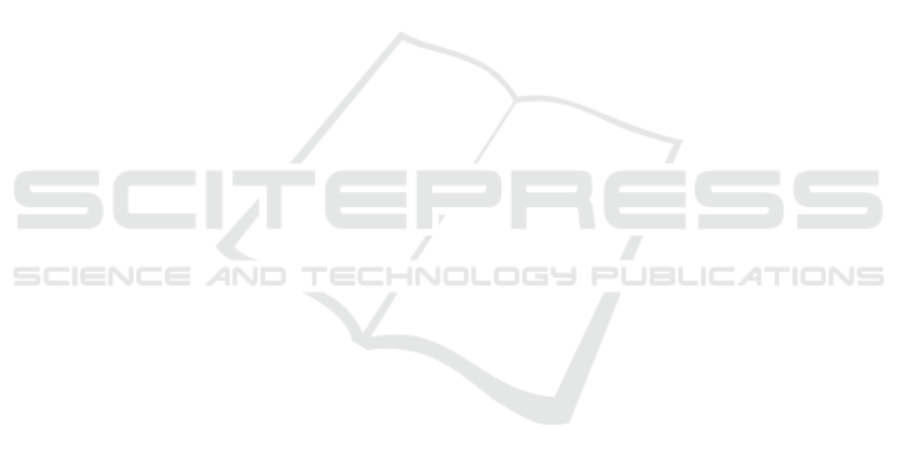
Inverse Kinematics of a Redundant Manipulator based on Conformal
Geometry using Geometric Approach
Je Seok Kim, Jin Han Jeong and Jahng Hyon Park
1
Department of Automotive Engineering, Hanyang University, Seoul, Korea
Keywords: Geometric Approach, Inverse Kinematics Analysis, Redundancy, Conformal Geometry, Joint Angles.
Abstract: This paper describes a geometrical approach for analysing the inverse kinematics of a 7 Degrees of Freedom
(DOF) redundant manipulator. The geometric approach is desirable since it provides complete and simple
solutions to the problem and determines the relationship between the joints and the end-effector without
iterative process. This paper introduces the approach to solve kinematic solution of 7 DOF in an intuitive way
using conformal geometric approach step by step. We finally present the comparison with pseudo inverse
solution which is the most well-known method in redundant manipulator kinematic problem at the same
simulation environment.
1 INTRODUCTION
A manipulators are designed to have the Degrees of
Freedom (DOF) only needed in the configuration
space, but have inherent problems, e.g., it is difficult
to avoid singularity or obstacles in the operating
space and lack of the adaptation to changes in
operating environments. Therefore, many studies are
conducted on a redundant manipulator in the form of
human arm with redundancy that uses remaining
DOF after performing given work to perform
additional work.
Generally, velocity kinematics algorithm and
geometric approach are used to analyse the inverse
kinematic of redundant manipulators. The velocity
kinematics algorithm (Whitney 1972, Liegeois 1977,
Baillieul 1985) is based on the generalized pseudo-
inverse to calculate the velocity transformation from
Cartesian to joint space. Pseudo-inverse of the
Jacobian matrix provides a possibility to solve for
approximate solutions. There is no exact velocity
solution for redundant robot. It increases the
possibility of singularity and causes cumulative errors
due to repeated integration of the value of speed. In
terms of the geometric approach, Tolani (Tolani,
Goswami et al. 2000) made a geometric approach by
the shape of 7-DOF manipulator into three joints of
shoulder, elbow, and wrist to express the movement
of human arm naturally in computer graphics, but it
was difficult to express the entities such as spheres
and circles in 3D spaces. This paper attempted to
reanalyse the study of Tolani in conformal geometry.
Conformal geometry is a mathematical language
that integrates various mathematical theories, such as
Projective Geometry, Quaternion, and Lie Algebra
for easy understanding and has been widely used
since the 1960s when Hestenes applied geometric
algebra to physics. Therefore, it is spotlighted as a
new method in robotics (Hildenbrand, Zamora et al.
2008, Aristidou and Lasenby 2011), computer vision
(Bayro-Corrochano, Reyes-Lozano et al. 2006,
Debaecker, Benosman et al. 2008, Ishida, Meguro et
al. 2013), and computer graphics (Wareham,
Cameron et al. 2005, Roa, Theoktisto et al. 2011).
Conformal geometry easily expresses intuitively and
mathematically the geometric entities, such as
spheres and circles, from geometric perspectives to
allow real-time calculations. For more details on
conformal geometry, refer to the paper by
Hildenbrand
(Hildenbrand 2012).
The inverse kinematics analysis of manipulators
in conformal geometry has already been conducted by
Hildenbrand (Hildenbrand, Lange et al. 2008)
and
Zamora (Zamora and Bayro-Corrochano 2004). They
used manipulators with 5- to 6-DOF only suitable for
given configuration space and the analysis was
possible only with simple geometric entities.
However, 7-DOF manipulator has redundancy and it
is necessary to optimize cost function.
Recently, many studies are conducted about cost
function in the inverse kinematics analysis of
179
Seok Kim J., Han Jeong J. and Hyon Park J..
Inverse Kinematics of a Redundant Manipulator based on Conformal Geometry using Geometric Approach.
DOI: 10.5220/0005535001790185
In Proceedings of the 12th International Conference on Informatics in Control, Automation and Robotics (ICINCO-2015), pages 179-185
ISBN: 978-989-758-122-9
Copyright
c
2015 SCITEPRESS (Science and Technology Publications, Lda.)