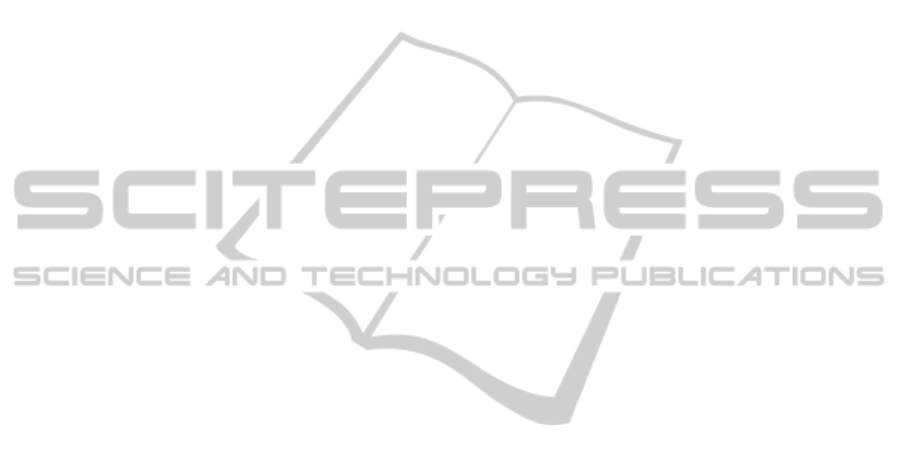
at constant speed and frequency is used during
compaction of the pavement along a pre-determined
path. However, material and environmental
variability results in non-uniform compaction of the
mix. Investigations carried out during field
compaction have shown as much as 2% variation in
density in locations less than a meter apart from each
other (Beainy et al., 2011). Intelligent Compaction
(IC) technologies attempt to address this variability in
compaction quality by providing continuous real-
time quality control by monitoring the level of
compaction of the pavement and adjusting the amount
of compaction energy applied by the roller in order to
obtain uniform density.
IC solutions have been developed by Original
Equipment Manufacturers (OEMs) with the goal of
providing real-time estimation of the level of
compaction (Arasteh, 2007; Briaud and Seo, 2003;
Rakawoski, 2008). However, these approaches were
hampered by limited understanding of the roller
dynamics and the lack of adequate mathematical
models and have met with limited success.
Several attempts have been made in recent years
to study the dynamical interaction between the roller
and the underlying material. Huerne (2004)
developed a constituent model of asphalt mixture
using critical state theory adopted from the soil
mechanics and used this model to study compaction
using a static roller. Koneru et al. (2008) developed a
constitutive model using a thermodynamic
framework to study the compaction of asphalt mixes.
In this method, the notion of multiple natural
configurations assumed by a body was used to
analyze compaction of asphalt mixes using laboratory
equipment. Masad et al (2010) used a
thermodynamics based nonlinear viscoelastic model
of the asphalt mix. A finite element based numerical
scheme was developed to simulate the response
during laboratory and field compaction. The
developed model was able to predict the influence of
material properties such as binder viscosity,
aggregate shape characteristics, and aggregate
gradation during the static compaction of asphalt
specimen. Chen (2011) formulated a Discrete element
Method based model of asphalt compaction taking
into account the viscoelastic property of the mix as
well as the slippage and interlocking of the aggregates
during compaction. While these results are
encouraging, significant work is still required to
develop a simple and computationally tractable
model to implement and study real-time closed loop
control algorithms.
Researchers have also studied analytical models
such as Maxwell, generalized Maxwell, Kelvin–
Voigt, generalized Kelvin, Huet–Sayegh, and Burger
models to represent asphalt pavement as a
combination of simple mechanical elements such as
spring and damper (Nillson et al., 2002; Pronk, 2005;
Xu and Solaimanian, 2009). These models are used
mostly to study the long term behavior of the
pavement under traffic loads. Their ability in
representing the pavement during field compaction is
not studied. Among the analytical models, Burger’s
model is simple and can represent the viscoelastic
behavior of an asphalt pavement (Liu and You, 2009;
Liu et al., 2009). Beainy et al. (2013) used Burger’s
model to represent the dynamical properties of
asphalt pavement in his model for studying the
asphalt-roller interaction during compaction. The
model captures the coupled dynamics of the static
vibratory interaction between the roller and asphalt
pavement in the direction normal to the surface of the
pavement. The movement of the roller along the
pavement and the vibration of the roller drum in the
longitudinal or lateral direction are not taken into
account. Imran et al. (2014) incorporated the motion
of roller to the Beainy’s model to demonstrate its
applicability in emulating the field compaction
process that uses a conventional rolling pattern. In
their study, the asphalt pavement was considered to
be a collection of small independent blocks of
Burger’s material. At any given time, the roller was
assumed to be interacting with one set of blocks. This
model also was limited to study the vibration in the
vertical direction only. The effect of shear resistance
of the asphalt pavement was not taken into account.
This paper extends the work of Imran et al. (2014) by
incorporating the effect of shear strength between the
adjacent blocks in the longitudinal direction. The
model is aimed to capture the dynamics of the
vibratory compaction in both the vertical and the
longitudinal direction.
2 DEVELOPMENT OF THE
MODEL
The work of Beainy et. al (2013) and Imran et. al
(2014) is extended in this study for the development
of a model that can represent the asphalt-roller
interaction during compaction process. In this model,
the vibratory roller drum and the underlying
pavement are considered to form a coupled system.
The roller is considered to be in continuous contact
with the asphalt pavement. The dynamics due to
bouncing or loss of contact is not taken into account.
The vibration dynamics in both the vertical and
ICINCO2015-12thInternationalConferenceonInformaticsinControl,AutomationandRobotics
534