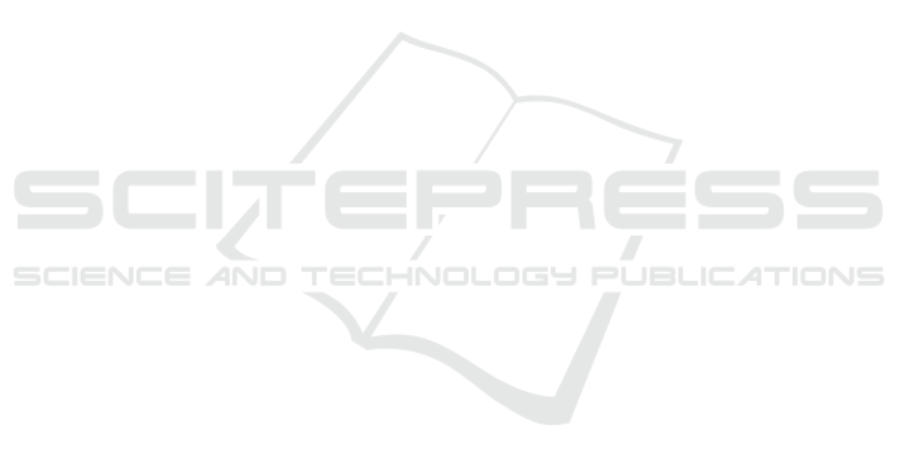
LaValle, S. M., Yershova, A., Katsev, M., and Antonov, M.
(2014). Head tracking for the oculus rift. In IEEE
International Conference on Robotics and Automation
(ICRA), pages 187 – 194, Hong Kong, China.
Moghadam, P. and Vidas, S. (2014). Heatwave: The next
generation of thermography devices. In International
Society for Optical Engineering (SPIE), volume 9105,
page 91050.
Nguyen, L., Bualat, M., Edwards, L., Flueckiger, L., Neveu,
C., Schwehr, K., Wagner, M., and Zbinden, E. (2001).
Virtual reality interfaces for visualization and control
of remote vehicles. Autonomous Robots, 11(1):59–68.
Okura, F., Ueda, Y., Sato, T., and Yokoya, N. (2013). Tele-
operation of mobile robots by generating augmented
free-viewpoint images. In IEEE and RSJ International
Conference on Intelligent Robots and Systems (IROS),
pages 665–671, Tokyo, Japan.
Ridao, P., Carreras, M., Hernandez, E., and Palomeras,
N. (2007). Underwater telerobotics for collabora-
tive research. In Ferre, M., Buss, M., Aracil, R.,
Melchiorri, C., and Balaguer, C., editors, Advances
in Telerobotics, volume 31 of Springer Tracts in Ad-
vanced Robotics, pages 347–359. Springer Berlin Hei-
delberg.
Saitoh, K., Machida, T., Kiyokawa, K., and Takemura, H.
(2006). A 2D-3D integrated interface for mobile robot
control using omnidirectional images and 3d geomet-
ric models. In IEEE and ACM International Sym-
posium on Mixed and Augmented Reality (ISMAR),
pages 173–176, Washington, DC, USA.
Stoll, E., Wilde, M., and Pong, C. (2009). Using virtual
reality for human-assisted in-space robotic assembly.
In World Congress on Engineering and Computer Sci-
ence, volume 2, San Francisco, USA.
Tomasi, C. and Manduchi, R. (1998). Bilateral filtering for
gray and color images. In IEEE International Con-
ference on Computer Vision (ICCV), pages 839–846,
Washington, DC, USA.
Vidas, S. and Moghadam, P. (2013). Heatwave: A hand-
held 3D thermography system for energy auditing. In
Energy and Buildings, volume 66, pages 445 – 460.
Vidas, S., Moghadam, P., and Bosse, M. (2013). 3D thermal
mapping of building interiors using an RGB-D and
thermal camera. In IEEE International Conference on
Robotics and Automation (ICRA), pages 2311–2318,
Karlsruhe, Germany.
Yong, L. S., Yang, W. H., and Jr, M. A. (1998). Robot task
execution with telepresence using virtual reality tech-
nology. In International Conference on Mechatronic
Technology, Hsinchu, Taiwan.
Zeise, B., Kleinschmidt, S. P., and B.Wagner (2015). Im-
proving the interpretation of thermal images with the
aid of emissivity’s angular dependency. In IEEE Inter-
national Symposium on Safety, Security, and Rescue
Robotics (SSRR), pages 1–8, West Lafayette, Indiana,
USA.
Zhang, Z. (1999). Flexible camera calibration by viewing
a plane from unknown orientations. In IEEE Inter-
national Conference on Computer Vision, volume 1,
pages 666–673, Kerkyra, Greece.
Zhang, Z. (2000). A flexible new technique for camera cali-
bration. In IEEE Transactions on Pattern Analysis and
Machine Intelligence, volume 22, pages 1330–1334.
GPU-accelerated Multi-sensor 3D Mapping for Remote Control of Mobile Robots using Virtual Reality
29