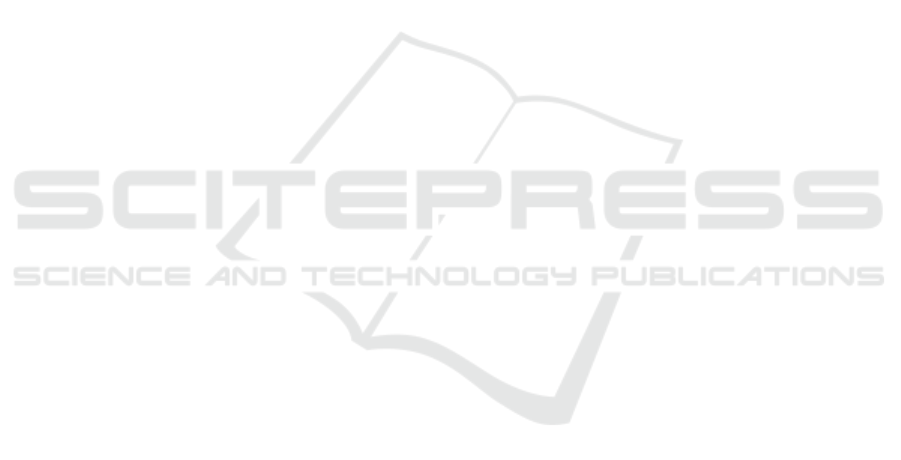
nition, 2009. CVPR 2009. IEEE Conference on, pages
1271–1278. IEEE.
Dogar, M. and Srinivasa, S. (2011). A framework for push-
grasping in clutter. Robotics: Science and Systems
VII.
Edsinger, A. and Kemp, C. C. (2006). Manipulation in hu-
man environments. In Humanoid Robots, 2006 6th
IEEE-RAS International Conference on, pages 102–
109. IEEE.
Fisher, M. and Hanrahan, P. (2010). Context-based search
for 3d models. In ACM Transactions on Graphics
(TOG), volume 29, page 182. ACM.
Flusser, J. (1995). Object matching by means of matching
likelihood coefficients. Pattern Recognition Letters,
16(9):893–900.
Fu, H., Cohen-Or, D., Dror, G., and Sheffer, A. (2008).
Upright orientation of man-made objects. In ACM
transactions on graphics (TOG), volume 27, page 42.
ACM.
Glover, J., Bradski, G., and Rusu, R. B. (2012). Monte carlo
pose estimation with quaternion kernels and the bing-
ham distribution. In Robotics: science and systems,
volume 7, page 97.
Hsiao, K., Nangeroni, P., Huber, M., Saxena, A., and Ng,
A. Y. (2009). Reactive grasping using optical prox-
imity sensors. In Robotics and Automation, 2009.
ICRA’09. IEEE International Conference on, pages
2098–2105. IEEE.
Jiang, H. and Yu, S. X. (2009). Linear solution to scale
and rotation invariant object matching. In Computer
Vision and Pattern Recognition, 2009. CVPR 2009.
IEEE Conference on, pages 2474–2481. IEEE.
Jiang, Y., Moseson, S., and Saxena, A. (2011). Efficient
grasping from rgbd images: Learning using a new
rectangle representation. In Robotics and Automa-
tion (ICRA), 2011 IEEE International Conference on,
pages 3304–3311. IEEE.
Koppula, H. S., Anand, A., Joachims, T., and Saxena, A.
(2011). Semantic labeling of 3d point clouds for in-
door scenes. In Advances in Neural Information Pro-
cessing Systems, pages 244–252.
Kouskouridas, R. and Gasteratos, A. (2012). Establishing
low dimensional manifolds for 3d object pose estima-
tion. In Imaging Systems and Techniques (IST), 2012
IEEE International Conference on, pages 425–430.
IEEE.
Li, H., Kim, E., Huang, X., and He, L. (2010). Object
matching with a locally affine-invariant constraint. In
Computer Vision and Pattern Recognition (CVPR),
2010 IEEE Conference on, pages 1641–1648. IEEE.
Miller, A. T., Knoop, S., Christensen, H., Allen, P. K.,
et al. (2003). Automatic grasp planning using shape
primitives. In Robotics and Automation, 2003. Pro-
ceedings. ICRA’03. IEEE International Conference
on, volume 2, pages 1824–1829. IEEE.
Nalpantidis, L., Bj
¨
orkman, M., and Kragic, D. (2012). Yes-
yet another object segmentation: Exploiting camera
movement. In Intelligent Robots and Systems (IROS),
2012 IEEE/RSJ International Conference on, pages
2116–2121. IEEE.
Rietzler, A., Detry, R., Kopicki, M., Wyatt, J. L., and Piater,
J. (2013). Inertially-safe grasping of novel objects. In
Cognitive Robotics Systems: Replicating Human Ac-
tions and Activities (Workshop at IROS 2013).
Sapna Varshney, S., Rajpa, N., and Purwar, R. (2009). Com-
parative study of image segmentation techniques and
object matching using segmentation. In Methods and
Models in Computer Science, 2009. ICM2CS 2009.
Proceeding of International Conference on, pages 1–
6. IEEE.
Saxena, A., Chung, S. H., and Ng, A. Y. (2008). 3-d depth
reconstruction from a single still image. International
journal of computer vision, 76(1):53–69.
Saxena, A., Driemeyer, J., Kearns, J., and Ng, A. Y. (2006).
Robotic grasping of novel objects. In Advances in
neural information processing systems, pages 1209–
1216.
Saxena, A., Driemeyer, J., and Ng, A. Y. (2009). Learn-
ing 3-d object orientation from images. In Robotics
and Automation, 2009. ICRA’09. IEEE International
Conference on, pages 794–800. IEEE.
Schuster, M. J., Okerman, J., Nguyen, H., Rehg, J. M., and
Kemp, C. C. (2010). Perceiving clutter and surfaces
for object placement in indoor environments. In Hu-
manoid Robots (Humanoids), 2010 10th IEEE-RAS
International Conference on, pages 152–159. IEEE.
Suzuki, S. et al. (1985). Topological structural analy-
sis of digitized binary images by border following.
Computer Vision, Graphics, and Image Processing,
30(1):32–46.
Toussaint, M., Plath, N., Lang, T., and Jetchev, N. (2010).
Integrated motor control, planning, grasping and high-
level reasoning in a blocks world using probabilistic
inference. In Robotics and Automation (ICRA), 2010
IEEE International Conference on, pages 385–391.
IEEE.
Viola, P. and Jones, M. (2001). Robust real-time object
detection. International Journal of Computer Vision,
4:51–52.
Xiong, X. and Huber, D. (2010). Using context to create se-
mantic 3d models of indoor environments. In BMVC,
pages 1–11.
Vision-based Robotic System for Object Agnostic Placing Operations
475