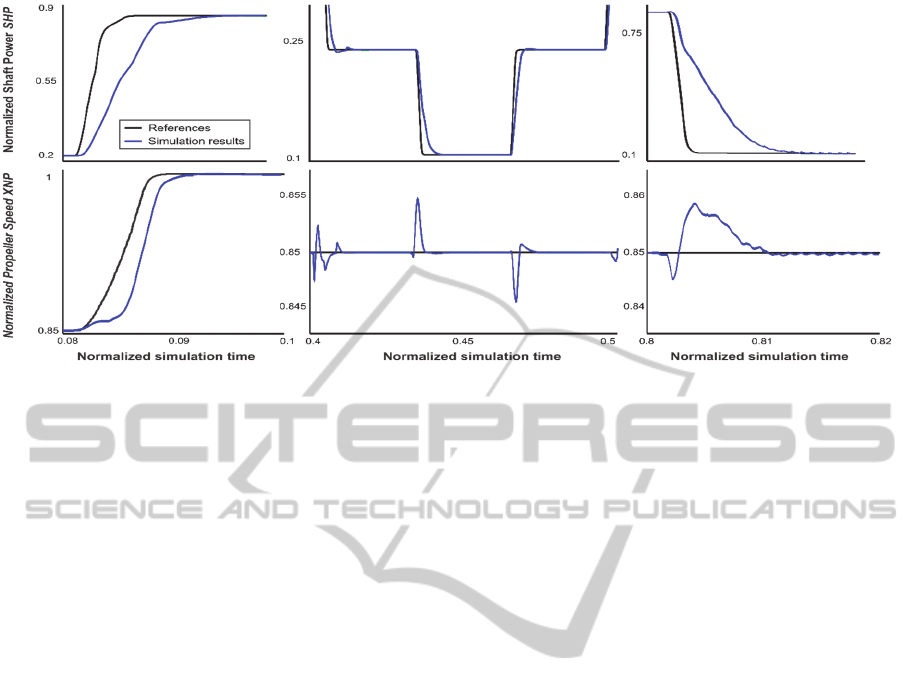
Figure 14: Simulation results (zoom on some transient states).
8 CONCLUSIONS
This paper proposes a straightforward and systematic
way of designing a decentralized control. The first
step consists in analyzing the interactions of the
process. The proposed procedure leads the choice of
an input-output pairing and a control strategy. Given
the high couplings of the turboprop engine, an
inverted decoupler has been used to reduce the
interactions. PI controllers have then been tuned
using an IMC-PID method.
Control laws have been interpolated using a gain
scheduling method in order to ensure the desired
performances on the flight envelope. Robustness
analysis and simulation results finally illustrate the
good performances of the control laws.
Future works will focus on the adaptation of the
proposed methodology in order to take into account
the uncertainties during the interaction analysis and
the decoupling steps.
REFERENCES
Âström, K.J., Hägglund, T., 1995. PID Controllers:
Theory, Design, and Tuning, 2
nd
edition. ISA.
Birk W., Medvedev. A., 2003. “A note on gramian-based
interaction measures”. Proc. European Control
Conference, Cambridge, UK.
Bristol, E., 1966. “On a new measure of interactions for
multivariable process. Automatic Control”. IEEE
Transactions on, Vol 11(1) pp 133-134.
Ferreres, G., 1999. A practical approach to robustness
analysis with aeronautical applications. Kluwer
Academic Publishers.
Ford M.P., Daly K.C., 1979. “Dominance improvement by
pseudodecoupling”. Proceedings of the Institution of
Electrical Engineers. Vol 126(12) pp 1316-1320.
Gagnon, E., Pomerleau, A., Desbiens, A., 1998.
“Simplified, ideal or inverted decoupling?”. ISA Trans.
Vol 37, pp. 265-276.
Garrido, J., Vasquez, F., Morilla F., 2011. “Generalized
Inverted Decoupling for TITO processes”. IFAC,
Milano, Italy.
He M.J., C. W., 2004. “New Criterion for Control-Loop
Configuration of Multivariable Processes”. Control,
Automation, Robotics and Vision Conference, Vol 2,
pp 913-918.
High, G.T., Prevallet, L.C., Free, J.W., 1991. “Apparatus
for decoupling a torque loop from a speed loop in a
power management system for turboprop engines”. US
5274558 A.
Hovd M., Skogestad. S., 1992. “Simple frequency-
dependent tools for control system analysis, structure
selection and design”. Automatica, Vol 28(5) pp 989-
996.
Le Brun, C., Godoy, E., Beauvois D., Liacu, B., Noguera,
R., 2014. “Control Laws Design of a Turboprop
Engine”. Applied Mechanics and Materials Vol 704 pp
362-367.
Maciejowski J.M., 1989. Multivariable Feedback Design.
Addison Wiley.
Niederlinski, A., 1971. “A heuristic approach to the design
of linear multivariable interacting control systems”.
Automatica, Vol 7 pp 691-701.
Rivera, D.E., Morari, M., Skogestad, S., 1986. Internal
model control. 4. PID controller design. Ind. Eng.
Chem. Process Des. Dev., 25, pp 252.
Snecma, 2012. Training Manual Turboprop - General
Familiarization.
Soares, C., 2008. Gas Turbines: a Handbook of Air, Land
and Sea Application. Butterworth-Heinemann.
CouplingAnalysisandControlofaTurbopropEngine
427