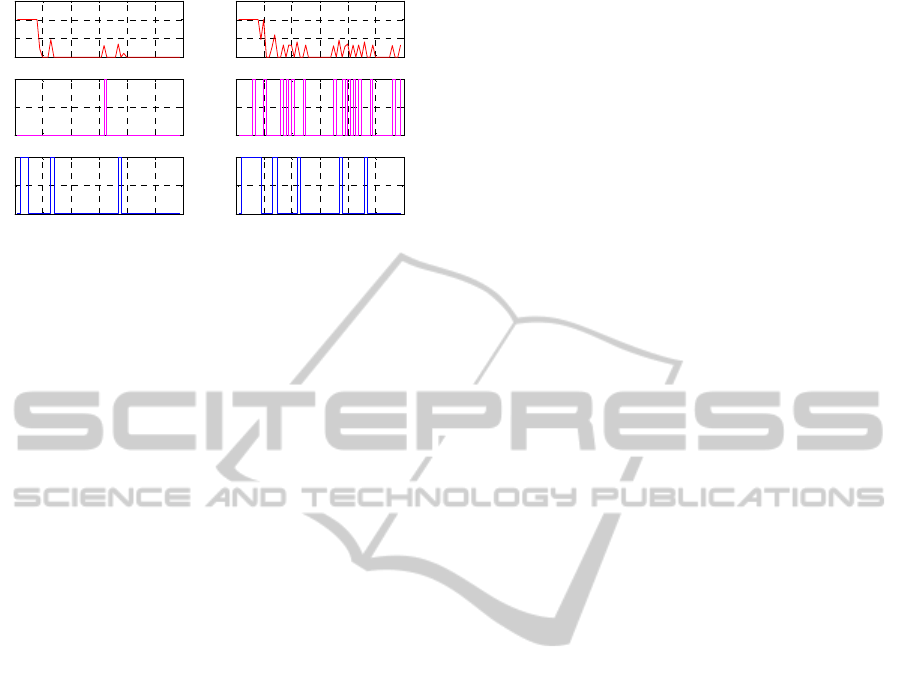
Figure 5: Controlled variables –
3
h
changes.
the suboptimal solution, and increases the
opportunities to find the optimal solution; however
this will increase the computation time. The
selection of the number of particles and the
maximum number of iteration is a trade-off, and is
based on the dynamics of the process to be
controlled.
5 CONCLUSIONS
This paper presented integrating Particle Swarm
Optimization with Analytical Nonlinear Model
Predictive Control (PSO-ANMPC) for constrained
nonlinear hybrid systems with discrete and
continuous control signals. The proposed PSO-
ANMPC controller offers a suboptimal solution in
reasonable time, thus increases the opportunities of
real-time application for many nonlinear hybrid
systems. It can be applied directly to nonlinear
hybrid systems, thus no need to linearize the
nonlinear dynamics as usually done with other
techniques. PSO-ANMPC can be applied to some
classes of hybrid systems including constrained
nonlinear systems, constrained non-convex
optimization problems and fast dynamic hybrid
systems. The proposed controller has the ability to
consider hard and soft constraints. However, there is
no guarantee to find the optimal solution.
An application of the PSO-ANMPC controller to
a three-tanks example showed that it reduces
significantly the computational time, which is an
inherent drawback of classical MPC controllers.
Therefore, real-time implementation of the proposed
PSO-ANMPC controller is possible.
Future work will include experimental works to
validate this technique in practice, as well as,
improving the algorithm and applying it to other
classes of hybrid systems.
REFERENCES
Bemporad A. and M. Morari, 1999. Control of systems
integrating logical, dynamics, and constraints.
Automatica, 35(3):407-427, March.
Bemporad A., F. Borrelli, and M. Morari, 2000a. Optimal
controllers for hybrid systems: Stability and piecewise
linear explicit form. In Proc. 39th IEEE Conf. on
Decision and Control, Sydney, Australia, December
2000.
Bemporad A., F. Borrelli, and M. Morari, 200b. Piecewise
linear optimal controllers for hybrid systems. In Proc.
American Contr. Conf., pages 1190-1194, Chicago,
IL, June 2000.
Bratton D., and J. Kennedy, 2007. Defining a Standard for
Particle Swarm Optimization. Proceedings of the 2007
IEEE Swarm Intelligence Symposium.
Camacho, E. F. et C. Bordons, 1999. Model predictive
control. Springer-Verlag, London.
Clarke, D.W., C. Mohtadi et P. S. Tuffs, 1987.
Generalized predictive control – Part I. and II.
Automatica, Vol.23 (2), pp. 137-160.
Clerc M., and J. Kennedy, 2002. The particle swarm -
explosion, stability, and convergence in a
multidimensional complex space. IEEE Transactions
on Evolutionary Computation, Vol. 6(1): pp. 58-73.
Kennedy, J., Eberhart, R., 1995. Particle Swarm
Optimization. Proceedings of IEEE International
Conference on Neural Network, IV: 1942-1948.
Maciejowski J.M., 2002. Predictive Control. Prentice
Hall.
Olaru Sorin, Jean Thomas, Didier Dumur and Jean
Buisson, 2004. “Genetic Algorithm based Model
Predictive Control for Hybrid Systems under a
Modified MLD Form”, International journal of
Hybrid Systems, Vol. 4 : 1-2, mars-juin 2004.
Poli R., 2008. Analysis of the Publications on the
Applications of Particle Swarm Optimisation. Journal
of Artificial Evolution and Applications, Volume
2008, Article ID 685175, 10 pages.
Richalet J., A. Rault, J. L. Testud et J. Japon. 1978. Model
predictive heuristic control: application to industrial
processes”, Automatica, 14(5), pp. 413-428.
Sedighizadeh D and E. Masehian, 2009. Particle Swarm
Optimization Methods, Taxonomy and Applications.
International Journal of Computer Theory and
Engineering, Vol. 1, No. 5, December 2009. 1793-
8201.
Thomas J., and A. Hansson, 2010. Speed Tracking of
Linear Induction Motor: An Analytical Nonlinear
Model Predictive Controller. In proceeding of
Conference of Control Application CCA’10, Tokyo,
Japan, Sep.
Thomas J., and A. Hansson. Speed Tracking of a Linear
Induction Motor: Enumerative Nonlinear Model
Predictive Control. IEEE Transactions on Control
Systems Technology, Vol.21 (5), pp. 1956-1962, Sept.
2013.
Thomas J., J. BUISSON, D. DUMUR, H. GUÉGUEN,
2003. “Predictive Control of Hybrid Systems under a
0 10 20 30 40 50 60
0
0.5
1
1.5
x 10
-4
Input Q1
0 10 20 30 40 50 60
0
0.5
1
1.5
x 10
-4
Input Q2
0 10 20 30 40 50 60
0
0.5
1
V1
0 10 20 30 40 50 60
0
0.5
1
V2
0 10 20 30 40 50 60
0
0.5
1
Sampling Instants
V13
0 10 20 30 40 50 60
0
0.5
1
Sampling Instants
V23
ICINCO2015-12thInternationalConferenceonInformaticsinControl,AutomationandRobotics
300