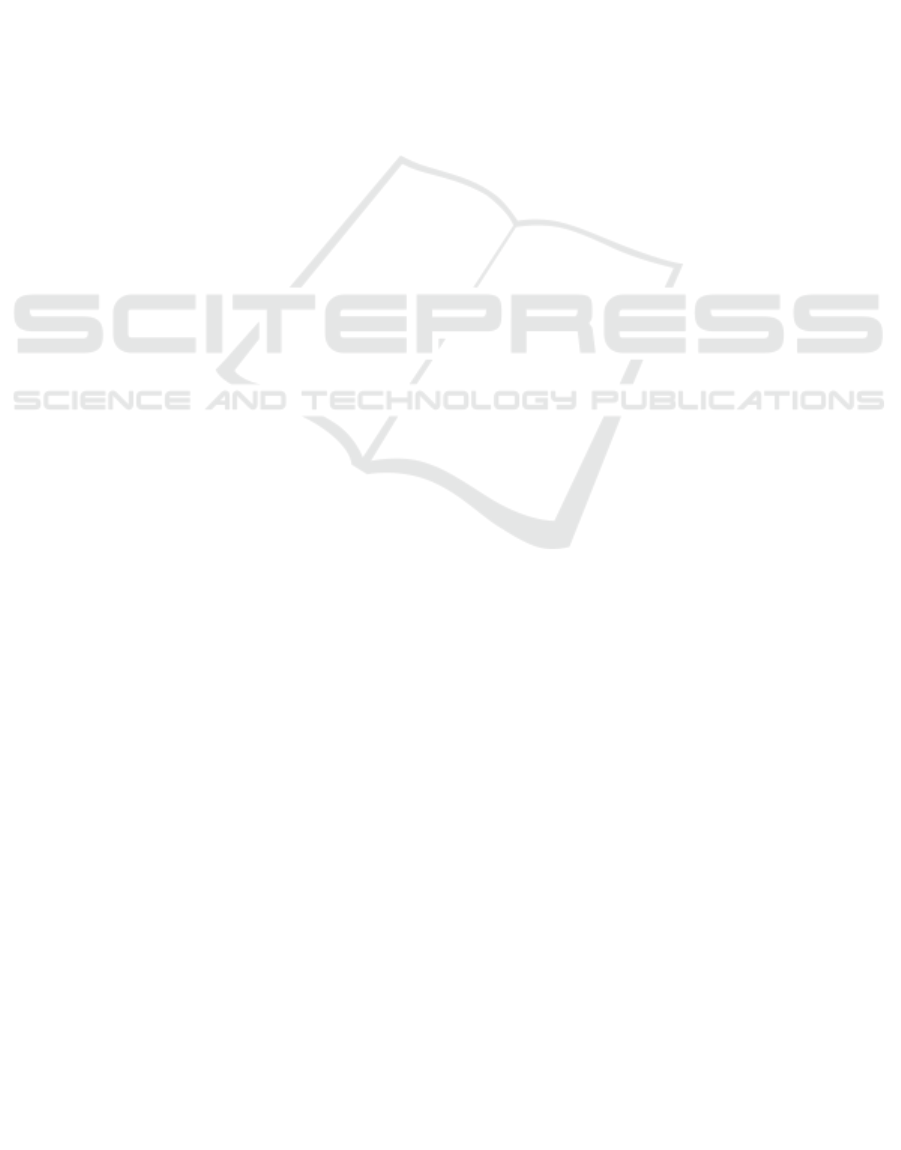
Guaranteed Control of a Robotic Excavator During Digging Process
Alexander Gurko
1
, Oleg Sergiyenko
2
, Juan Ivan Nieto Hipólito
2
, Igor Kirichenko
1
,
Vera Tyrsa
3
and Juan de Dios Sanchez Lopez
4
1
Kharkov National Automobile and Highway University, Kharkov, Ukraine
2
Autonomous University of Baja California, Mexicali, Baja California, Mexico
3
Kharkiv Petro Vasylenko National Technical University of Agriculture, Kharkov, Ukraine
4
Autonomous University of Baja California, Ensenada, Baja California, Mexico
Keywords: Robotic Excavator, Guaranteed Control, Multiple Identification, R-functions.
Abstract: Automation of excavators offers a promise for increasing productivity of digging. At the same time, it’s a
highly difficult issue due to presence of various nonlinearities and uncertainties in excavator mechanical
structures and hydraulic actuators, disturbance when a bucket contacting the ground etc. This paper
concerns the problem of robust trajectory tracking control of an excavator arm. To solve this problem, the
computed torque control with the guaranteed cost control is considered. The mathematical tool of R-
functions as an alternative to the linear matrix inequality approach to constructing information sets of an
excavator arm state is used. Simulation results and functional ability analysis for the proposed control
system are given.
1 INTRODUCTION
Hydraulic excavators are used at a wide variety of
sites from civil construction to disaster elimination,
therefore efficiency and productivity increase of
these machines is a highly important problem. One of
the ways to solve the problem is to design a robotic
excavator. In addition to the increase of productivity,
the automation of excavators reduces loads on an
operator, improves his safety and makes it possible to
work in places that are inaccessible for humans.
However, robotic excavators are created
extremely slowly due to high dynamic loads during
the bucket and soil interaction, which is difficult to
predict, and other uncertainties such as backlashes
between machine parts, variability of a fluid
viscosity in hydraulic actuators, oil leaks, etc.
There are a lot of papers focused on the robotic
excavator design and creation of digging process
control system. For example, some works (Koivo et
al, 1996; Gao et al., 2009; Gu et al., 2012) describe
PD and PID controllers application to control a
robotic excavator arm movement. Besides, in one of
the papers (Gu et al., 2012) a proportional-integral-
plus (PIP) controller and a nonlinear PIP controller
based on a state-depended parameter model structure
were proposed.
In one of the works (Yokota et al., 1996) a
disturbance observer in addition to PI-controller to
control a mini excavator arm was proposed. Along
with the computed torque control, the adaptive and
robust controls of the excavator arm were designed in
(Yu et al., 2010).
In (Bo et al.) a fuzzy plus PI controller with fuzzy
rules based on the soft-switch method was
developed. In (Zhang et al., 2010) an adaptive fuzzy
sliding mode control to realize the trajectory tracking
control of an automatic excavator was designed. Two
controllers based on fuzzy logic, including the fuzzy
PID controller and fuzzy self tuning with neural
network, were developed in (Le Hanh et al., 2009) to
control the electro hydraulic mini excavator. In
(Choi, 2012) the Time-Varying Sliding Mode
Controller with fuzzy algorithm was applied to the
tracking control system of the hydraulic excavator.
Time-delay controllers were proposed for motion
control of a hydraulic excavator arm in (Chang and
Lee, 2002; Vidolov, 2012).
All these works have made a valuable
contribution to solve the problem of robotic
excavator creating, but a commercial fully robotic
excavator will probably appear not soon due to the
mentioned above factors.
In this paper we propose the guaranteed cost
control for the trajectory tracking control of the
52
Gurko A., Sergiyenko O., Hipólito J., Kirichenko I., Tyrsa V. and Lopez J..
Guaranteed Control of a Robotic Excavator During Digging Process.
DOI: 10.5220/0005536000520059
In Proceedings of the 12th International Conference on Informatics in Control, Automation and Robotics (ICINCO-2015), pages 52-59
ISBN: 978-989-758-123-6
Copyright
c
2015 SCITEPRESS (Science and Technology Publications, Lda.)