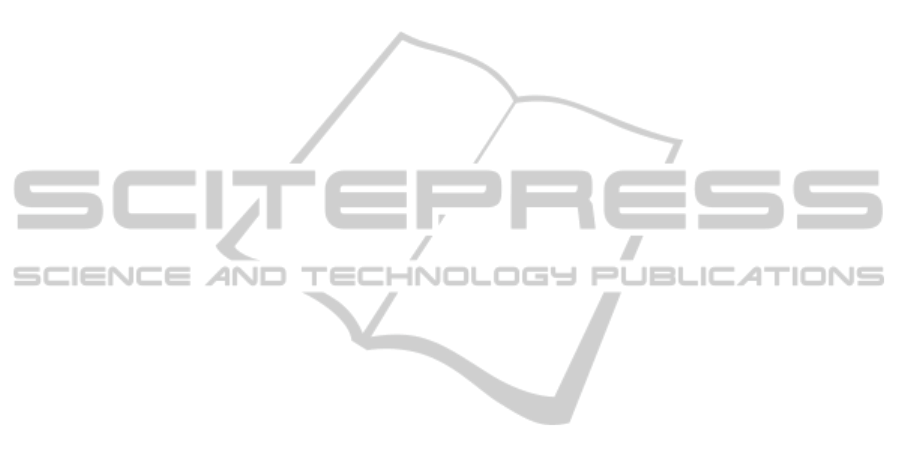
be improved further. Screenshots of the application
(see Figure 7) show the perspective of the tablet as
well as the appearance of the interface before and af-
ter the button is pressed to start the control of the ball.
6 CONCLUSIONS
This paper presented the development of a vision-
based approach to control a ball and beam test-bed
using the camera onboard a tablet to provide mea-
surements as the tablet is pointed at the test-bed from
an arbitrary perspective. A touch-based user inter-
face with augmented reality allows users to interact
with the test-bed in real-time as the system is being
controlled. Results from experiments validate the use
of tablets as portable, hand-held, vision-based sensor,
estimation, and control components in a wireless net-
worked control system for plants whose states can be
estimated from vision-based measurements.
ACKNOWLEDGEMENTS
This work is supported in part by the National Science
Foundation awards RET Site EEC-1132482, GK-12
Fellows DGE: 0741714, and DRK-12 DRL: 1417769,
and NY Space Grant award 48240-7887. The authors
thank Anthony Brill and Sai Prasanth Krishnamurthy
for their support.
REFERENCES
Baggio, D. (2012). Mastering OpenCV with Practical Com-
puter Vision Projects. Packt Publishing Ltd.
Berenguel, M., et al. (2004). An artificial vision-based con-
trol system for automatic heliostat positioning offset
correction in a central receiver solar power plant. So-
lar Energy, 76(5):563–575.
Bol
´
ıvar, C. and Beauchamp, G. (2014). Modelling the
ball-and-beam system from newtonian mechanics and
from lagrange methods. In Proc. Latin American and
Carribbean Conference on Engineering and Technol-
ogy, page 176.
Burschka, D. and Hager, G. (2001). Vision-based control
of mobile robots. In IEEE Int. Conf. Robotics and
Automation, volume 2, pages 1707–1713.
Dadios, E.P., et al. (2000). Vision guided ball-beam balanc-
ing system using fuzzy logic. In IEEE Conf. Industrial
Electronics Society, volume 3, pages 1973–1978.
Das, A.K., et al. (2002). A vision-based formation control
framework. IEEE Trans. Robotics and Automation,
18(5):813–825.
Desai, A., et al. (2013). Stabilization and control of
quad-rotor helicopter using a smartphone device.
IS&T/SPIE Electronic Imaging, 8662(8):1–9.
El-Gaaly, T., et al. (2013). Visual obstacle avoidance for
autonomous watercraft using smartphones. In Au-
tonomous Robots and Multirobot Systems Workshop.
Greenwood, D. (1988). Principles of Dynamics. Prentice-
Hall Englewood Cliffs, NJ.
Grieder, R., et al. (2014). Multi-robot control and interac-
tion with a hand-held tablet. In Proc. IEEE Int. Conf.
Robotics and Automation, volume 131.
Hartley, R. and Zisserman, A. (2003). Multiple View Geom-
etry in Computer Vision. Cambridge University Press.
Hasanzade, I., Anvar, S., and Motlagh, N. (2008). Design
and implementation of visual servoing control for ball
and beam system. In Int. Symp. Mechatronics and Its
Applications, pages 1–5.
Hirschorn, R. (2002). Incremental sliding mode control of
the ball and beam. IEEE Trans. Automatic Control,
47(10):1696–1700.
Hu, J., et al. (2012). Fish species classification by color,
texture and multi-class support vector machine using
computer vision. Computers and Electronics in Agri-
culture, 88:133–140.
Huang, H., et al. (2007). Visual-based impedance force
control of three-dimensional cell injection system.
In IEEE Int. Conf. Robotics and Automation, pages
4196–4201.
Hutchinson, S., Hager, G., and Corke, P. (1996). A tutorial
on visual servo control. IEEE Trans. Robotics and
Automation, 12(5):651–670.
Kastrinaki, V., Zervakis, M., and Kalaitzakis, K. (2003). A
survey of video processing techniques for traffic appli-
cations. Image and Vision Computing, 21(4):359–381.
Laukonen, E. and Yurkovich, S. (1993). A ball and beam
testbed for fuzzy identification and control design. In
American Control Conference, pages 665–669. IEEE.
Lewis, F. (1986). Optimal Estimation: With an Introduction
to Stochastic Control Theory. Wiley New York et al.
Li, G., et al. (2012). Testing mobile phone camera based fin-
gerprint recognition under real-life scenarios. Norsk
informasjonssikkerhetskonferanse, 2012.
Masselli, A., Hanten, R., and Zell, A. (2013). Robust real-
time detection of multiple balls on a mobile robot. In
European Conf. Mobile Robots, pages 355–360.
Nguyen, L., et al. (2009). Vision-based system for the con-
trol and measurement of wastewater flow rate in sewer
systems. Water Science and Technology, 60(ECOL-
ARTICLE-2009-029):2281–2289.
Pang, Z.-H., Zheng, G., and Luo, C.-X. (2011). Augmented
state estimation and LQR control for a ball and beam
system. In Int. Conf. Industrial Electronics and Appli-
cations, pages 1328–1332.
Petrovic, I., Brezak, M., and Cupec, R. (2002). Machine vi-
sion based control of the ball and beam. In Int. Work-
shop Advanced Motion Control, pages 573–577.
Sanderson, A. and Weiss, L. (1980). Image-based vi-
sual servo control using relational graph error signals.
Proc. IEEE, 1074.
UsingTabletsintheVision-basedControlofaBallandBeamTest-bed
101