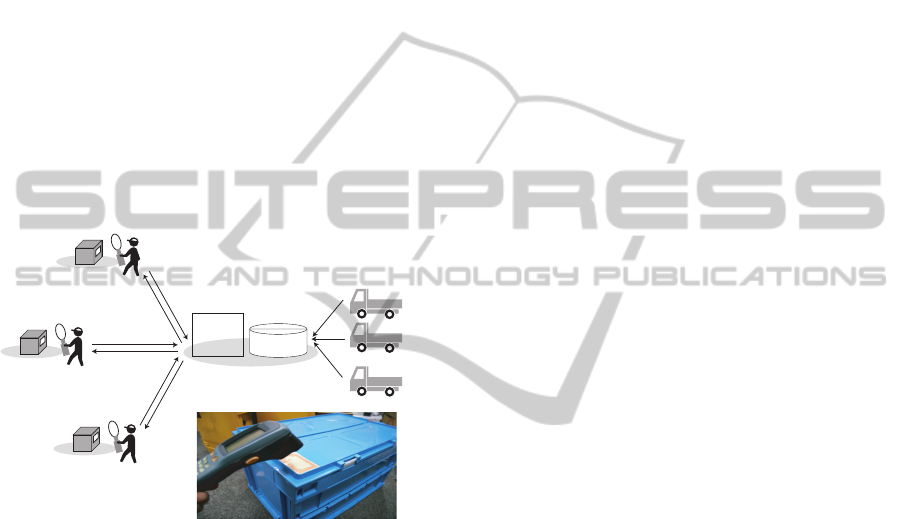
routes in the database satisfy the required route, it se-
lects the truck with the least number of truck move-
ment between points, which is n of ⊒
n
in Definition
3. Although the cost of selecting a route is dependent
on the number of trucks and the length of their routes,
the system can handle each of the routes presented in
this paper within a few milliseconds.
Non-deterministic operators, e.g.,
#
and
%
, tend
to cause the exposition of a number of sub-trees in
transition trees. Nevertheless, our algorithm can eas-
ily restrain the number of sub-trees resulting from
non-deterministic operators because the expansion
rules of expressions, i.e., the operational semantics
of the language, distinguish between derivations re-
sulting from deterministic operators and those result-
ing from non-deterministic operators. Readers may
wonder why E
*
operator creates an infinite number
of sub-trees, but the current implementation interprets
the operator in a lazy evaluation manner.
Route
Database
Client (Supplier A)
Client (Supplier C)
Client (Supplier B)
Recommended
truck identifier
Route
RFID tag reader
RFID tag reader
RFID tag
reader
Box with
RFID tag
Box with
RFID tag
Box with RFID tag
Recommended truck
Recommended truck
Required route
in RFID tag
Required route
in RFID tag
Required route
in RFID tag
Route
Selection
Engine
Route selection server
Route
Route
Figure 7: Experiment.
We have implemented the e-logistics system on a
PaaS cloud computing infrastructure, called Google’
App Engine. Trucks’ routes are maintained in a key-
value store, called Bigtable, provided by the infras-
tructure. When our system receives a truck route
from a truck operator, it transforms the required route
into a tree structure and stores the structure into the
Bigtable database. When it receives a request with a
required route, our route selector engine transforms
the required route into a tree structure and matches
between the structure and the structures correspond-
ing to trucks’ routes. This means truck operators and
suppliers do not need any special equipment to use
the logistics management system. This is important
because in cooperative logistics, most suppliers are
small to medium enterprises that do not want to have
to invest in additional equipment for cooperative lo-
gistics.
The current implementation assumes that the
routes required for products or pallets are stored in
RFID tags attached to the products or pallets because
they may have their own delivery requirements. It
assumes that each client-side system at a supplier or
customer point has more than one RFID tag reader,
which periodically or explicitly tries to detect the
presence of tags within its coverage area. It supported
Phillips i-Code system (13.56 MHz), which provides
each tag with 112 bytes. We were able to maintain
each of the example routes presented in these papers
in the first and second tag systems, where the length of
the identifier for each point was 4 bytes. The current
implementation of the algorithm was not optimized
for performance. Nevertheless, we describe the ba-
sic performance of the implementation. By using an
RFID reader embedded with a WiFi network inter-
face, the cost of reading the route specification in a
tag depends on the length of the specification, e.g. the
cost of reading a specification with a length of less
than 40 bytes is within 0.2 sec. When the routes of
five trucks were registered in the server running on a
computer (Intel Core 2 Duo 2 GHz and WindowsXP),
the cost of selecting a truck after the reader had de-
tected a tag, including the cost of communication be-
tween the server and client via a TCP/IP session, was
less than 1.2 sec. Client-side systems for suppliers
and customers can be operated using only RFID read-
ers, which connect to a server through either wired
or wireless networks. This means they do not need
any special equipment to use the logistics manage-
ment system. This is important because in milk-run
logistics, most suppliers are small to medium enter-
prises that do not want to have to invest in additional
equipment for milk-run logistics.
7 RELATED WORK
There have been many attempts to use process calculi,
e.g., as formal methods for various businessenterprise
processes. Several researchers have used process cal-
culi, e.g., π-calculus, as business-process modeling
languages, such as BPEL, (K. Xu, 2006; M. Mazzara,
2006; F. Puhlmann, 2005; Smith, 2003). π-calculus
has been used as a formal composition language for
software composition and Web service composition,
e.g., Orc (J. Misra, 2004) and SCC (M. Boreale and
Zavattaro, 2006). Process calculi are theoretically
sound and support bisimulation analysis and model
checking. They are also gaining increasing accep-
tance as a support tool in industry. However, there
have been no process-calculus-based formal methods
for logistics, in particular for improving the transport
efficiency of trucks.
ICE-B2015-InternationalConferenceone-Business
22