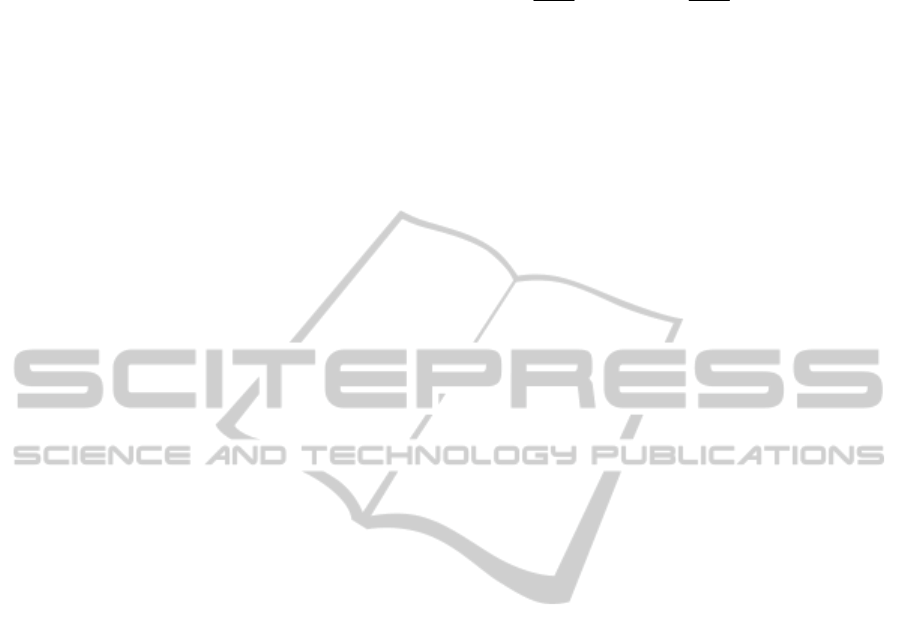
variable is transmitted to both direct channels and to
the controller.
The structure from Figure 6 can work, in the case
the p variable value is not transmitted to the
reference direct channel, but this case is not treated
in this paper. Also, the structure can be adapted for
the case when the automatic determination of the p
value is necessary (Muresan and Abrudean, 2010),
case which also, is not treated in this paper. The
work of the actuator A, it having a linear behaviour,
is expressed using a second order transfer function.
The values of the time constants of the actuator are:
T
A
= 0.1min (the time constant of the actuator) and
T
1
= 2min (the time constant introduced using an
electronic equipment in order to “delay” the
propagation of the control signal to the actuator).
Also, the proportionality constant of the actuator
K
A
= -56.25 ml/(h·mA). The generated output signal
represents the value of the ethanolamine flow which
has to be subtracted from F
inmax
in order to obtain the
F
in
signal. This adjustment is necessary due to the
fact that the plant technological start is made using
F
inmax
. The A element is modelled using the neural
network 7 (NN7). NN7 has exactly the structure
from Figure 4, for n = 10. Also all the delay lines
from Figure 4 are necessary due to the fact that the
actuator model is of second order. The network NN7
is trained using the same training algorithm as in the
case of NN4, the same type of input signal and 500
pairs of input-output data. The imposed mean square
error of is reached after 17 training epochs. The used
sampling time, in this case, has the value
T
s
= 0.036 min. This value is much smaller than the
value of the sampling time used for the training of
all neural networks from the previous Paragraph (3)
(T
s
= 30 min) due to the much smaller time constants
values of the actuator comparing to the value of the
time constant of the technological process.
The transducer T model is expressed using a first
order transfer function with K
T
= 5.7143mA/% (the
proportionality constant of the transducer) and
T
T
= 6min (the time constant of the transducer). The
computation of K
A
and K
T
proportionality constants
is made taking in consideration the fact that the
automation equipment used for this application
works with unified current signals. This model is
learned using the NN8 neural network from
Figure 6. The network parameters and the training
parameters are the same as in the case of the NN4
training, with the exception that T
s
= 0.09min.
The controller is tuned in order to compensate
the main time constant of the process T(T(p)). The
mathematical model which describes the controller
work in time domain is expressed using the
following differential equation:
a(t)
d
da(t)
T(p)c(t)
d
dc(t)
T
f
,
(19)
where T
f
is the time constant of the first order filter
used in order to obtain the controller feasibility
(T
f
< T(p)). The control signal c(t) represents the
solution of the equation (19). At the changing of the
p independent variable value, the value of the
process time constant is modified and from (19) it
results that the value of the T(p) time constant of the
controller is modified, too, in order to be adapted to
the new time constant of the process. This
explanation implies the term “adaptive controller”.
Also the modification of the T(p) value is made
through the value of p independent variable, being
justified the abstract term of “distributed parameter
controller”. The implementation of the controller
using three neural networks interconnected between
them using mathematical operators, is presented in
Figure 7. The NN31 has the same structure as NN3
from Figure 5, generating at the output the value
T(p). Also, the NN41structures have the same
structure as NN4 from Figure 5, implementing the
integration operation. The training procedures and
parameters for the two types of neural networks
from Figure 7 are the same as in the case of NN3
and NN4 from Figure 5, with the exception of the
sampling time (in this case T
s
= 3min). In the case
when the
13
C isotope concentration control is made
in the point p = p
f
, the value T
f
= 8h represents a
good compromise between the system stability and
the structure performances. Also, for this value, the
usage of the control signal is feasible from its
saturation values avoidance point of view.
Having the neural models of the elements A, TP
and T, practically the model of the Reference Model
of the Fixed Part can be implemented, for example,
on a process computer and the structure from
Figure 6 can be used. The model of the controller,
also expressed using a neural networks structure, can
be implemented on a computation equipment, too.
5 SIMULATION RESULTS
The simulations (Colosi et. all, 2013) are made in
MATLAB/Simulink. First the validity of the
analytical solution from (16) is verified. In Figure 8
is presented the comparative graph between 5 step
responses of the separation column model expressed
through the mentioned analytical solution, if the
simulation is made for p = p
f
. The values of the
considered input step type variations are F
in
{200;
ICINCO2015-12thInternationalConferenceonInformaticsinControl,AutomationandRobotics
260