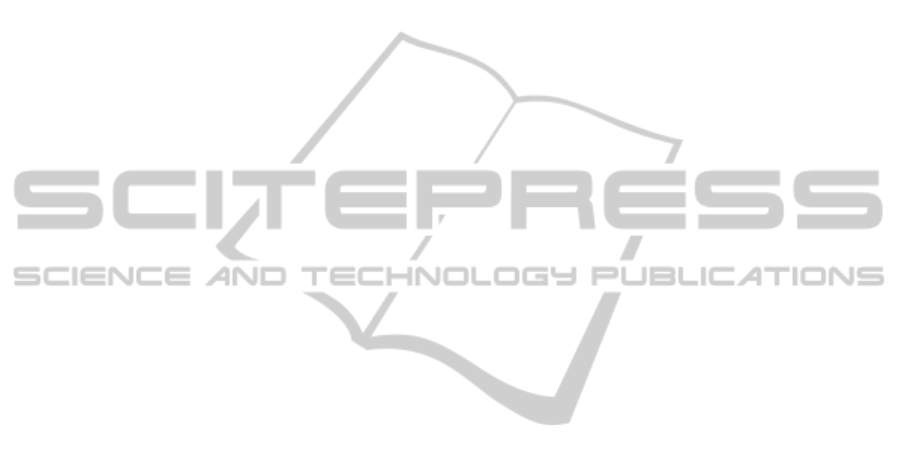
quantified. In the light of the experimental results
presented, the following conclusions can be drawn:
• The cutting forces proved to be more sensitive
to the TCP speed than it is for the cutting speed;
they increased as the TCP speed increased.
• Results show that during high speed robotic
trimming, inaccuracies of the serial robot
kinematic, the mechanical compliance of the
robot and the effective process forces are
leading to large trajectory deviations which
leads to profile errors and dimensional errors.
• Results show also that trajectory deviations and
delamination are the main sources of error
affecting the accuracy of CFRP parts.
• The robot configuration, which is optimally
suited to perform the trimming task, is reached
by using a relatively folded configuration and a
minimal displacement of the joint 1.
During high-speed robotic trimming of CFRP,
the higher cutting forces and the lower stiffness of
the robot, lead to high levels of vibrations.
Regenerative vibrations create chatter. Chatter not
only limits the productivity of cutting processes, but
also causes delamination, poor surface finish,
reduces geometrical accuracy and in some cases,
rejection of machined parts. As future work, it
would be interesting to study the relationship
between cutting conditions and chatter, chatter and
delamination, chatter and tool wear and finally
chatter and surface roughness. A study on the
stability lobes for the prediction of chatter formation
could be also interesting.
On the other hand, results show that trajectory
deviations are the most sources of error affecting the
accuracy of CFRP parts. To reduce the effect of
trajectory deviations, it might be interesting to
propose compensation strategies for this error.
REFERENCES
Muelaner, JE., Wang, Z., Maropoulos PG., 2010.
Concepts for and analysis of a high accuracy and high
capacity (HAHC) aerospace robot, 21
st
International
Computer-Aided Production Engineering Conference
(CAPE), Edinburgh, Scotland.
Slamani, M., Nubiola, A., Bonev, IA., 2012a. Modeling
and assessment of the backlash error of an industrial
robot. Robotica 30(7), 1167-1175.
Ruderman M, Hoffmann F, Bertram T (2009) Modeling
and identification of elastic robot joints with hysteresis
and backlash. IEEE Transactions on Industrial
Electronics 56(10), 3840–3847.
Slamani, M., Nubiola, A., Bonev, IA., 2012b. Assessment
of the positioning performance of an industrial robot
Industrial Robot 39(1), 57-68.
Brogardh, T., 2009. Robot control overview: An industrial
perspective. Modeling Identification and Control
30(3): 167-180.
Lambrechts, P., Boerlage, M., Steinbuch, M., 2005.
Trajectory planning and feedforward design for
electromechanical motion systems. Control
Engineering Practice 13(2): 145-157.
Hakvoort, WBJ., Aarts, RGKM., Dijk, VJ., Jonker, JB.,
2008. Lifted system iterative learning control applied
to an industrial robot. Control Engineering Practice
16(4), 377-391.
Koch, H., Konig, A., Kleinmann, K., Weigl-Seitz, A.,
Suchy J., 2011. Predictive Robotic Contour Following
Using Laser-Camera-Triangulation, IEEE/ASME
International Conference on Advanced Intelligent
Mechatronics, Budapest, Hungary, 422-427.
Kataoka, H., Miyazaki, T., Ohishi, K., Katsura, S.,
Tungpataratanawong, S., 2011. Tracking control for
industrial robot using notch filtering system with little
phase error. Electrical Engineering in Japan 175(1):
793-801.
Olabi, A., Bearee, R., Gibaru O., Damak, M. 2010
Feedrate planning for machining with, industrial six-
axis robots. Control Engineering Practice 18(5):
471-482.
Shimada, A., 1995. Servo system design considering low-
stiffness of robot, Precision Engineering 61(9):
1332-1336.
Lischinsky, P., Canudas-de-Wit, C., Morel, G., 1997.
Friction Compensation of a Schilling Hydraulic Robot.
IEEE International Conference on Control
Applications, Hartford, CT, USA 294-299.
Shirase, K., Tanabe, N., Hirao, M., Yasui, T., 1996,
Articulated robot application in end milling of
sculptured surface, JSME Int. J., Series C, 39 (2):308-
316.
Dumas, C., Boudelier, A., Caro, S., Garnier, S., Ritou, M.,
Furet, B., 2011. Development of a robotic cell for
trimming of composite parts, Mechanics & Industry
12: 487-494.
Leali, F., Vergnano, A., Pini, F., Pellicciari, M., Berselli,
G., 2014. A workcell calibration method for enhancing
accuracy in robot machining of aerospace parts, Int J
Adv Manuf Technol, DOI 10.1007/s00170-014-6025-y.
Sheikh-Ahmad, Jamal Y., 2009. Machining of Polymer
Composites, Springer.
IssuesandChallengesinRoboticTrimmingofCFRP
405