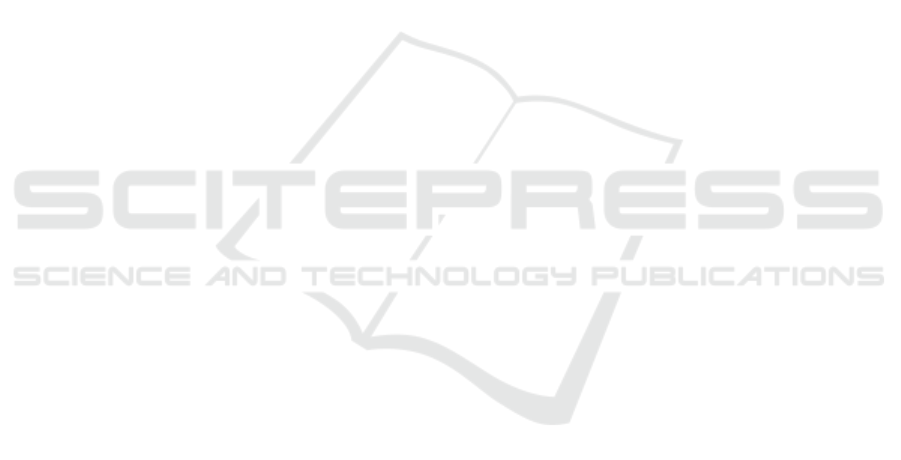
5 CONCLUSIONS
In this work, we evaluate the performance of a
pyramid-based foveated matcher in terms of both ac-
curacy and efficiency, in the context of robotic cloth
manipulations. By conducting simulations of cloth
wrinkles we obtained depth map ground-truths for
our evaluation. Using this simulated dataset, we
found that foveated matching is effective in trading
off accuracy for efficiency for stereo matching perfor-
mance. In addition, by assuming the robotic behav-
ior described in prior work, we found that the use of
foveation can allow high accuracy for robotic cloth
flattening and grasping tasks with a two to three fold
speed gain.
Note that our work has several limitations: firstly,
we assume that there is only one wrinkle on the cloth.
Secondly, we assume a certain stereo matching accu-
racy is required to achieve the robotic manipulation
tasks. This might vary according to different cloth
materials, wrinkle properties, etc. We leave the work
of dealing with more real cloth wrinkles with real
robotic manipulations (various tasks) as future work.
REFERENCES
Aragon-Camarasa, G., Oehler, S. B., Liu, Y., Li, S.,
Cockshott, P., and Siebert, J. P. (2013). Glasgow’s
stereo image database of garments. arXiv preprint
arXiv:1311.7295.
Barron, J. L., Fleet, D. J., and Beauchemin, S. S. (1994).
Performance of optical flow techniques. International
journal of computer vision, 12(1):43–77.
Bernardino, A. and Santos-Victor, J. (2002). A binocular
stereo algorithm for log-polar foveated systems. In
Biologically Motivated Computer Vision, pages 127–
136. Springer.
Bersch, C., Pitzer, B., and Kammel, S. (2011). Bi-
manual robotic cloth manipulation for laundry fold-
ing. In Intelligent Robots and Systems (IROS), 2011
IEEE/RSJ International Conference on, pages 1413–
1419. IEEE.
Boyling, T. and Siebert, J. (2000). A fast foveated stereo
matcher. In Proc. Conf. on Imaging Science Systems
and Technology, pages 417–423.
Cusumano-Towner, M., Singh, A., Miller, S., O’Brien,
J. F., and Abbeel, P. (2011). Bringing clothing into
desired configurations with limited perception. In
Robotics and Automation (ICRA), 2011 IEEE Inter-
national Conference on, pages 3893–3900. IEEE.
Cutkosky, M. R. (2012). Robotic grasping and fine manipu-
lation, volume 6. Springer Science & Business Media.
Doumanoglou, A., Kim, T.-K., Zhao, X., and Malassio-
tis, S. (2014). Active random forests: An applica-
tion to autonomous unfolding of clothes. In Computer
Vision–ECCV 2014, pages 644–658. Springer.
Hartley, R. I. and Sturm, P. (1997). Triangulation. Computer
vision and image understanding, 68(2):146–157.
Maitin-Shepard, J., Cusumano-Towner, M., Lei, J., and
Abbeel, P. (2010). Cloth grasp point detection based
on multiple-view geometric cues with application to
robotic towel folding. In Robotics and Automa-
tion (ICRA), 2010 IEEE International Conference on,
pages 2308–2315. IEEE.
Mei, X., Sun, X., Zhou, M., Jiao, S., Wang, H., and Zhang,
X. (2011). On building an accurate stereo matching
system on graphics hardware. In Computer Vision
Workshops (ICCV Workshops), 2011 IEEE Interna-
tional Conference on, pages 467–474. IEEE.
Ramisa, A., Alenya, G., Moreno-Noguer, F., and Torras, C.
(2012). Using depth and appearance features for in-
formed robot grasping of highly wrinkled clothes. In
Robotics and Automation (ICRA), 2012 IEEE Interna-
tional Conference on, pages 1703–1708. IEEE.
Scharstein, D., Hirschm
¨
uller, H., Kitajima, Y., Krathwohl,
G., Ne
ˇ
si
´
c, N., Wang, X., and Westling, P. (2014).
High-resolution stereo datasets with subpixel-accurate
ground truth. In Pattern Recognition, pages 31–42.
Springer.
Scharstein, D. and Szeliski, R. (2002). A taxonomy and
evaluation of dense two-frame stereo correspondence
algorithms. International Journal of Computer Vision,
47(1-3):7–42.
Sun, L., Aragon-Camarasa, G., Rogers, S., and Siebert, J.
(2015). Accurate garment surface analysis using an
active stereo robot head with application to dual-arm
flattening. In Robotics and Automation (ICRA), 2015
IEEE International Conference on, pages 185–192.
Van Den Berg, J., Miller, S., Goldberg, K., and Abbeel, P.
(2011). Gravity-based robotic cloth folding. In Algo-
rithmic Foundations of Robotics IX, pages 409–424.
Springer.
Willimon, B., Birchfield, S., and Walker, I. (2011a). Clas-
sification of clothing using interactive perception. In
Robotics and Automation (ICRA), 2011 IEEE Interna-
tional Conference on, pages 1862–1868. IEEE.
Willimon, B., Birchfield, S., and Walker, I. D. (2011b).
Model for unfolding laundry using interactive percep-
tion. In IROS, pages 4871–4876.
Xu, T. and Cockshott, P. (2015). Guided filtering based
pyramidical stereo matching for unrectified images.
In Image and Vision Computing New Zealand, In-
ternational Conference, IVCNZ 2015, Auckland, New
Zealand.
Xu, T., Cockshott, P., and Oehler, S. (2014). Acceleration of
stereo-matching on multi-core cpu and gpu. In IEEE
Intl Conf on High Performance Computing and Com-
munications, pages 108–115. IEEE.
VISAPP 2016 - International Conference on Computer Vision Theory and Applications
664