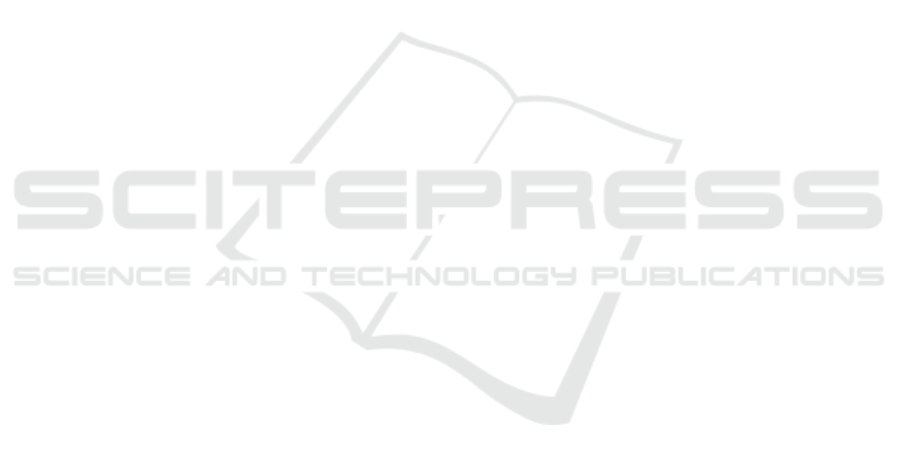
General Motors, is still an open question.
Throughout the process it also became evident that
when the model is done up-front, before a full un-
derstanding of the surrounding system is in place, it
will be based on assumptions on what the context will
look like. This is in line with results from Volvo Cars
(Eliasson et al., 2014). In our case we found inconsis-
tent assumptions regarding the types of signal values
as well as the internal logic of surrounding systems.
Finally, introducing MBT will have a positive ef-
fect on the time it takes to go from concept to pro-
duction since testing can be done much earlier and the
combination of simulations and hardware rigs will ex-
pose defects quicker than the traditional waterfall pro-
cess. In this way model-based ways of working will
promote an agile and iterative development, which in
turn shortens the lead times (Eliasson and Burden,
2013; Burden et al., 2014).
6 CONCLUSIONS
Our study complements and expands previous re-
search by exploring the impact of model-based test-
ing for validating the behaviour of a truck’s head
beams. The study was conducted at Volvo Group
Trucks Technology in Gothenburg, Sweden, and con-
sisted of testing at three different stages. First the
model was tested as is at the Model-in-the-Loop
stage; then it was tested in a simulated system known
as the Software-in-the-Loop stage; before finally be-
ing tested in a hardware rig – the Hardware-in-the-
Loop stage.
Our results are three-fold. First, we show how a
model can be transferred from a Model-in-the-Loop
setting to a Hardware-in-the-Loop context via a sys-
tem simulation; the overall process is shown in Fig.
1. Second, we supply an analysis of the shortcomings
of the model that were found as the model was tested
in more and more platform-specific settings. Third,
our results show that the introduction of model-based
testing will require organisational changes even if the
used tools are familiar to the company.
In the near future we will be able to test the model
on a real truck to see if any new defects or faulty as-
sumptions are exposed. Another research direction
for the future is to explore to which extent the test
cases developed for the MiL stage can be automati-
cally reused at the more platform-specific stages, but
also to determine to which extent the test cases for the
SiL and HiL stages can be reused with other program-
ming tools since it is not yet established which tools
will be used across the organisation.
Speaking of organisation, it is still work in
progress to implement and adapt the developed test
practices in the organisation at large and we aim to
report on the organisational changes and necessary
adaptations of model-based practices. A key aspect
to explore is to which extent MBT can be used for
other features of the truck and in other divisions of the
organisation. In this line of work we will seek strate-
gies to mitigate the tensions reported on by previous
studies, to explore how the test engineers and test en-
vironment developers can work in harmony with each
other.
ACKNOWLEDGEMENTS
The authors would like to thank Mathworks for pro-
viding the necessary licenses for free during the case
study. We would also like to acknowledge the effort
that Vector put into the case study by adapting their
tools for our needs. This work was partially funded
by the Vinnova project Next Generation Electrical Ar-
chitecture.
REFERENCES
Aranda, J., Damian, D., and Borici, A. (2012). Transition to
Model-Driven Engineering - What Is Revolutionary,
What Remains the Same? In MODELS 2012, 15th In-
ternational Conference on Model Driven Engineering
Languages and Systems, pages 692–708. Springer.
Bringmann, E. and Kramer, A. (2008). Model-Based Test-
ing of Automotive Systems. In Software Testing, Ver-
ification, and Validation, 2008 1st International Con-
ference on, pages 485–493.
Burden, H., Heldal, R., and Whittle, J. (2014). Com-
paring and Contrasting Model-driven Engineering at
Three Large Companies. In Proceedings of the 8th
ACM/IEEE International Symposium on Empirical
Software Engineering and Measurement, ESEM ’14,
pages 14:1–14:10, New York, NY, USA. ACM.
Eliasson, U. and Burden, H. (2013). Extending Agile Prac-
tices in Automotive MDE. In XM Extreme Modeling
Workshop, Miami, Fl, USA.
Eliasson, U., Heldal, R., Lantz, J., and Berger, C. (2014).
Agile Model-Driven Engineering in Mechatronic Sys-
tems - An Industrial Case Study. In Dingel, J.,
Schulte, W., Ramos, I., Abrah
˜
ao, S., and Insfr
´
an, E.,
editors, Model-Driven Engineering Languages and
Systems - 17th International Conference, MODELS
2014, Valencia, Spain, September 28 - October 3,
2014. Proceedings, volume 8767 of Lecture Notes in
Computer Science, pages 433–449. Springer.
Etschberger, K. (2001). Controller Area Network: Basics,
Protocols, Chips and Applications. IXXAT Automa-
tion GmbH.
From Model to Rig – An Automotive Case Study
621