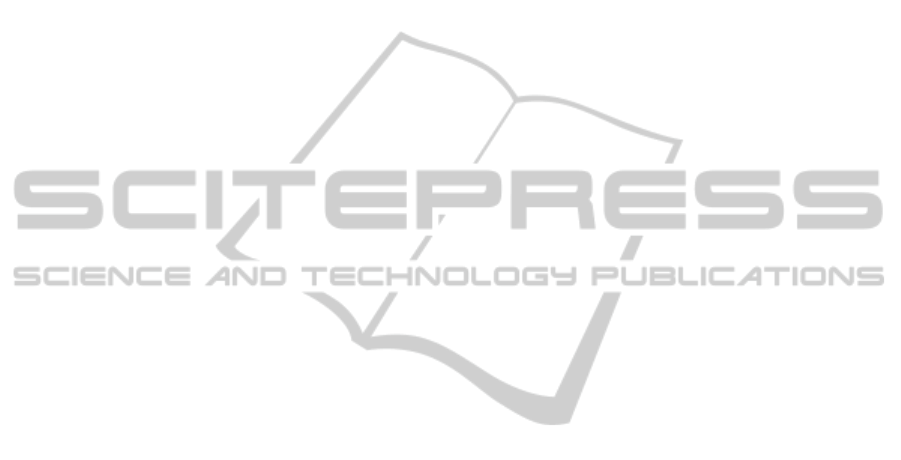
simulations have been carried out at both kT=0 and
at values 1>kT>0, under periodic boundary
conditions. It is to be noted here that the term kT in
simulation replaces both the Boltzmann constant and
the temperature as an assumed combined product.
The term kT generally takes a value between 0 and 1
and represents the thermal energy of simulation. It is
analogous to the thermal energy of experimental
systems but not directly related (Janssens et al.,
2007). Just as in the real world, when a phase
change is imminent when a metal is heated beyond a
critical temperature, there is a critical value for the
term KTs, beyond which the microstructure
evolution through simulation seizes and a disordered
state sets in.
3 EXPERIMENTAL HARDWARE
AND SOFTWARE
All the experiments were carried out on a specially
built system with 16 GB ram, INTEL CORE 15-
2500K-6M-3.3 GHZ Processor and a Asus P8H67-
MLE Motherboard B3 Model. The code was written
on a Java Core Eclipse platform and close attention
was paid to memory management since very large
arrays were run. The code invokes generation of
massive random numbers which was achieved
through the JAVA virtual machine (JVM).
Random number generation plays a crucial role
in the process of computer simulation of grain
growth. Since computers are basically calculating
machines, and use deterministic algorithms to
generate random numbers, they basically produce
pseudo random numbers, unless and until they are
accessing some external device such as a gamma ray
counter or a clock. The very foundation of Monte
Carlo method lies on generation of robust and long
range random numbers, especially since certain
simulation trials have to last millions of Monte
Carlo Steps, preferably without repeating the
sequence. The JAVA virtual machine (JVM) has a
reliable random number generator based on linear
congruential algorithm and can produce billions of
random numbers (2
48
, to be precise) on the trot,
before it repeats the sequence.
4 RESULTS AND DISCUSSIONS
In this work, Al-4% Cu samples, initially hot
extruded to about 50%, were annealed at a
recrystallization temperature of 480
0
C, and held for
various durations such as 1, 2, 3, 4 and 10 hours.
They were then polished with emery sheets (with
grit sizes 80 – 1200) and etched with Keller’s
reagent (2.5% HF, 1.5% HNO
3
, 1% HCl, rest
ethanol) for 10 seconds. They were then washed in
running water and dried with methanol and hair
dryer. The microstructures were observed under a
microscope and snapshots were taken, at
magnifications of 50x, 100x, 200x, etc. Al-4% Cu
was selected because upon annealing the alloy
precipitates fine second phase particles of CuAl
4
which pin grain boundaries and stagnate the average
grain size.
On the other hand, simulations were run on
various matrix sizes with different quantities of
second phase particles randomly interspersed to
represent polycrystalline materials. The matrices
were processed with millions of steps of the
Metropolis algorithm simulating grain growth which
takes place in metals during annealing. Simulated
grain structures were captured at different stages of
grain growth evolution of various matrix samples
and selected portions of these microstructures have
been used for pictorial comparisons with real
microstructures. Pictures from stagnation stage,
which refers to a stage where no more evolution is
possible due to grain growth inhibition by second
phase particles, have also been used in the
comparison.
Table 1 shows pictorial comparisons between
various real microstructures on the left hand side,
and, the simulated microstructures on the right hand
side. The first set of pictures shown in Figure 1(a)
and 1(b) allows for a comparison between an Al-
4%Cu alloy annealed at 480
0
C for one hour, and
photographed at 100x magnification, with a portion
of the simulated microstructure evolved with a
square matrix of size (N) 1000 x 1000, a Q-state
value of 16, with zero percent of second phase
particles representing a pure metal and finally a
certain stage in grain growth as represented by the
number of Monte Carlo steps of 50,000.
Figures 2(a) and 2(b) show the comparison
between the same alloy annealed for two hours with
a digital microstructure having parameters N=1000,
Q=64, f=0.001, kT=0.5 and MCS=1,394,926 (at
stagnation). The selected crystal surface is based on
1000 x 1000 matrix with an assumed 64 (Q) grain
orientations. A value of f=0.001 means that a
surface fraction representing 0.1% of the surface of
the microstructure is occupied by second phase
particles each having a size of one unit being
randomly distributed throughout the matrix. These
static particles are shown as tiny dark spots in the
SIMULTECH2015-5thInternationalConferenceonSimulationandModelingMethodologies,Technologiesand
Applications
120