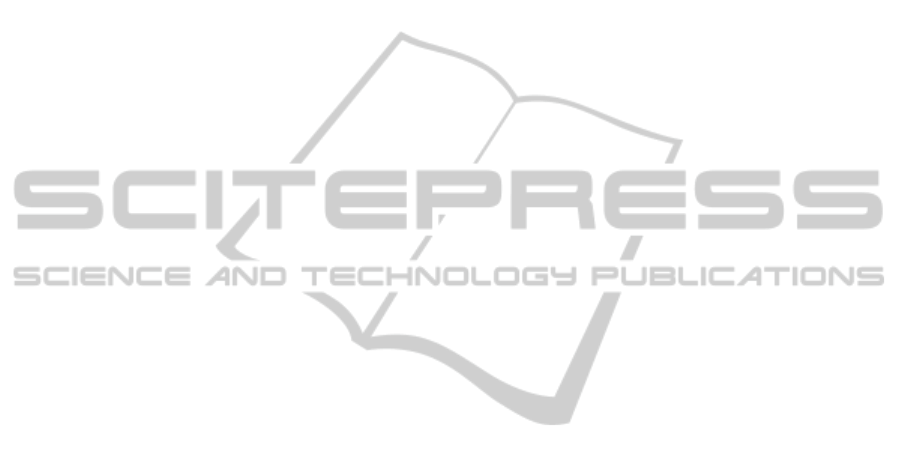
REFERENCES
Holopainen, R., Asikainen, V., Tuomainen, M., Bjorkroth,
M., Pasanen, P., Seppanen, O., 2003. Effectiveness of
duct cleaning methods on newly installed duct
surfaces.
Indoor Air. Vol. 13: pp.212-222.
Jeon, S., Jeong, W., Park, D., 2013. Surface Cleaning
Force Control of Rotating Brushes For an Air Duct
Cleaning Robot,
International Conference on
Informatics in Control, Automation and Robotics
(ICINCO), 2013 July 29-31; Reykjavik, Iceland. pp.
453-457.SCITEPRESS.
Caracciolo, L., De Luca, A., Iannitti, S., 1999. Trajectory
Tracking Control of a Four-Wheel Differentially
Driven Mobile Robot.
IEEE International Conference
on Robotics and Automation. 1999 May 10-15; Detroit,
MI. pp. 2632-2638.
Fierro, R., Lewis, F. L., 1997. Control of a Nonholonomic
Mobile Robot: Backstepping Kinematics into
Dynamics.
Journal of Robotic Systems. Vol. 14, No. 3,
pp. 149-163.
Jeong, W., 2014. Performance Analysis of a Mobile Duct
Cleaning Robot.
International Journal of Advanced
Engineering Applications.
Vol. 7, No. 2, pp. 26-32.
Kim, S., Jung, S., 2006. Hardware Implementation of a
Neural Network Controller with an MCU and an
FPGA for Nonlinear Systems.
International Journal of
Control, Automation, and Systems
. Vol. 4, No. 5, pp.
567-574.
Martinez, J. L., Mandow, A., Morales, A., Pedraza, S.,
Garcia-Cerezo, A., 2005. Approximating Kinematics
for Tracked Mobile Robots.
The International Journal
of Robotics Research.
Vol. 24, No. 10, pp. 867-878.
King, M., 2010.
Process Control: A Practical Approach.
West Sussex: John Wiley and Son. pp. 36-50.
Bloch, A. M., Reyhanoglu, M., McClamroch, N. H., 1992.
Control and stabilization of nonholonomic dynamic
systems.
IEEE Trans. Autom. Control. Vol. 37, No. 11,
pp. 1746-1757.
Sarkar, N., Yun, X., Kumar, V., 1994. Control of
mechanical systems with rolling constraints:
Application to dynamic control of mobile robots
. Int. J.
Rob. Res
. Vol. 13, No. 1, pp. 55-69.
Yang, J. M., Kim, J. H., 1999. Sliding Mode Control for
Trajectory Tracking of Nonholonomic Wheeled
Mobile Robots.
IEEE Transactions on Robotics and
Automation.
Vol. 15, No. 3, pp. 578-587.
Kanayama, Y., Kimura, Y., Miyazaki, F., Noguchi, T.,
1990. A stable tracking control method for an
autonomous mobile robot.
IEEE International
Conference on Robotics and Automation
, 1990 May
13-18; Cincinnati, OH
. pp. 384-389.
M’Closkey, R. T., Murray, R. M., 1994. Extending
exponential stabilizers for nonholonomic systems from
kinematic controllers to dynamic controllers.
Proc.
IFAC Symp. Rob. Control,1994; Capri, Italy
. pp. 211-
216.
ICINCO2015-12thInternationalConferenceonInformaticsinControl,AutomationandRobotics
380