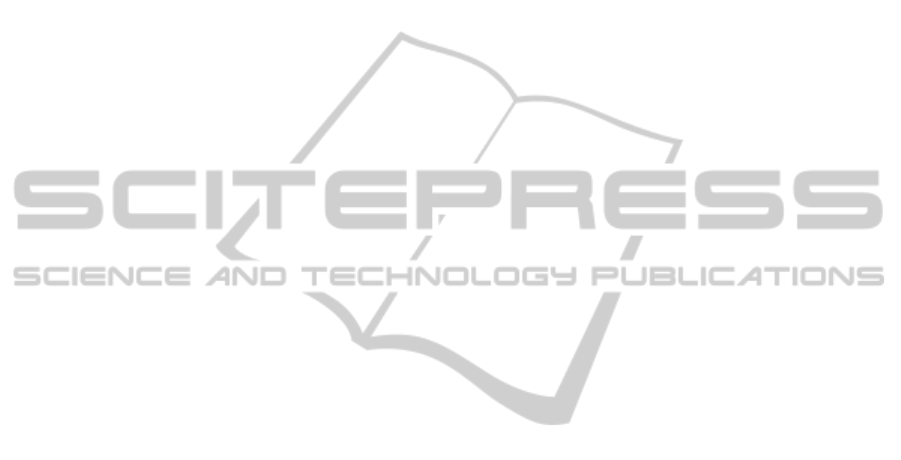
2. Multistage Procedure for PI Controller Tun-
ning: a multistage approach is proposed merg-
ing a deterministic and evolutionary algorithm,
the Normalized Normal Constraint (NNC) and
Multiobjective Differential Evolution Algorithm
with Spherical Pruning (sp-MODE), respectively.
This technique is formulated through design of a
multi-objective optimization procedure, to ensure
the construction of Pareto frontier that guarantee
well distribution and exclude the non-Pareto and
local Pareto points. This procedure focuses on
reliability-based optimization instances. To val-
idate the approach, we will consider the Boiler
Control Benchmark and the Peltier cell; the re-
sults of the improvement of the performance is
demonstrated and its usefulness for controller tun-
ing.
REFERENCES
Alfaro, V. M. (2006). Low-Order Models Identification
from the Process Reaction Curve. Ciencia y Tec-
nolog
´
ıa (Costa Rica), 24(2):197–216. (in Spanish).
Alfaro, V. M. and Vilanova, R. (2012). Conversion for-
mulae and performance capabilities of two-degree-of-
freedom pid control algorithms. In Proceedings of the
17th. IEEE Conference on emerging technologies &
factory automation (ETFA).
Arrieta, O., Visioli, A., and Vilanova, R. (2010). Pid au-
totuning for weighted servo/regulation control opera-
tion. Journal of Process Control, 20(4):472–480.
˚
Astr
¨
om, K. J. and H
¨
agglund, T. (5-7 April, Terrasa, Spain,
2000). Benchmark Systems for PID Control. In IFAC
Digital Control: Past,, Present and Future of PID
Control (PID’00).
Aumann, R. and Hart, S. (1994). Handbook of Game The-
ory with Economic Applications. Elsevier.
Foley, M., Ramharack, N., and Copeland, B. (2005). Com-
parison of PI controller tuning methods. Ind. Eng.
Chem. Res., 44(17):6741–6750.
Mart
´
ınez, M. A., Sanchis, J., and Blasco, X. (2006). Mul-
tiobjective controller design handling human prefer-
ences. Engineering applications of artificial intelli-
gence, 19(8):927–938.
Messac, A., Ismail-Yahaya, A., and Mattson, C. (2003a).
The normalized normal constraint method for gener-
ating the Pareto frontier. Structural and Multidisci-
plinary Optimization, (25):86 – 98.
Messac, A., Ismail-Yahaya, A., and Mattson, C. A. (2003b).
The normalized normal constraint method for gener-
ating the pareto frontier. Structural and multidisci-
plinary optimization, 25(2):86–98.
Miettinen, K. M. (1998). Nonlinear multiobjective opti-
mization. Kluwer Academic Publishers.
Reynoso-Meza, G., S
´
anchez, H., Blasco, X., and Vilanova,
R. (2014a). Reliability based multiobjective optimiza-
tion design procedure for pi controller tuning. In 19th
World Congress The International Federation of Au-
tomatic Control, Cape Town, South Africa.
Reynoso-Meza, G., Sanchis, J., Blasco, X., and Mart
´
ınez,
M. (2014b). Controller tuning using evolutionary
multi-objective optimisation: current trends and ap-
plications. Control Engineering Practice, (DOI:
10.1016/j.conengprac.2014.03.003).
S
´
anchez, H., Reynoso-Meza, G., Vilanova, R., and Blasco,
X. (2013). Comparaci
´
on de t
´
ecnicas de optimizaci
´
on
multi-objetivo cl
´
asicas y estoc
´
asticas para el ajuste de
controladores pi (spanish). In XXXIV Jornadas de Au-
tom
´
atica, Terrassa, Barcelona, Spain.
S
´
anchez, H. and Vilanova, R. (2013a). Multiobjective tun-
ing of PI controller using the NNC method: Simpli-
fied problem definition and guidelines for decision
making. In Proceedings of the 18th IEEE Confer-
ence on Emerging Technologies & Factory Automa-
tion, Cagliary, Italy.
S
´
anchez, H. and Vilanova, R. (2013b). Nash-based criteria
for selection of pareto optimal controller. In Proceed-
ings of the 17th. International Conference on System
Theory, Control anmd Computing, Sinaia, Romania.
S
´
anchez, H. and Vilanova, R. (2014). Optimality compari-
son of 2dof PID implementations. In Proceedings of
the 18th International Conference on System Theory,
Control and Computing, Sinaia, Romania.
S
´
anchez, H., Vilanova, R., and Arrieta, O. (2014). Imple-
mentacion de controladores PID: Equivalencia y opti-
malidad (spanish). In XXXV Jornadas de Autom
´
atica,
Valencia, Spain.
S
´
anchez, H., Visioli, A., and Vilanova, R. (2015). Nash tun-
ing for optimal balance of the servo/regulation opera-
tion in robust pid control. In Mediterranean Confer-
ence on Control & Automation, Torremolinos, Spain.
Zhuang, M. and Atherton, D. P. (1993). Automatic tuning of
optimum PID controllers. IEE Proceedings - Control
Theory and Applications, 140:216–224.
Multi-objectiveOptimizationforControlandProcessOperation
21