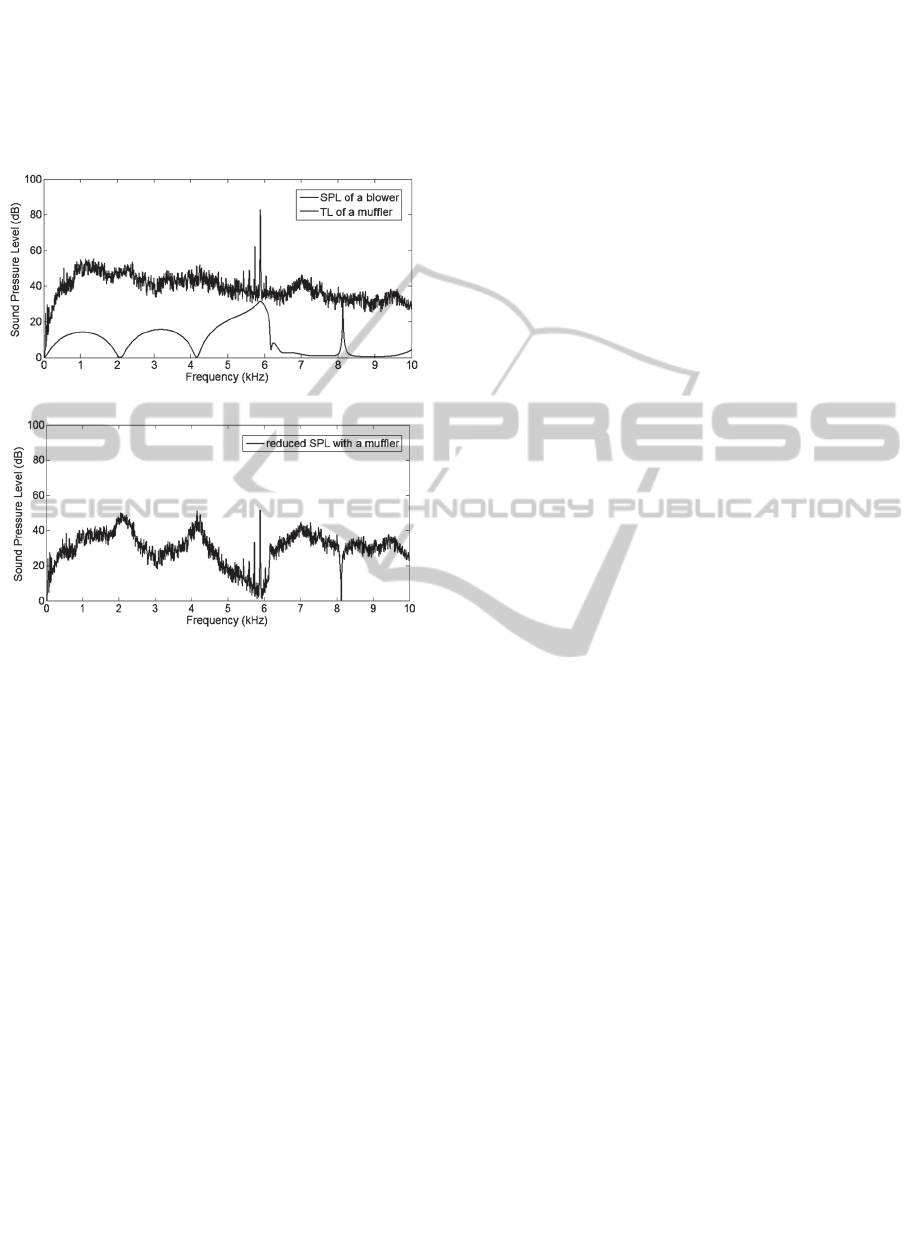
BPF 5800 Hz in the noise spectrum of the
regenerative blower as shown in Figure 4.
4 RESULTS
(a)
(b)
Figure 7: (a) blower noise spectrum and TL of the
designed perforated muffler and (b) reduced noise
spectrum.
The regenerative blower generates the noise of
overall sound pressure level (SPL) 84 dB(A) with
the frequency spectrum shown in Figure 7(a), that
has two kinds of noise components such as discrete
frequency noise at BPF 5800Hz and the broadband
noise distributed over wide frequency range. In
order to effectively reduce the discrete frequency
noise at BPF, the perforated muffler with the
porosity σ 22% is designed and attached. TL of
the muffler is evaluated over the frequency range
between 0 and 10kHz is as shown in Figure 7(a).
The overall SPL of 84 dB(A) is expected to be
reduced to 72 dB(A) by attaching the perforated
muffler as shown Figure 7(b) that represents the
reduced noise spectrum by attaching the perforated
muffler to the regenerative blower.
5 CONCLUSIONS
A perforated muffler has been designed to reduce a
high noise level that is generated from a regenerative
blower used in fuel cell applications. In order to
effectively reduce discrete frequency noise
component at high frequency 5800 Hz, the design
parametric study has been performed using transfer
matrix method and FEM. It is implemented to design
the perforated muffler that effectively reduces the
high noise level. The overall SPL of 84 dB has been
expected to be reduced to 72 dB by attaching the
perforated muffler. Further research is expected to
experimentally verify the design results and to
evaluate the contribution of porous material inserted
inside the coaxial duct of the perforated muffler to
more reduction of the blower noise.
ACKNOWLEDGEMENTS
This work was supported by the Development of the
Regenerative Blower for fuel cell application of the
Korea Institute of Energy Technology Evaluation
and Planning (KETEP) grant funded by the Korea
government Ministry of Knowledge Economy.
REFERENCES
Lee, C., Kil, H. G., Kim G.C., Kim, J. G., Ma, J. H.,
Chung K. H., 2013. Aero-acoustic Performance
Analysis Method of Regenerative Blower, Journal. of
Fluid machinery (in Korean), 16(2).
Crocker, J. W., M. J.,1978. Analysis of concentric
resonators having partitioned cavities, Journal of
Acoustical Society of America, 64(1).
Sullivan, 1979. A method for modelling perforated
muffler components. I. Theory, Journal of Acoustical
Society of America, 66(3).
Munjal, M. L., 1987. Acoustics of ducts and mufflers with
application to exhaust and ventilation system design,
John Wiley & Sons.
Wu, T. W., Wan. G. C., 1996. Muffler performance
studies using a direct mixed-body boundary element
method and a three-point method for evaluating
transmission loss. ASME Transaction, Journal of
Vibration and Acoustics, 118.
Saf., O., Erol, H., 2010, On acoustics and flow behavior of
the perforated mufflers, 17
th
International Congress
on Sound & Vibration.
Erikson, L. J., 1980. Higher order mode effects in circular
ducts and expansion chambers, Journal of Acoustical
Society of America, 66(3).
Mechel, F. P., 2008. Formulas of Acoustics, Springer, 2
nd
edition.
SIMULTECH2015-5thInternationalConferenceonSimulationandModelingMethodologies,Technologiesand
Applications
492