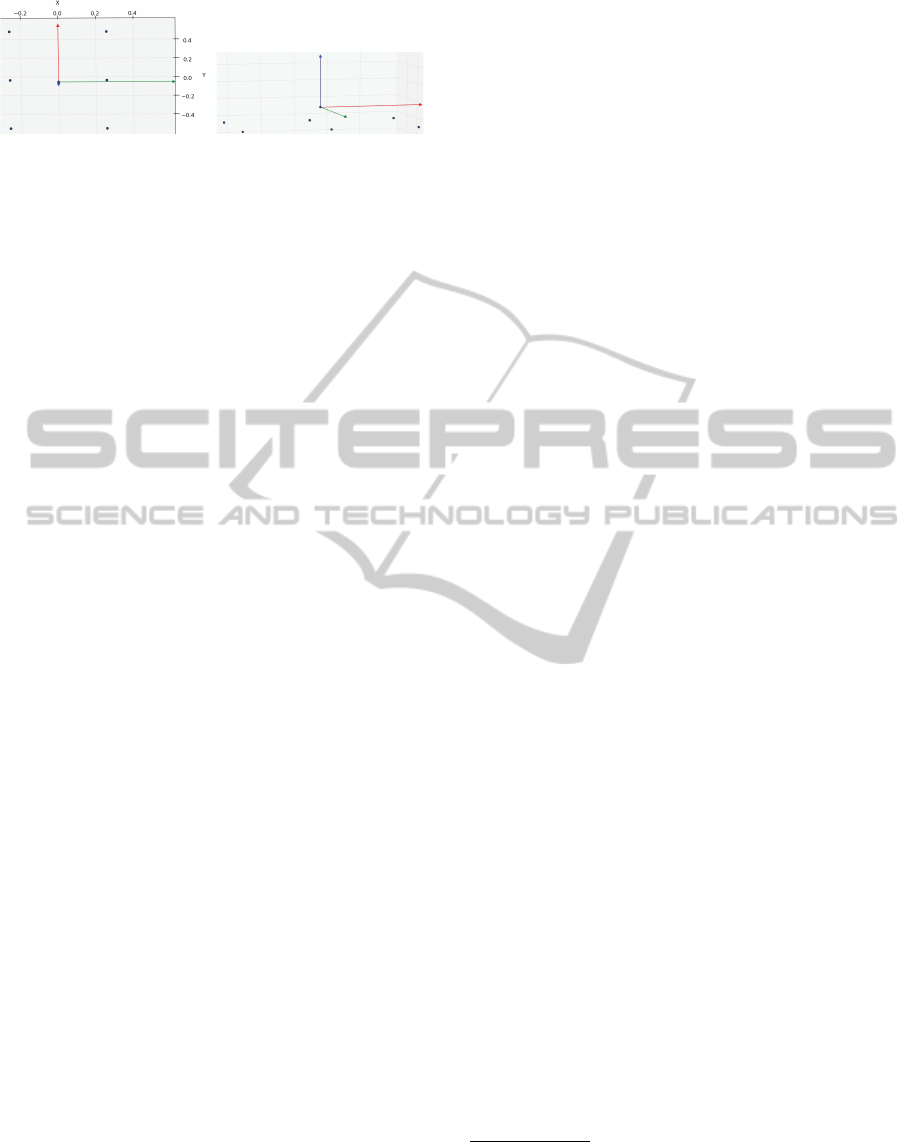
Figure 3: Representation of the mobile vehicle and its ref-
erence frame. Fig. 3 (a) illustrates the top view of the rep-
resentation of the robot and Fig. 3 (b) shows a perspective
of the representation. In this case an approximation of the
representation of the robot in Fig. 2 is shown.
domly defined using the RAPOSA-NG. This assign-
ment must take into consideration the traversability
of the terrain. To solve the optimization problem we
tested two well known numerical constrained opti-
mization algorithms: Constrained Optimization BY
Linear Approximation and Sequential Least SQuares
Programming. The COBYLA algorithm (Powell,
2007) is based on linear approximations to the objec-
tive function and each constraint, where the derivative
of the objective function is not known. The SLSQP
algorithm (Kraft, 1988) allows us to deal with con-
strained minimization problems by sequentially min-
imizing the quadratic error of the result. It is possible
to require a level of accuracy from both algorithms.
After testing both, the COBYLA and the SLSQP, we
determined the latter is the fastest and more reliable
when limiting the error to the set value. Regarding
the path planning problem itself, the FMM is avail-
able in an extension module (scikit-fmm), from the
python libraries. When creating a path using RRTs
we modified some lines of code written by LaValle
(LaValle, 2006), changing the criteria by which the
nodes are chosen or pruned as explained before.
5 TEST SCENARIOS
The proposed approach was tested /simulated, using
the process explained in section 3, considering three
possible scenarios which presented a variety of fea-
tures that we considered relevant for the purpose mis-
sion of the RAPOSA-NG. The four chosen test sce-
narios, itemized below, intend to verify the robot’s
capabilities to overcome obstacles and hurdles that
could be present on a real life search and rescue
(SAR) scenario:
1. A representation of a mountain, Fig.4, area syn-
thetically generated, the surface is rendered from
a grey scale image that represents an elevation
map. This is a mountain like scenario, exemplary
of the typical scenario were outdoor unmanned
vehicles operate;
2. An image of irregular polygons at different
heights emulating debris, Fig.6. The sharp edges
of the debris like bricks or concrete walls are sim-
ulated as irregular polygonal steps;
3. A RoboCup Robot Rescue arena
1
Fig. 8. This
scenario, although a physical simulation of an ac-
tual SAR environment, is where, typically, these
robots are tested through a series of task fulfil-
ment, and competitions;
4. A valley like scenario where the least effort path
is clearly somewhere between the two mounts.
The maps can be scaled up/down for our convenience,
so that the scale of the robot is not too small. The first
map is 248x248 in a total of 61504 of cells to be pro-
cessed, the second and forth are 491x491 in a total
of 241081 cells and the third has a total of 117572
cells. Processing the entire surface from Fig.4 we ob-
tain the equivalent to a energy potential information
that can be depicted as seen in Fig.5. Fig.4 shows
the surface as it exists, in shape, but it is scaled down
so that the highest peak is not bigger than the robot’s
length. Fig.5 shows the same physical space as the
later but it is already processed to allow path planning
to occur. Notice that, the surface is as if tilted to the
right, this is because the goal was set on the right side
of the map and it is the point with the lowest poten-
tial energy. The represented peaks are softer than the
Fig.4 and possibly not even in the same place because
they do not represent elevation but a higher difficulty
for the autonomous vehicle maintain a stable position
or traverse. The same reasoning applies to the maps
in Fig.6 and 8 and resulting energy potential in Fig.7
and 9 respectfully. The highest peaks seen in Fig.7
are representing obstacles, points in space where the
robot is incapable to travel trough. The cost at those
points is so high (the peaks are scaled down to bet-
ter visualize the results), the path will never include
them. Fig.8 represents a complex environment and
with a variety of obstacles as walls and steps. Tak-
ing the world’s representation as in Fig.5, 7 or 9 the
optimal path to the goal corresponds to the gradient
descent from a given initial position and a path can
be determined from anywhere on the map. From the
representation of the potential we obtain the optimal
path, for the given cost map Fig.10 and Fig.11. The
path represented in Fig.10 was obtained from the rep-
resentation of the world depicted in Fig.5 and Fig.11
from Fig.7. The maps show isochrone lines, which
1
This elevation map is derived from running octomap
in simulation (ROS/Gazebo) over the RoboCup Robot
Rescue arena, http://www.isd.mel.nist.gov/projects/USAR/
arenas.htm. It was obtained by an autonomous robot with
a depth camera and SLAM methods (Kohlbrecher et al.,
2013)
APhysics-basedOptimizationApproachforPathPlanningonRoughTerrains
263