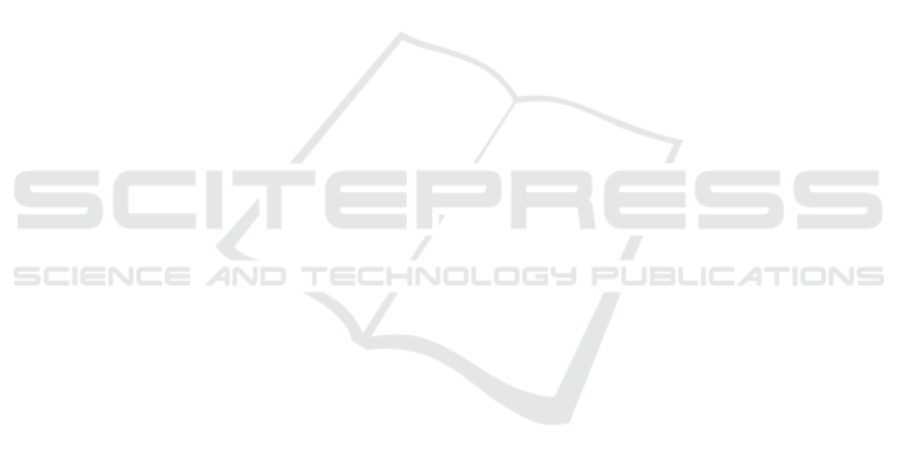
and a video conferencing system, respectively. These
consist of approximately 500 variables. Whereas the
third example, a vessel prognostics and health man-
agement system, consists of approximately 1000 vari-
ables. These examples illustrate the numbers in Table
1 which show that the proposed approach is sufficient
for configuring today’s automation systems. With the
calculation of the minimum correction subsets inte-
grated into the software described in section 5, a tool
is created which enables engineers to design automa-
tion systems very efficiently. Furthermore, even sys-
tems with several thousand components can be easily
formulated and checked for consistency.
7 CONCLUSION
In this paper a holistic approach to designing automa-
tion systems is presented. Based on the work intro-
duced in (T
¨
orngren et al., 2014) and (Nie et al., 2013),
it is shown that our work contributes to greatly sim-
plify and speed up the design of an automation sys-
tem. The most important point is that through the
presented work system designers can concentrate on
high-level specifications in their field of knowledge
while certain details and implementation specific as-
pects are added automatically. Overall, the presented
approach aides designers in two ways. On the one
hand, the design is compartmentalised to accommo-
date the need that experts with different backgrounds
and professions interpret designs in different ways
(see (T
¨
orngren et al., 2014)). This means, in order to
achieve maximum efficiency, each expert should be
best put to work with a vocabulary and concepts he is
most familiar with. On the other hand, the AD4AS
prototype finds each unsatisfied constraint within a
system and can attribute it to different views (i.e. ex-
perts). Furthermore, we showed in section 6, that
finding unsatisfied constraints can be done in reason-
able time for the amount of components usually found
in automation systems. Therefore, the suggestions
from (Fay et al., 2015) and (T
¨
orngren et al., 2014)
were implemented and extended to construct a proto-
type which can contribute to close the gap between
the increasing complexity of automation systems and
automated design tools.
ACKNOWLEDGEMENT
Funded by the German Federal Ministry of Education
and Research, ’Design Methods for Automation Sys-
tems with Model Integration and Automatic Variation
Validation’, 16M3204B.
REFERENCES
Ansotegui, C., Bonet, M. L., and Levy, J. (2013). Sat-based
maxsat algorithms. Artificial Intelligence, 196:77–
105.
Bartak, R. (1999). Constraint programming: In pursuit of
the holy grail. In in Proceedings of WDS99 (invited
lecture), pages 555–564.
Becket, R. (2015). Specification of flatzinc-version 1.6.
Benavides, D., Cort
´
es, R. A., and Trinidad, P. (2004).
Coping with automatic reasoning on software product
lines. In Proceedings of the 2nd Groningen Workshop
on Software Variability Management.
Benavides, D., Segura, S., and Ruiz-Cort
´
es, A. (2010). Au-
tomated analysis of feature models 20 years later: A
literature review. Information Systems, 35(6):615–
636.
Bofill, M., Palah
´
ı, M., Suy, J., and Villaret, M. (2012). Solv-
ing constraint satisfaction problems with sat modulo
theories. Constraints, 17(3):273–303.
B
¨
ottcher, B., Moriz, N., and Niggemann, O. (2014). From
formal requirements on technical systems to complete
designs - a holistic approach. In Schaub, T., Friedrich,
G., and O’Sullivan, B., editors, 21st European Con-
ference on Artificial Intelligence, volume 263 of Fron-
tiers in Artificial Intelligence and Applications, pages
977–978.
Chakrabarti, A., Shea, K., Stone, R., Cagan, J., Camp-
bell, M., Hernandez, N. V., and Wood, K. L.
(2011). Computer-based design synthesis research: an
overview. Journal of Computing and Information Sci-
ence in Engineering, 11(2):021003.
Czarnecki, K. and Eisenecker, U. W. (2000). Generative
programming: methods, tools, and applications.
Czarnecki, K., Hwan, C., Kim, P., and Kalleberg, K. (2006).
Feature models are views on ontologies. In Software
Product Line Conference, 2006 10th International,
pages 41–51. IEEE.
Fay, A., Vogel-Heuser, B., Frank, T., Eckert, K., Hadlich,
T., and Diedrich, C. (2015). Enhancing a model-based
engineering approach for distributed manufacturing
automation systems with characteristics and design
patterns. Journal of Systems and Software, 101(0):221
– 235.
Felfernig, A., Benavides, D., Galindo, J., and Reinfrank, F.
(2013). Towards anomaly explanation in feature mod-
els. In Workshop on Configuration, Vienna, Austria,
pages 117–124.
Freuder, E. C. and Wallace, R. J. (1992). Partial constraint
satisfaction. Artificial Intelligence, 58(1):21–70.
Gruner, S., Weber, P., and Epple, U. (2014). Rule-based en-
gineering using declarative graph database queries. In
Industrial Informatics (INDIN), 2014 12th IEEE In-
ternational Conference on, pages 274–279.
Gu, J., Purdom, P. W., Franco, J., and Wah, B. W.
(1999). Algorithms for the satisfiability (sat) problem.
Springer.
Jiang, Y., Kautz, H., and Selman, B. (1995). Solving prob-
lems with hard and soft constraints using a stochas-
tic algorithm for max-sat. In 1st International Joint
ICAART 2016 - 8th International Conference on Agents and Artificial Intelligence
286