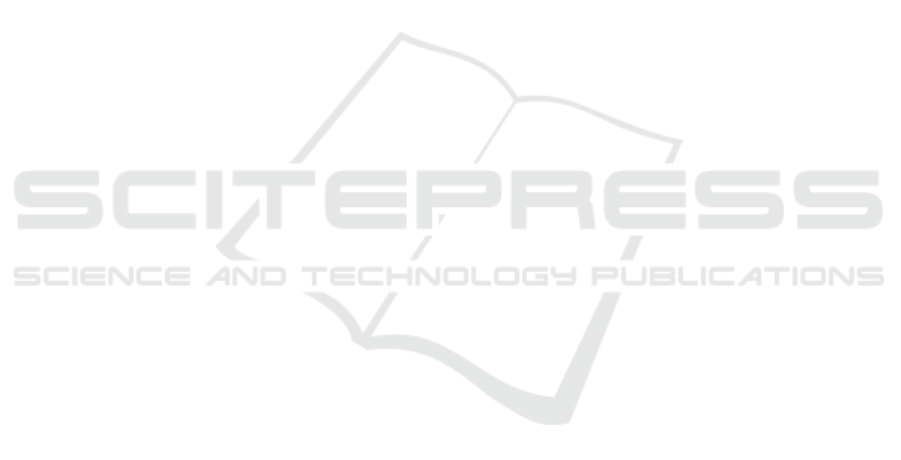
sually improved images to perform better due to the
absence of saturated and underexposed regions.
Evaluating the combinations we can also make
some assumptions about the relation within filters and
line detectors. Fast LSD and EDLines are little af-
fected by the kernel choices. In both single exposure
images and multi-exposure composed images, the re-
sults change less than 100 nanometers. LSWMS is af-
fected by the filter type when applied to HDR images.
Hough and PPHT, in the other hand, are highly af-
fected by the filter choice. Using a Gaussian low pass
filter reduces the detection rate, making the detector
fail in all cases. The median filter, also increases error
and variation, making the mean filter the best option.
Finally, the experiment results show that, even
though it is widely used in academic research, the
Hough transform can be replaced by modern, state-
of-the-art algorithms, improving both detection qual-
ity and computational complexity bounds.
6 CONCLUSIONS AND FUTURE
WORK
We present a system that integrates different tech-
niques to perform dimensional measurement of thick
steel plate bevels. We show how, using domain
knowledge, the extracted dimensions can be mapped
in control settings for the robotic welding equipment.
Unlike the previous approaches, it does not rely on
a single moving spot like laser trackers, nor a pat-
tern of spots like optical contact systems, neither a
line like laser scanners. No structured light or polar-
ized lenses are used. The approach is based on image
acquisition and processing making use of computer
vision algorithms. The groove modeling is achieved
through the use of line detection algorithms that look
for straight lines and segments. State-of-the-art al-
gorithms, such as Debevec’s HDR composition, Fast
LSD, PPHT, LSWMS and EDLines were tested on
real data to evaluate their capabilities.
Experimental results demonstrated that, using
carefully selected algorithm combinations, the system
can successfully extract the measurand dimensions.
The proposed approach has evident advantages over
the manual process that is used in shop floor nowa-
days, given that it can yield a large number of fea-
tures in a very short time using state of the art algo-
rithms, is not susceptible to the most frequent mea-
surement error sources and automatically controls the
welding equipment settings. In the same hand, we
also demonstrated obsolete and non-deterministic al-
gorithms could be replaced by state-of-the art alterna-
tives achieving better results at lower computational
cost.
We will be further exploring lighting options,
noise suppression algorithms and image composition
techniques to test how the achieved results can be im-
proved to surpass the precision requirements of the
welding industry. Previous studies have shown the
impact of illumination wavelength on enhancing or
suppressing desired properties on the image surface.
We believe it might also impact the image acquisition
on reflective surfaces. On the same hand, bilateral
filtering and image smoothing via L0 gradient mini-
mization (Xu et al., 2011), which have not been tested
yet due to their computational complexity bounds and
inability to perform in real-time on the proposed hard-
ware architecture, will be included in the compari-
son. Furthermore, Debevec’s multi-exposure image
composition will be compared to other recent ap-
proaches that minimize the computational cost and
are hardware-friendly.
In the long term, machine learning and deep learn-
ing will be used to extract information of the pro-
cess and produce a general purpose welding work-
cell. Therefore it must be able to identify the ma-
terial and it’s conditions; the environment variables
such as wind and humidity and incorporate the knowl-
edge that only experienced weldors today have. Stud-
ies have already been realized to map the main differ-
ences among senior and novice weldors and we intend
to use them to elevate the overall quality of the weld-
ing process.
ACKNOWLEDGEMENTS
This work was supported by National Counsel of
Technological and Scientific Development (CNPq),
Coordination for the Improvement of Higher Educa-
tion Personnel (CAPES) and Funding Authority for
Studies and Projects (FINEP).
REFERENCES
Akinlar, C. and Topal, C. (2011). Edlines: A real-time line
segment detector with a false detection control. Pat-
tern Recognition Letters, 32(13):1633–1642.
Ang Jr, M. H., Lin, W., and Lim, S.-Y. (1999). A
walk-through programmed robot for welding in ship-
yards. Industrial Robot: An International Journal,
26(5):377–388.
BIPM, I., IFCC, I., ISO, I., and IUPAP, O. (2008). Evalua-
tion of measurement data – guide to the expression of
uncertainty in measurement.
De Xu, Min Tan, X. Z. Z. T. (2004). Seam tracking and
visual control for robotic arc welding based on struc-
Welding Groove Mapping - Implementation and Evaluation of Image Processing Algorithms on Shiny Surfaces
333