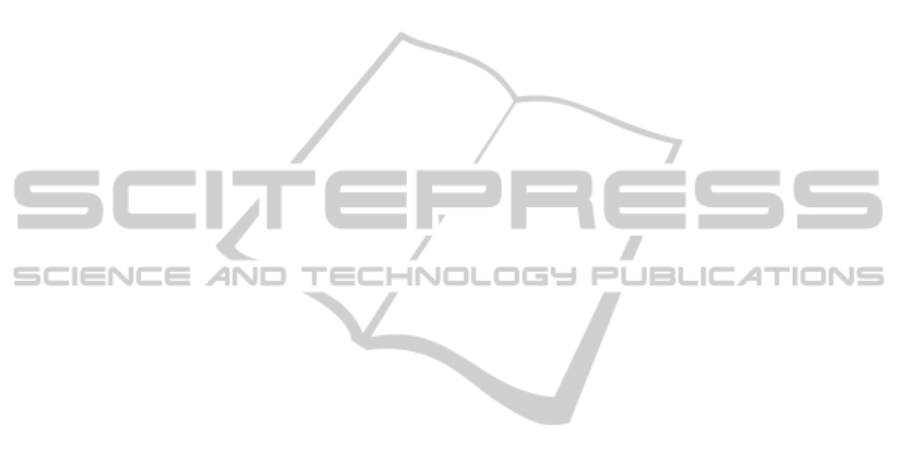
First steps towards the proposed programming en-
vironment have already been made. In a first setup,
a single robot and multiple end-effectors have been
used. Based on a process model and a CAD model of
the robot cell, a semi-automatic generation of a feasi-
ble process flow is possible, including offline teaching
and simulation. Details on the architecture and setup
can be found in N
¨
agele et al. (2015).
5 CONCLUSION
This work illustrated the challenges that develop-
ers face when complex manufacturing processes
should be realized with a multi-functional robot cell.
The Multi-Functional Cell located at the DLR ZLP
in Augsburg is one of the world’s biggest multi-
functional robot cells in operation today and can be
seen as a prototype of what is yet to come accord-
ing to current research agendas. Based on a particu-
lar CFRP manufacturing process, the main challenges
that need to be solved were explained. The vision of a
programming environment for multi-functional robot
cells that unifies process, CAD and robot team models
was presented. By future joint research, the Univer-
sity of Augsburg and the DLR Center for Lightweight
Production will strive to realize this vision.
ACKNOWLEDGEMENT
The demonstration depicted in Section 2 was made
possible with the help and support of Andreas Buch-
heim, Somen Dutta, Mona Eckardt, Lars Larsen,
Thomas Schmidt, and Alfons Schuster of the DLR.
REFERENCES
Baker, A. A., Dutton, S., and Kelly, D. (2004). Composite
Materials for Aircraft Structures. American Institute
of Aeronautics & Astronautics.
Basile, F., Caccavale, F., Chiacchio, P., Coppola, J., and Cu-
ratella, C. (2012). Task-oriented motion planning for
multi-arm robotic systems. Robotics and Computer-
Integrated Manufacturing, 28(5):569 – 582.
euRobotics aisbl (2014). Strategic research agenda for
robotics in Europe 2014 – 2020.
Feldmann, S., Loskyll, M., Rosch, S., Schlick, J., Zuhlke,
D., and Vogel-Heuser, B. (2013). Increasing agility
in engineering and runtime of automated manufactur-
ing systems. In 2013 IEEE Intl. Conf. on Industrial
Technology, pages 1303–1308.
Gan, Y., Dai, X., and Li, D. (2013). Off-Line Program-
ming Techniques for Multirobot Cooperation System.
In Intl. J. of Adv. Robotic Systems. InTech Europe.
Geisberger, E. and Broy, M., editors (2012). Integrierte
Forschungsagenda Cyber-Physical Systems. acatech.
Huckaby, J., Vassos, S., and Christensen, H. I. (2013). Plan-
ning with a task modeling framework in manufactur-
ing robotics. In 2013 IEEE/RSJ Intl. Conf. on Intelli-
gent Robots and Systems, pages 5787–5794.
International Federation of Robotics (2014). World
Robotics – Industrial Robots 2014. VDMA Verlag.
Kagermann, H., Wahlster, W., and Helbig, J. (2013). Rec-
ommendations for implementing the strategic initia-
tive INDUSTRIE 4.0. Final report of the Industrie 4.0
Working Group, acatech.
Krebs, F., Larsen, L., Braun, G., and Dudenhausen, W.
(2014). Design of a multifunctional cell for aerospace
CFRP production. The Intl. J. of Adv. Manufacturing
Technology, pages 1–8.
Larsen, L., Kim, J., and Kupke, M. (2014). Intelligent path
planning towards collision-free cooperating industrial
robots. In 11th Intl. Conf. on Informatics in Control,
Automation and Robotics.
Mediavilla, M., Fraile, J., Peran, J., and Dodds, G. (1998).
Optimization of collision free trajectories in multi-
robot systems. In Robotics and Automation. Proceed-
ings. 1998 IEEE Intl. Conf. on, volume 4, pages 2910–
2915 vol.4.
Michniewicz, J. and Reinhart, G. (2014). Cyber-physical
robotics – automated analysis, programming and con-
figuration of robot cells based on cyber-physical-
systems. Procedia Technology, 15:567–576.
N
¨
agele, L., Macho, M., Angerer, A., Hoffmann, A., Vistein,
M., Sch
¨
onheits, M., and Reif, W. (2015). A backward-
oriented approach for offline programming of com-
plex manufacturing tasks. In The 6th Intl. Conf. on
Automation, Robotics and Applications.
Ou, L.-M. and Xu, X. (2013). Relationship matrix based
automatic assembly sequence generation from a CAD
model. Computer-Aided Design, 45(7):1053 – 1067.
Pfrommer, J., Schleipen, M., and Beyerer, J. (2013). PPRS:
Production skills and their relation to product, pro-
cess, and resource. In 2013 IEEE Intl. Conf. on
Emerging Tech. & Factory Automation, pages 1–4.
Stenmark, M. and Malec, J. (2013). Knowledge-based in-
dustrial robotics. In 12th Scandinavian Conf. on Arti-
ficial Intelligence, pages 265–274.
Stenmark, M., Malec, J., and Stolt, A. (2014). From high-
level task descriptions to executable robot code. In 7th
IEEE Conf. on Intelligent Systems, pages 189–202.
Thomas, U. and Wahl, F. (2001). A system for automatic
planning, evaluation and execution of assembly se-
quences for industrial robots. In Intelligent Robots
and Systems. Proceedings. 2001 IEEE/RSJ Intl. Conf.
on, volume 3, pages 1458–1464 vol.3.
TowardsMulti-functionalRobot-basedAutomationSystems
443