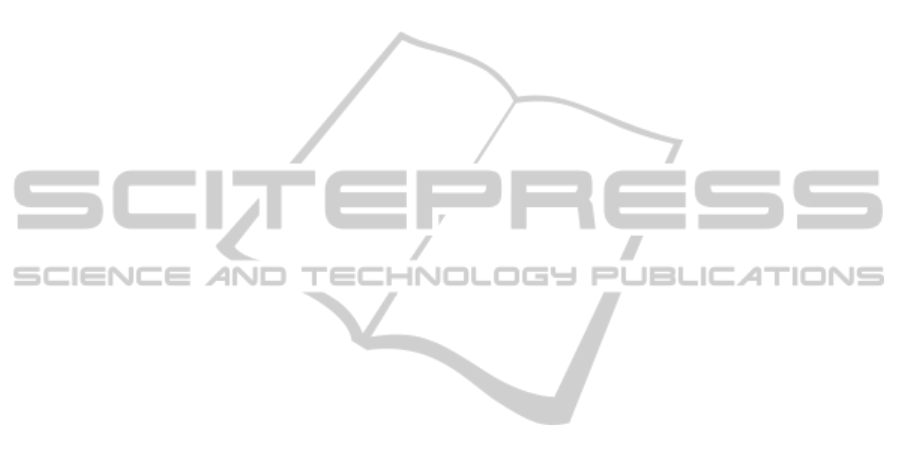
[]
2/1
2
)(min s
i
j
i
j
αωξ
<
()
[]
2/1
132
12
i
f
i
f
i
f
KKK −<
(34)
When the trajectory penetrates S
q
(or S
F
), the
damping coefficients
i
f
i
j
K
2
,
ξ
are increased (Shilling,
1993), (Ivanescu and Stoian, 1998):
[]
2/1
2
)(max s
i
j
i
j
αωξ
>
()
[]
2/1
132
12
i
f
i
f
i
f
KKK −>
(35)
In the second phase, on the last trajectory
segment, the system develops towards the origin,
directly, on the switching line S
q
(or S
F
).
8 CONCLUSIONS
This paper presents a control procedure and a
control algorithm with two levels to solve the
control problem of a cooperating multi-arm robotic
system like a gripper with n fingers manipulating a
usual object. The control system is a hierarchical
system. The problems of the inter-coordination and
the force distribution are decided by the upper-level
coordinator which brings together all the appropriate
information. This information is directed towards the
n lower-level subsystems. The local control is solved
by assigning the local controllers based on the
inverse model method.
A control algorithm is also presented. This
allows for the robotic structure, under the terms of
the actuator blocking occurrence during the working,
either a correct positioning (if it is possible) or a
positioning in an acceptable proximity of the desired
co-ordinates by minimising the movements (by the
adequate commands to the functional elements).
A synthesis of the commands is proposed. First,
a workspace analysis is made and then an algorithm
for the actuators in the terms of a good working
(finding the optimal motions) is presented in terms
of the blocking or unblocking of some robotic
segments.
ACKNOWLEDGEMENTS
This research work is supported by the Project no.
PO9003/1138/31.03.2014, Romanian Government
under the Sectorial Operational Program "Economic
Competitiveness Growth".
REFERENCES
Beni, G., Hackwood, S., 1985. Recent advances in
Robotics, Willey-Interscience. New York.
Cheng F.T., Orin D.E., 1991. Optimal Force Distribution
in Multiple-Chain Robotic Systems. In IEEE Trans. on
Sys. Man and Cyb., vol. 21, pp. 13-24.
Cheng F.T., Orin D.E., 1991. Efficient Formulation of the
Force Distribution Equations for Simple Closed-Chain
Robotic Mechanisms. In IEEE Trans on Sys. Man and
Cyb., vol. 21, pp. 25-32.
Cheng F.T., 1995. Control and Simulation for a Closed
Chain Dual Redundant Manipulator System. In
Journal of Robotic Systems, pp. 119-133.
Craig, J. J., 1990. Introduction to Robotics, Addison-
Wesley Publishing Company. New York.
Iancu, E., Vinatoru, M., 1999. Fault detection and
isolation, SITECH. Craiova.
Ivanescu, M., Stoian, V., 1998. A Control System for
Cooperating Tentacle Robots. In Proceedings of the
IEEE International Conference on Robotics and
Automation, vol. 2, pp. 1540-1545.
Khatib D.E., 1996. Coordination and Decentralisation of
Multiple Cooperation of Multiple Mobile Manipula-
tors. In Journal of Robotic Systems, 13 (11), 755-764.
Luck, C.L., Lee, S., 1995. Redundant Manipulators under
Kinematic Constraints: A Topology Based Kinematic
Map Generation and Discretization. In Proceedings of
the IEEE International Conference on Robotics and
Automation, vol. 2, pp. 2496-2501.
Mason, M. T., 1981. Compliance and Force Control. In
IEEE Trans. Systems Man Cyb., No. 6, pp. 418-432.
Shilling, J. S., 1993. Fundamentals of Robotics. Analysis
and Control, Prentice Hall. London.
Vinatoru, M., Iancu, E., Patton, R.J., Chen, J., 1998. Fault
Isolation Using Inverse Sensitivity Analysis. In Prooc.
of Internat. Conference on Control'98, pp. 964-968.
Zheng Y.F., Luh J.Y.S., 1988. Optimal Load Distribution
for Two Industrial Robots Handling a Single Object.
In Proc. of IEEE Int. Conf. Rob. Autom., pp. 344-349.
Wang L.C.T., 1996. Time-Optimal Control of Multiple
Cooperating Manipulators. In Journal of Robotic
Systems, pp. 229-241.
ICINCO2015-12thInternationalConferenceonInformaticsinControl,AutomationandRobotics
288