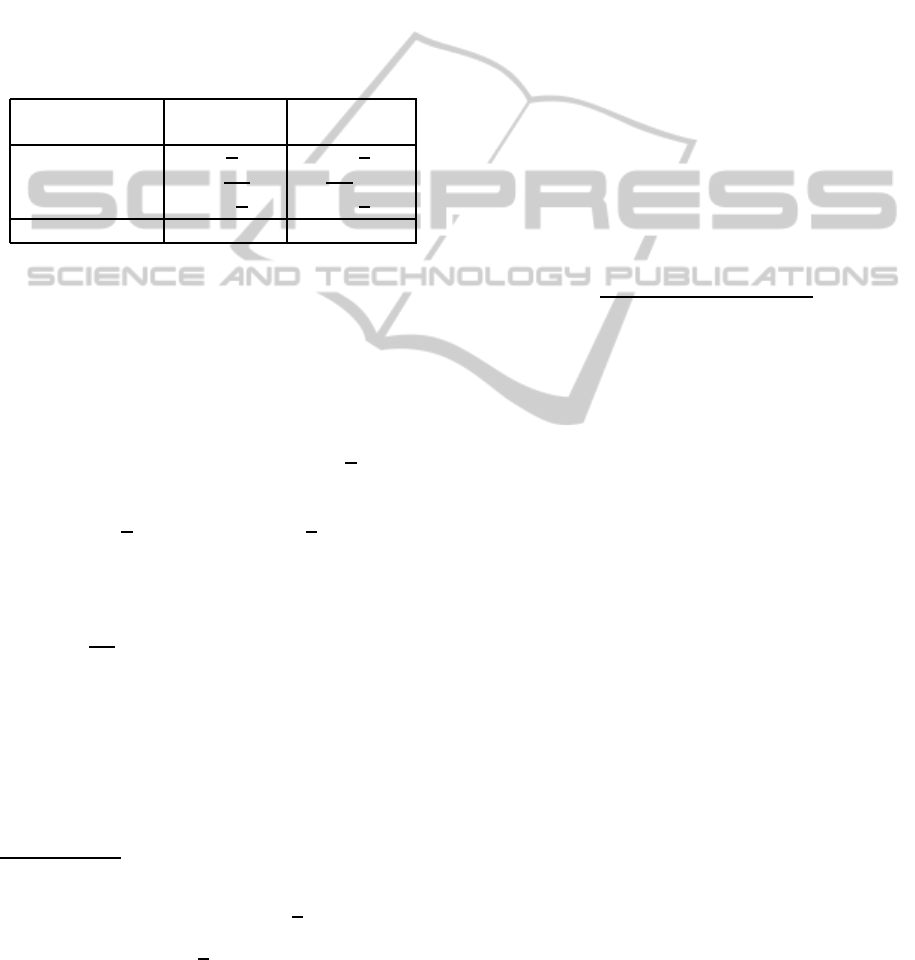
ties including stiffnesses and instabilities so that a
better compromise among the design parameters can
be achieved. The magnetic material used here is
NdFeB with the remanence magnetic flux density of
1.23Telsa. The schematics of two passive bearings
obtained after several design iterations are shown re-
spectively in Figure 5 and Figure 6. Particularly, in
passive bearing II, while the outer stack consists of
three magnetic rings, the inner stack consists of four
magnetic rings, and the magnetic poles of the outer
stack are dislocated from those of the inner stack by
0.2mm in the downward manner.
Table 1: Properties of the Passive Bearings.
Passive
Bearing I
Passive
Bearing II
Radial Stiffness 8,000
N
m
38,000
N
m
Tilting Stiffness 16.62
N·m
rad
1.4
N·m
rad
Axial Instability 26,300
N
m
74,400
N
m
Axial bias force 49.44N −21.2N
The radial stiffness, tilting stiffness, axial stabil-
ity and the upward force respectively provided by the
two passive bearings are listed in Table 1. According
to this table, the tilting stiffness is mainly contributed
by passive bearing I and the radial stiffness is mainly
contributed by passive bearing II. In order to keep
the axial instability to minimum, we deliberately limit
the radial stiffness of passive bearing II, which is the
main source of axial instability, to 38, 000
N
m
by hav-
ing unequal numbers of magnetic rings for the inner
and outer stack
1
. The total radial stiffness in this case
is only 46,000
N
m
, which is still 1, 000
N
m
less than the
lower bound computed in previous section. As will
be shown later, the additional radial stiffness needed
will be provided by the active bearing. From the ta-
ble it can also be found that the total tilting stiffness is
only 18.02
N·m
rad
, which means that the rotor will expe-
rience a resonance at 2,200rpm. Due to the limited
space for placing the magnets and the unavailability
of magnets of extreme strength, it is difficultto further
increase the tilting stiffness to avoid the resonance.
In the following investigation, this tilting stiffness is
adopted, so as the rotor accelerates towards the rated
speed, it will experience resonance shortly. Since the
unbalance force is small at low speeds, as long as the
1
The finite element simulations indicate that if the inner and
outer stacks of passive bearing II both have three rings,
then the radial stiffness is only 33.450
N
m
. If the number
of rings for both stacks are increased to four, the radial
stiffness becomes 44,510
N
m
but the axial instability also
becomes excessive. As a comprimise, unequal number of
rings are adopted respectively for the outer (3) and inner
(4) stack.
rotor accelerates fast enough, it will not collide with
the stator and such resonance will be acceptable. Fi-
nally, the dislocation between the concentric stacks
of bearing II induces a downward axial bias force of
21.2N to the rotor. This downward force is used to
cancel part of the upward force from bearing I. By
doing so, the total upward force that the active bearing
has to counteract is not excessive and thus its power
consumption at steady state is reduced.
4 MODELING, IDENTIFICATION,
AND CONTROL OF THE
ACTIVE MAGNETIC BEARING
In the active magnetic bearing, if the magnetic flux
leakage, fringing flux, and the magnetic reluctance in
the iron core are ignored, one can derive the following
magnetic force equation:
F
m
=
−A
2
[µ
0
Ni+ B
r
l/µ
r
]
2
2µ
0
(z+ l/µ
r
)
2
(1+ A
2
/A
1
)
(6)
where F
m
is the downward magnetic force generated,
µ
0
is the air permeability, µ
r
and B
r
are respectively
the relative permeability and the remanence magnetic
flux density of the permanent magnet, z is the air gap,
µ
0
is the air permeability, i is the coil current, N is
the number of coil turns, l is the thickness of the per-
manent magnet, A
1
and A
2
are respectively the areas
of the inner(circular) and outer(annular) pole faces.
Table 2 lists the numerical values of the relevant pa-
rameters for the active magnetic bearing. Comparing
the magnetic force computed by (6) with the finite-
element simulations, it can be found that the theo-
retical equation tends to overestimate the magnetic
force because it ignores the magnetic flux leakage and
fringing flux associated with the permanent magnet.
To make a more accurate force prediction, one can in-
troduce a correction factor η in which ηl replaces l in
(6) as the equivalent thickness of the permanent mag-
net. By choosing η to be 0.946, Figure 7 shows that
the theoretical equation matches the finite element re-
sults better with maximum error less than 3%.
4.1 Linear Model and Identification
To facilitate the subsequent linear control design, the
nonlinear force equation (6) with the correction factor
is linearized around i = 0, and z = z
0
, where z
0
is the
nominal air gap. The linearization results in
F
m
≈ −k
i
δi+ k
s
δz−F
b
(7)
ICINCO2015-12thInternationalConferenceonInformaticsinControl,AutomationandRobotics
506