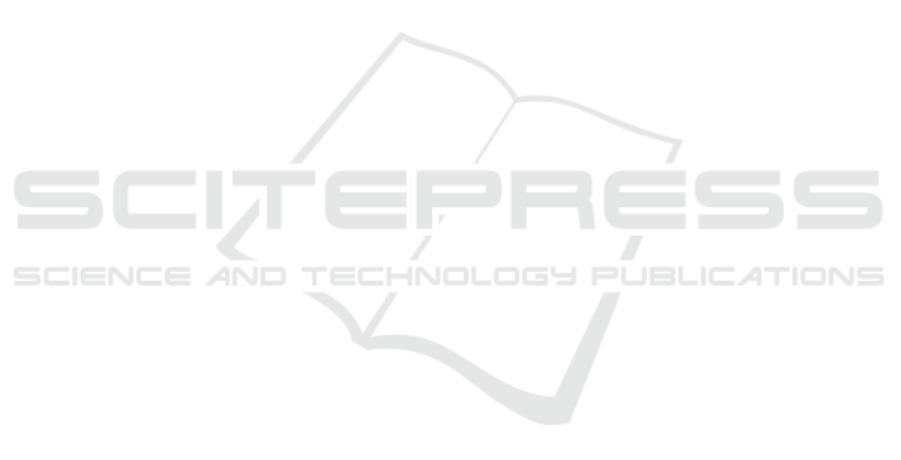
Bostelman, R., Hong, T., and Chang, T. (2006). Visualiza-
tion of pallets. In SPIE Optics East.
Bourdev, L. and Brandt, J. (2005). Robust object detection
via soft cascade. In CVPR, pages II: 236–243.
Byun, S. and Kim, M. (2008). Real-time positioning and
orienting of pallets based on monocular vision. In IC-
TAI (2), pages 505–508. IEEE Computer Society.
Chen, J., Shan, S., He, C., Zhao, G., Pietik
¨
ainen, M., Chen,
X., and Gao, W. (2010). Wld: A robust local image
descriptor. IEEE Trans. Pattern Anal. Mach. Intell,
32(9):1705–1720.
Cucchiara, R., Piccardi, M., and Prati, A. (2000). Focus
based feature extraction for pallets recognition. In
BMVC.
Dalal, N. and Triggs, B. (2005). Histograms of oriented gra-
dients for human detection. In CVPR, pages I: 886–
893.
Doll
´
ar, P., Appel, R., Belongie, S., and Perona, P. (2014).
Fast feature pyramids for object detection. PAMI.
Doll
´
ar, P., Belongie, S., and Perona, P. (2010). The fastest
pedestrian detector in the west. In BMVC, pages 1–11.
British Machine Vision Association.
Dollar, P., Tu, Z. W., Perona, P., and Belongie, S. (2009).
Integral channel features. In BMVC.
Doll
´
ar, P., Wojek, C., Schiele, B., and Perona, P. (2012).
Pedestrian detection: An evaluation of the state of
the art. IEEE Trans. Pattern Anal. Mach. Intell,
34(4):743–761.
Duda, R. and Hart, P. E. (1972). Use of the hough transfor-
mation to detect lines and curves in pictures. CACM,
15:11–15.
Hirschmuller, H. (2005). Accurate and efficient stereo pro-
cessing by semi-global matching and mutual informa-
tion. In CVPR, pages II: 807–814.
Hough, P. V. C. (1962). A method and means for recogniz-
ing complex patterns. U.S. Patent No. 3,069,654.
Katsoulas, D. and Kosmopoulos, D. I. (2001). An efficient
depalletizing system based on 2d range imagery. In
IEEE International Conference on Robotics and Au-
tomation, 2001. Proceedings 2001 ICRA., volume 1,
pages 305–312. IEEE.
Kim, W., Helmick, D., and Kelly, A. (2001). Model based
object pose refinement for terrestrial and space auton-
omy. In International Symposium on Artificial Intelli-
gence, Robotics, and Automation in Space, Montreal,
Quebec, Canada.
Mikolajczyk, K., Zisserman, A., and Schmid, C. (2003).
Shape recognition with edge-based features. In
BMVC.
Nyg
˚
ards, J., H
¨
ogstr
¨
om, T., and Wernersson,
˚
A. (2000).
Docking to pallets with feedback from a sheet-of-light
range camera. In IROS, pages 1853–1859. IEEE.
Oh, J.-Y., Choi, H.-S., Jung, S.-H., Kim, H.-S., and Shin,
H.-Y. (2013). An experimental study of pallet recogni-
tion system using kinect camera. In Advanced Science
and Technology Letters Vol.42 (Mobile and Wireless
2013), pages 167–170.
Ojala, T., Pietikainen, M., and Harwood, D. (1994). Perfor-
mance evaluation of texture measures with classifica-
tion based on kullback discrimination of distributions.
In ICPR, pages A:582–585.
Ojala, T., Pietikainen, M., and Harwood, D. (1996). A com-
parative study of texture measures with classification
based on feature distributions. Pattern Recognition,
29(1):51–59.
Pages, J., Armangue, X., Salvi, J., Freixenet, J., and Marti,
J. (2011). Computer vision system for autonomous
forklift vehicles in industrial environments. The 9th.
Mediterranean Conference on Control and Automa-
tion.
Pradalier, C., Tews, A., and Roberts, J. M. (2008). Vision-
based operations of a large industrial vehicle: Au-
tonomous hot metal carrier. J. Field Robotics, 25(4-
5):243–267.
Prasse, C., Skibinski, S., Weichert, F., Stenzel, J., M
¨
uller,
H., and Hompel, M. T. (2011). Concept of automated
load detection for de-palletizing using depth images
and RFID data. International Conference on Con-
trol System, Computing and Engineering (ICCSCE),
pages 249–254.
Ross, H. and Murray, D. J. (1996). E.H.Weber on the tac-
tile senses 2nd ed. Hove: Erlbaum (UK) Taylor and
Francis.
Schapire, R. (1990). The strength of weak learnability.
MACHLEARN: Machine Learning, 5.
Seelinger, M. J. and Yoder, J.-D. (2006). Automatic visual
guidance of a forklift engaging a pallet. Robotics and
Autonomous Systems, 54(12):1026–1038.
Spangenberg, R., Langner, T., Adfeldt, S., and Rojas, R.
(2014). Large scale semi-global matching on the CPU.
In Intelligent Vehicles Symposium, pages 195–201.
IEEE.
Varga, R. and Nedevschi, S. (2014). Vision-based auto-
matic load handling for automated guided vehicles. In
Intelligent Computer Communication and Processing,
pages 239–245. IEEE.
Viola, P. and Jones, M. (2001). Rapid object detection using
a boosted cascade of simple features. Proc. CVPR,
1:511–518.
Viola, P. A., Platt, J. C., and Zhang, C. (2005). Multiple
instance boosting for object detection. In NIPS.
Walter, M. R., Karaman, S., Frazzoli, E., and Teller, S. J.
(2010). Closed-loop pallet manipulation in unstruc-
tured environments. In IROS, pages 5119–5126.
IEEE.
Weichert, F., Skibinski, S., Stenzel, J., Prasse, C., Kama-
gaew, A., Rudak, B., and ten Hompel, M. (2013). Au-
tomated detection of euro pallet loads by interpreting
PMD camera depth images. Logistics Research, 6(2-
3):99–118.
Yang, M.-H., Kriegman, D. J., and Ahuja, N. (2002). De-
tecting faces in images: A survey. IEEE Trans. Pattern
Anal. Mach. Intell, 24(1):34–58.
Zabih, R. and Woodfill, J. (1994). Non-parametric local
transforms for computing visual correspondence. In
ECCV, pages B:151–158.
Robust Pallet Detection for Automated Logistics Operations
477