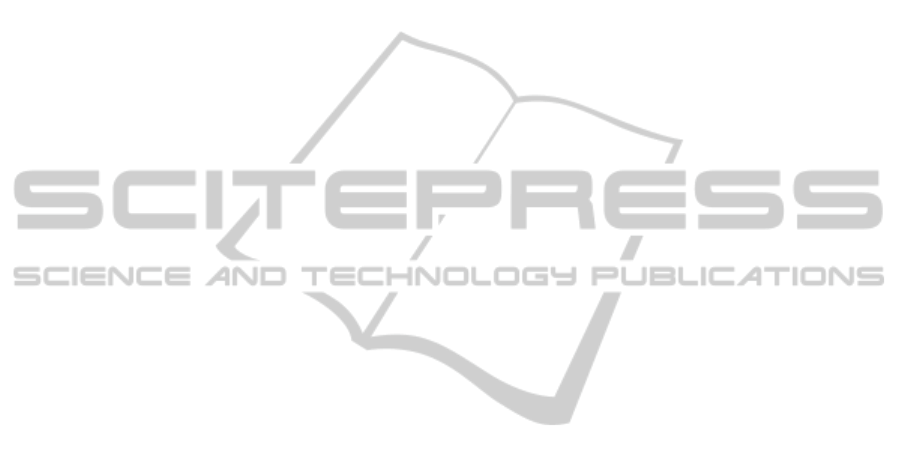
3 CASE STUDY
The case study involved the Siphon well
construction for circulating water in the Datan power
generation project, which is located in Datan
Village, Guanyin Township, Taoyuan County,
Taiwan. The parameters were set as follows:
(a) The number of primary bored piles: The number
of primary bored piles was denoted as N
p
, which
conformed to the principle of N
p
≧ 2 to enable
the construction of secondary bored piles. The
adopted numbers of primary bored piles in this
study were 5, 6, 7, 8, 9, 10, 15, 20, 25, and 30,
enabling the observation of variations in
construction times spent on various numbers of
primary bored piles.
(b) The construction time for the primary bored
piles: The construction time for the primary
bored piles was calculated based on the 104 on-
site construction data, from which the maximum
(4.55) and minimum (2.55) hours were
extracted. The system-produced time for
constructing primary bored piles (i.e.,T
p
) was
generated using random numbers; T
p
ranged
from 2.55 to 4.55.
(c) Number of working hours per day: The
construction crew’s working hours each day
were denoted as T
p
. Through interviews, this
study categorized the working times as 8 hours
(one-day work), 12 hours (one-day of work and
4 hours of overtime), 16 hours (shifts taken by
two construction crews), and 24 hours (shifts
taken by three construction crews, that is, the
full-day construction crews).
(d) The upper limit of the function: The upper limit
of the function was the condition for
terminating system operation. When the waiting
time exceeded the upper limit of the function,
the resulting sequence was regarded as
inadequate and would not be adopted
subsequently. In this study, the upper limit was
assumed to be 200 hours.
(e) The minimum curing time: At a construction
site, the time when the construction of the
secondary bored piles can be initiated (denoted
as T
a
) is generally based on a standard of seven
days. However, construction may also be
initiated after only three days of curing of
primary bored piles. In other words, the
standard curing time is not fixed. In this study,
various lengths of curing time were employed in
the analysis: 3 days (72 hours), 4 days (96
hours), 5 days (120 hours), and 7 days (168
hours).
The number of primary bored piles in a single
cycle: In one cycle, the number of constructed
primary bored piles may influence the time
consumption in that cycle and further influence the
total construction time. Accordingly, the quantities
of primary bored piles in one cycle were set as 6, 7,
8, 9, 10, 15, 20, 25, and 30 for the analysis, to
understand the required construction time when the
amounts of curing time were 72 hours, 96 hours, 120
hours, 144 hours, and 168 hours.
3.1 Analysis of Working Hours
per Day
The construction crew’s working hours each day
may influence the construction time of one cycle,
thereby influencing the total time consumed to
complete the entire construction project. Thus, the
quantity of primary bored piles in one cycle was set
as 5, 6, 7, 8, 9, 10, 15, 20, 25, and 30, and the curing
times were set as 72 hours, 96 hours, 120 hours, 144
hours, and 168 hours, for the subsequent analysis of
the working hours per day, which were 8 hours, 12
hours, 16 hours, and 24 hours.
The total amount of construction time was
influenced when the daily working hours were 12
and 16 hours. However, when the number of
working hours was 8 and 24 per day, the working
hours did not positively influence the total
construction time, because the required curing times
remained the same.
3.2 Sensitivity Analysis
The analysis in the previous section focused on a
single cycle. This study analysed three influencing
factors (the quantity of constructed primary and
secondary bored piles, the working hours per day,
and the curing time for the primary bored piles) and
employed the GA to optimize the construction
sequence for the secondary bored piles, yielding
satisfactory research outcomes. However, in
practice, a given project may need to construct a
fixed number of secant piles. In addition, the
working hours for each day and the possible curing
time are determined using cycle-number calculations
employed by previous studies. For example, in a
given project, 300 primary bored piles and 299
secondary bored piles must be completed. Assuming
that the curing time is 72 hours, working hours are 8
hours per day, and the number of primary bored
piles constructed in each cycle is 20, then the total
time consumption is calculated as follows:
ICSOFT-EA2015-10thInternationalConferenceonSoftwareEngineeringandApplications
148