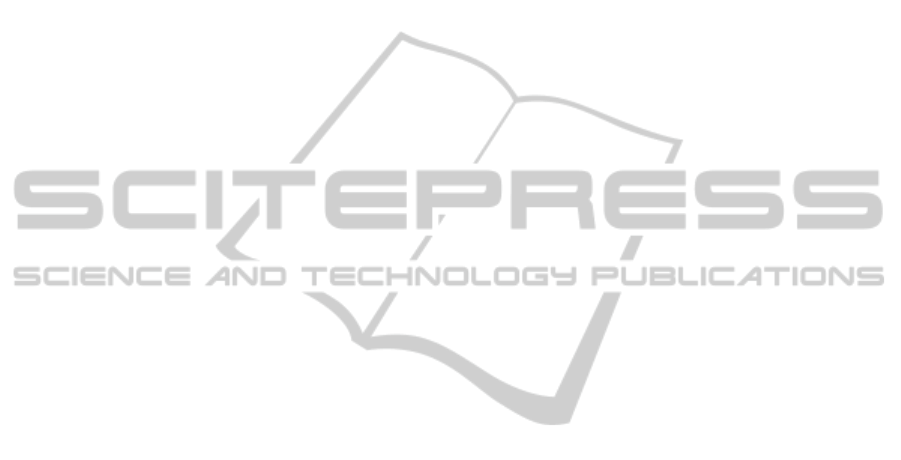
ported by the new approach described here. However,
no sophisticated numerical procedure could be suc-
cessful without: a) a user friendly interface, and b) an
understanding of the problem by the user. In our case,
the target functions as well as the parameter bound-
ary values are stated as time vectors. In the worst
case, the user has to determine 43 vectors; 1 vector of
initial states, 34 boundary vectors and 8 vectors with
target trajectories in order to perform a particular op-
timization run. The minimal set of input data when
boundaries and initial states are set automatically on
the basis of historical data is the vector of goal states
with terminal time.
ACKNOWLEDGEMENT
This research is financed by Slovenian Research
Agency ARRS, Proj. No.: BI-RU/14-15-047 and Re-
search Program Group No. P5-0018 (A).
REFERENCES
Aickelin, U., Dowsland, U., and Kathryn, A. (2004). An in-
direct genetic algorithm for a nurse-scheduling prob-
lem. Comput. Oper. Res., 31(5):761–778.
Albores, P. and Duncan, S. (2008). Government prepared-
ness: Using simulation to prepare for a terrorist attack.
Comput. Oper. Res., 35(6):1924–1943.
Bard, J. F., Morton, D., and Wang, Y. (2007). Workforce
planning at USPS mail processing and distribution
centers using stochastic optimization. Ann. Oper. Res.,
2007(155):51–78.
Chattopadhyay, A. K. and Gupta, A. (2007). A stochastic
manpower planning model under varying class sizes.
Ann. Oper. Res., 2007(155):41–49.
Dimitriou, V. A. and Tsantasb, N. (2010). Evolution of a
time dependent markov model for training and recruit-
ment decisions in manpower planning. Linear Algebra
and its Applications, 433(11-12):1950–1972.
Feyter, T. D. (2007). Modeling mixed push and pull pro-
motion flows in manpower planning. Ann. Oper. Res.,
2007(155):25–39.
Forrester, J. (1973). Industrial Dynamics. MIT Press, Cam-
bridge, MA.
Guerry, M.-A. (2014). Some results on the embeddable
problem for discrete-time markov models in man-
power planning. Communications in Statistics - The-
ory and Methods, 43(7):1575–1584.
Guo, Y., Pan, D., and Zheng, L. (1999). Modeling mixed
push and pull promotion flow. Ann. Oper. Res.,
1999(87):191–198.
Huang, H.-C., Lee, L.-H., Song, H., and Thomas Eck, B.
(2009). Simman-a simulation model for workforce
capacity planning. Comput. Oper. Res., 36(8):2490–
2497.
Kanduˇc, T. and Rodiˇc, B. (2015). Optimization of a fur-
niture factory layout. Croatian Operational Research
Review, 6(1):121–130.
Kofjaˇc, D., Kljaji´c, M., and Rejec, V. (2009). The anticipa-
tive concept in warehouse optimization using simula-
tion in an uncertain environment. European Journal
of Operational Research, 193(3):660–669.
Kok, T., Janssen, F., Doremalen, J., Wachem, E., Clerkx,
M., and Peeters, W. (2005). Philips electronics syn-
chronizes its supply chain to end the bullwhip effect.
Interfaces, 35(1):37–48.
Lanzarone, E., Matta, A., and Scaccabarozzi, G. (2010).
A patient stochastic model to support human resource
planning in home care. Production Planning & Con-
trol, 21(1):3–25.
Mehlman, A. (1980). An approach to optimal recruitment
and transition strategies for manpower systems using
dynamic programming. Journal of Operational Re-
search Society, 31:1009–1015.
Pastor, R. and Olivella, J. (2008). Selecting and adapting
weekly work schedules with working time accounts:
A case of a retail clothing chain. European Journal of
Operational Research, 184:1–12.
Schwartz, J. D., Wang, W., and Rivera, D. E. (2006).
Simulation-based optimization of process control
policies for inventory management in supply chains.
Automatica, 42(8):1311–1320.
Semenkin, E. and Semenkina, M. (2012a). The choice
of spacecrafts’ control systems effective variants with
self-configuring genetic algorithm. In Informatics in
Control, Automation and Robotics: Proceedings of
the 9th International Conference ICINCO, pages 84–
93.
Semenkin, E. and Semenkina, M. (2012b). Self-configuring
genetic algorithm with modified uniform crossover
operator. In Tan, Y., Shi, Y., and Ji, Z., editors, Ad-
vances in Swarm Intelligence, volume 7331 of Lecture
Notes in Computer Science, pages 414–421. Springer
Berlin Heidelberg.
Semenkin, E. and Semenkina, M. (2012c). Self-
configuring genetic programming algorithm with
modified uniform crossover. In Proceedings of the
Congress on Evolutionary Computations of the IEEE
World Congress on Computational Intelligence (CEC
WCCI 2012), pages 1918–1923, Brisbane, Australia.
SCITEPRESS.
Semenkin, E. and Semenkina, M. (2014). Stochastic mod-
els and optimization algorithms for decision support
in spacecraft control systems preliminary design. In
Ferrier, J.-L., Bernard, A., Gusikhin, O., and Madani,
K., editors, Informatics in Control, Automation and
Robotics, volume 283 of Lecture Notes in Electri-
cal Engineering, pages 51–65. Springer International
Publishing.
ˇ
Skraba, A., Kofjaˇc, D.,
ˇ
Znidarˇsiˇc, A., Maletiˇc, M., Rozman,
ˇ
C., Semenkin, E. S., Semenkina, M. E., and Stanovov,
V. V. (2015). Application of self-gonfiguring genetic
algorithm for human resource management. ournal of
Siberian Federal University. Mathematics & Physics,
8(1):94–103.
ModellingandOptimizationofStrictlyHierarchicalManpowerSystem
221