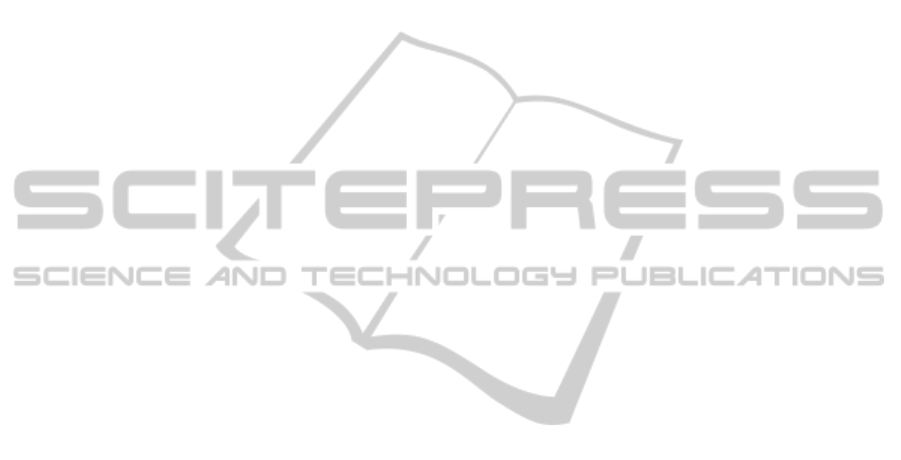
force/dynamics control Salisbury (1980); Mason
(1981); Raibert and Craig (1981); Yoshikawa (1987);
Khatib (1987), impedance control Hogan (1984)
has been particularly effective in order to inter-
act with compliant environments, including also
non-restrictive assumptions Colgate and Hogan
(1989) on the dynamical properties of the interacting
environment. In fact, with respect to pure force
controllers Lange et al. (2012, 2013), impedance con-
trol compounds an easier tunable dynamic balance
response for the robot. In addition, particular design
of impedance controllers Ott et al. (2010), grants
a wide control bandwidth, thanks to a continuous
adaptation of the controller.
Nevertheless, some force/deformation regulation
requirements are introduced (investigated, designed
and validated) in order to improve the robustness and
safety of interaction with a dynamic task, especially
in the case of a precision-force process Roveda
et al. (2013). Although impedance methods are
proved to be dynamically equivalent to explicit force
controllers Volpe and Khosla (1995) a direct tracking
of explicit interaction forces is not straightforwardly
allowed.
To overcome this limitation and preserving the
properties of the impedance behaviour two different
families of methods have been mainly introduced:
class (a) force-position tracking impedance con-
trollers and class (b) variable impedance controllers.
Common solutions of class (a) methods is suggested
in Villani et al. (1999), where the controlled force
is derived from a position control law, scaling the
trajectory as a function of the estimated environ-
ment stiffness, calculating the time-varying PID
gains. Another important approach (Seraji and
Colbaugh, 1993, 1997; Jung et al., 2004) involves
the generation of a reference motion as a function
of the force-tracking error, under the condition that
the environment stiffness is variously unknown,
i.e.estimated as a function of the measured force.
Common solutions of class (b) methods consist on
gain-scheduling strategies that select the stiffness and
damping parameters from a predefined set (off-line
calculated) on the basis of the current target state
(Ikeura and Inooka, 1995; Ferraguti et al., 2013). Lee
and Buss (2000) varies the controlled robot stiffness
on-line to regulate the desired contact force based
on the previous force tracking error, without any
knowledge of the environment. Yang et al. (2011)
presents a human-like learning controller to interact
with unknown environments that feedforward adapts
force and impedance. Oh et al. (2014a,b) describes a
frequency-shaped impedance control method shapes
a disturbance observer in the frequency domain so
that the impedance is manipulated to achieve both the
compliant interaction and reference tracking.
Commonly in class (a) methods, all approaches
mantain a constant dynamic behaviour of the con-
trolled robot, so that when the environment stiffness
quickly and significantly changes, the bandiwth of the
controllers has to be limited for avoiding instability,
while in class (b) methods, stationary, known and
structured environment are considered. Moreover, no
contributions are related to specifically avoid force
overshoots during the task execution.
The aim of this work is to combine the main
features of such control schemes in order to an-
alytically achieve the force overshoots avoidance
goal. Extending the work described in Roveda et al.
(2014), that provide an experimental proof of the
force overshoots avoidance during the task execution
by adapting all the impedance control parameters
(i.e., set-point, stiffness and damping), the developed
method allows to analytically derive the control gains
to obtain a target oscillations-free dynamic behaviour
for the force overshoots avoidance based on the
estimation of the interacting environment stiffness
(performed using an Extended Kalman Filter). The
developed algorithm shapes the equivalent stiffness
and damping of the closed-loop manipulator deform-
ing the impedance control set-point.
The developed control algorithm has been validated
using a KUKA LWR 4+ manipulator in contact with
a second impedance controlled KUKA LWR 4 +
that simulates an interacting environment (Figure 1),
showing the avoidance of force overshoots and the
achieved target dynamic performance.
2 PROBLEM FORMULATION
Based on the estimate of the environment stiffness
b
K
e
and the force error e
f
= f
d
− f, where f
d
and f are the
desired and measured robot forces, respectively, the
developed controller (Figure 2) defines the set-point
x
0
r
of the KUKA LWR 4 + impedance controller in
order to shape the stiffness and damping of the closed-
loop manipulator while tracking a force reference. In
particular, the controller has been derived to have the
complete analytical formulation. In such a way, the
control parameters (i.e., proportional and derivative
gains K
p
, K
d
and shaping coeffients K
0
, m
k
) can be
mathematically defined:
x
0
r
= x
r
+ K
−1
r
(e
f
m
k
+ K
0
)K
p
f
d
b
K
−1
e
− K
d
˙
x
r
(1)
b
K
e
= f (f
e
,x
eq
e
,x
e
) (2)
where K
0
is the diagonal stiffness matrix of the
controlled robot at zero-force error, m
K
is the
ImpedanceControlbasedForce-trackingAlgorithmforInteractionRoboticsTasks:AnAnalyticallyForceOvershoots-free
Approach
387