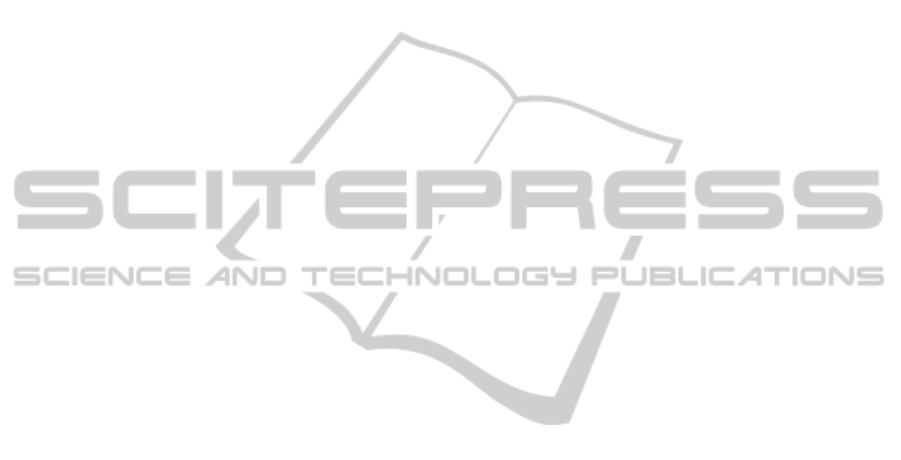
servo controller while the ball dynamics were con-
trolled through a lead compensator. Similar linear
cascaded topologies like the linear full-state feedback
controller can also be used where the inner loop
usually consists of a digital torque controller while
standard LQR and pole-placement design procedures
are applied to the outer loop. Such linear topologies
manage to achieve a limited performance. This is due
to the unaccounted nonlinear dynamics that become
more dominant the further the states are from the
system’s equilibrium point. On the other hand in
(Moarref et al., 2008), (Wang et al., 2007) and (Yuan
and De-hu, 2009) the authors used a fuzzy estimator
in the outer loop to include some ”intelligence” in the
control action action used to regulate the ball position.
In (Ho et al., 2013) a standard linear full-state
feedback controller is used with the feedback lineari-
sation topology to control the ball and plate system.
Feedback linearisation techniques are subject to lim-
itations such as the undefined relative degree of the
linearised ball and plate system at certain locations.
The authors managed to apply an approximative
input-output feedback linearisation technique, where
higher terms of the output could be ignored. A
similar control topology that tries to force a nonlinear
system to behave like a linear system, is the recursive
backstepping method (Khalil, 2002). This method
has been successfully applied to regulate the ball’s
position of two different ball and plate setups in (Ker
et al., 2007) and (Hongrui et al., 2008). On the other
hand papers (Liu and Liang, 2010) and (Liu et al.,
2009) manage to successfully simulate different
sliding mode topologies on the ball and plate model.
Sliding mode control is a robust control strategy
that guarantees a suitable response even in the face
of model imprecisions and external disturbances.
Robustness is achieved by employing a discontinuous
control action. This paper focuses on the study,
comparison and experimental evaluation of this
robust control technique. In addition it presents the
design and construction of the physical ball and plate
experimental test-bed, designed and build specifically
for the purpose of such research.
Despite its interesting nonlinear properties, literature
indicates that the ball and plate system has not at-
tracted as much attention as other setups like the ball
and beam and the inverted pendulum experiments.
Recent works, like (Liu and Liang, 2010) and (Liu
et al., 2009), present the ball and plate results within
a simulation environment. According to Moarref
(Moarref et al., 2008), this is due to the structural
complexities involved in the ball and plate setup.
Papers (Moarref et al., 2008), (Awtar et al., 2002),
(Ker et al., 2007) present different mechanisms that
can be used to implement the actual ball and plate
system. The L-shaped mechanism presented in
(Awtar et al., 2002), is the most popular mechanical
structure, to transmit the necessary torques. In fact
this is the standard actuation mechanism used in
educational setups and research papers (Jadlovska
et al., 2009), (Wang et al., 2012). Variations of
the same mechanisms are presented in (Yuan and
De-hu, 2009),(Ker et al., 2007) and (Yuan and
Zhang, 2010) where different types of actuators
(pneumatic cylinders and magnetic levitation) are
used. The main limitation of such structures is the
resulting small angle plate deflections allowed by
the actuating mechanism. Moarref (Moarref et al.,
2008) presented a different actuation mechanism
where two stepper motors are located at the sides
of the plate. One of the motors is directly coupled
to a metal frame supporting the rotating plate. The
other motor is actuating the plate’s motion through
a mechanical linkage. This structure allows a larger
range of motion, but it is subject to limitations when
the two motors are operating simultaneously. Like
the previous mechanical structures, the encoders do
not provide direct feedback of the plate’s angular
movements. Inaccurate feedback will deteriorate the
overall performance of the closed-loop system. Such
limitations are not desirable for a setup intended to
test nonlinear topologies. Section 3 discusses the ball
and plate hardware that we designed and constructed
to overcome the limitations imposed by the already
available structures.
The rest of the paper is organised as follows. Section
2 introduces the mathematical properties of the ball
and plate system. This is followed by a detailed expla-
nation of the constructed experimental setup, which
is one of the contributions of this paper. Section 4
focuses on the design of the standard linear topol-
ogy that was implemented on the ball and plate sys-
tem. The following section describes the sliding mode
scheme and how this was adapted to tackle a multi-
variable control problem like the ball and plate sys-
tem. Section 6 evaluates the resulting robust response
that was obtained when the sliding controller was im-
plemented on the experimental setup. The proposed
robust control scheme and its experimental compari-
son and evaluation constitute the other two contribu-
tions of this work.
ApplicationofSlidingModeControltotheBallandPlateProblem
413