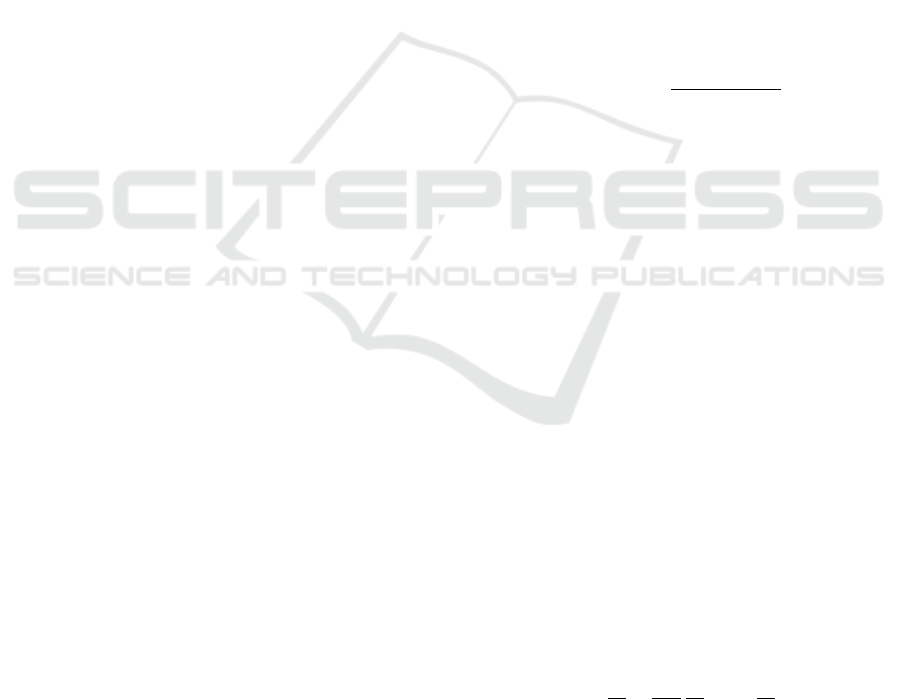
can be found for the optimization of the control policy
performance.
In this perspective, the main contributions of the
paper are two. First, the control policies employed by
the “standard” ACC systems are compared by means
of extensive simulations, considering different realis-
tic road scenarios. This kind of study is important to
understand which control policies and, more in gen-
eral, which control approaches can be more effec-
tive in view of their implementation on real vehicles.
Second, an optimization strategy based on a multi-
objective Pareto criterion is proposed, finalized at de-
signing high-performance control policies. The strat-
egy is tested by means of extensive simulations, in-
volving different realistic road scenarios. These simu-
lations show that the method allows the design of con-
trol policies able to perform significantly better with
respect to the “standard” policies, in terms of safety
and fuel consumption.
2 VEHICLE MODEL AND
CONTROL POLICIES
In this section, we introduce the vehicle and control
models that will be used in the simulations, first to
compare the “standard” ACC systems, then to test our
optimal control policy design method.
The following assumptions were made:
• All vehicles are identical and move in a straight
line.
• Before the maneuver of the lead vehicle, all the
vehicles were moving at the same steady state
speed.
• The lead vehicle takes a finite amount of time to
perform a maneuver prior to reaching steady state
speed.
The longitudinal dynamics of each vehicle (plant)
can be approximated by the following model (see (Ra-
jamani, 2012; Santhanakrishnan et al., 2003; Swaroop
et al., 1994)):
τ
...
p
+ ¨p = u (1)
where p is the vehicle longitudinal position, u repre-
sents a “desired” longitudinal acceleration and τ is the
vehicle time constant.
The desired acceleration u is the control input,
which can be used to improve the vehicle perfor-
mance in terms of safety, comfort and fuel consump-
tion. This task can be accomplished by a proper con-
trol policy, as shown schematically in Fig. 1, where
the block “Vehicle” is a dynamic system described
by (1) and ε is the spacing error to be defined sub-
sequently.
Usually, the control policies should satisfy string
stability requirements in order to give a good perfor-
mance. String stability is defined as stability with re-
spect to the spacing between vehicles. It ensures that
the spacing error, defined as the difference between
the actual and desired spacing, do not get larger as it
propagates upstream in a string of Adaptive Cruise
Control vehicles using the same control law (Raja-
mani, 2012; Santhanakrishnan et al., 2003; Swaroop,
1995; Swaroop et al., 1994; Yanakiev et al., 1998;
Chi-Ying et al., 1999). The CSP policy requires inter-
vehicular communication if string stability is to be
guaranteed (Swaroop et al., 1998; Yanakiev et al.,
1998), while the CTG and VTG policies overcome
this limitation (Yanakiev et al., 1995; Swaroop et al.,
1994; Yanakiev et al., 1998). Since we are only con-
sidering the autonomous operation, our tests are con-
ducted only on the CTG and VTG policies.
The CTG policy is defined by the control law
u = −
( ˙p − ˙p
f
+ λε)
h
(2)
ε = p −p
f
+ L
des
where p and p
f
are the positions of a vehicle and
the preceding vehicle respectively, and ε is the devi-
ation from the desired spacing, otherwise known as
the spacing error, (Rajamani, 2012; Santhanakrishnan
et al., 2003; Swaroop et al., 1994; Zhao et al., 2009).
λ, L
des
and h are design parameters, to be chosen
in order to obtain the desired longitudinal dynamics
performance. λ is a control gain, L
des
is the desired
spacing between the vehicles and h is called the time
gap (it represents the time distance between the two
vehicles).
Combining the vehicle equation (1) with the con-
trol equations (2), we obtain an Linear Time Invariant
(LTI) system, with input p
f
and output y = ε. Note
that, on a vehicle equipped with an ACC systems, p
f
is typically measured by a radar.
The VTG has several variants (Zhou et al., 2004;
Santhanakrishnan et al., 2003; Yanakiev et al., 1995;
Zhao et al., 2009; Wang et al., 2004, 2002; Zhou et al.,
2005), which are similar to each other. The Nonlin-
ear Range Policy (NRP) (Zhou et al., 2004, 2005) is
considered here because of its simple structure. This
policy is defined by the control law
u = (1 −
τk
h
−
τλk
h
2
h
2
k
) ¨p +(
τk
h
2
) ˙p
f
− ˙p (3)
where k is a design parameter, called the scaling factor
(Zhou et al., 2004, 2005).
As for the VTG policy, combining the vehicle
equation (1) with the control equations (3), we obtain
an LTI system, with input p
f
and output y = ε.
VEHITS 2016 - International Conference on Vehicle Technology and Intelligent Transport Systems
14