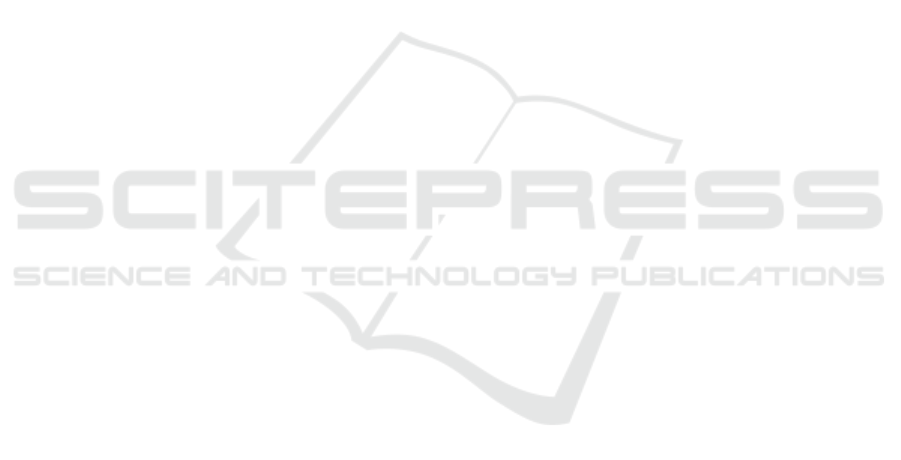
With the help of this information, the test model can
be improved to get near 100% test coverage in consid-
eration of the customer use cases. Domain knowledge
is the key for computing user realistic paths. Unre-
alistic paths only have to be checked referring their
impact on customer functions and common bugs.
A similar approach with focus of ’automation,
modularization and compatibility of all equipment to
do measurement, calibration and diagnosis’ (ASAP,
1999) is the Can Calibration Protocol (CCP). The Pro-
tocol is used for calibration and data acquisition. Re-
alized as a driver with access to the internal ECU
memory this part of the protocol has a similar effect
on the CPU load as the introduced approach. During a
session using CCP a ’continuous logical connection’
(ASAP, 1999) is established to transfer data from the
ECU to the master device (off board test automation).
This approach has a substantial similarity in the
connection layer: both interact at the driver layer.
However, according to the illustrated approach the
CCP has the main goal of data acquisition in contrast
to data simulation. With the enormous difference of
cutting the data communication to the agent (slave)
the new approach is, in case of simulation, way nearer
to the customer case.
3 CONCLUSIONS
The method of integrated hardware signal simulation,
with an integrated software approach, allows to sim-
ulate the user input analogous to the customer use
cases and thereby to compare system- and test model
in an innovative way. The approach shows a differ-
ent solution with no need of special hardware equip-
ment because of the integration of the simulation in
the distributed system as a distributed system. Real-
ized as a standard module for easy integration in the
AUTOSAR basic software to get an interface for sim-
ulation. The key aspect is the point of interaction lo-
cated in the AUTOSAR driver layer. The approach
uses an abstraction to simplify the data to generic sig-
nal sequences as well as to be able to adapt easily to
different hardware configurations.
A simple generic simulation module controls the
process of simulation, because of its simplicity the
simulation does not have a measurable effect on the
processor workload. The total system reaction, re-
spectively the system interaction with the environ-
ment and customer will be evaluated with proven and
tested methods, already in use. Therefore, there is no
need in building up new evaluation methods.
Next steps for the simulation approach are to
check the data size of the simulation sequences, es-
pecially for long term simulations, considering of the
limited memory space in automotive ECUs. This fact
is the main limitation for the length of data sequences
at this time.
REFERENCES
ASAP (1999). Can calibration protocol - version 2.1.
AUTOSAR Partnership (2014). Autosar components.
Balzert, H. and Ebert, C. (2008). Lehrbuch der
Sofwaretechnik. Spektrum Akademischer Verlag, Hei-
delberg, 2 edition.
Beizer, B. (1990). Software testing techniques. International
Thomson Computer Press, New York, 2 edition.
Byhlin, S., Ermedahl Jan Gustafsson, A., and Lisper, B. Ap-
plying Static WCET Analysis to Automotive Commu-
nication Software.
Eigner, M. and Stelzer, R. (2013). Product-Lifecycle-
Management. VDI. Springer, Berlin, Heidelberg, 2
edition.
Hoffmann, D. W. (2008). Software-Qualit
¨
at. EXa-
men.press. Springer, Berlin, Heidelberg.
K
¨
oberl, M. (2015). Integration softwarebasierter automa-
tisierungsmethoden in eine test-ecu. Master’s thesis,
University of Augsburg, Augsburg.
Myers, G. J., Sandler, C., and Badgett, T. (2012). The art of
software testing. John Wiley & Sons, Hoboken, N.J,
3 edition.
Pezz
`
e, M. and Young, M. (2008). Software testing and
analysis. Process, principles, and techniques. Wiley,
[Hoboken, N.J.].
Roßner, T. (2010). Basiswissen modellbasierter Test.
dpunkt.verl., Heidelberg, 1 edition.
Saad, C. and Bauer, B. (2011). Industry track of soft-
ware language engineering (itsle), 4th international
conference on software language engineering (sle
2011)(may 2011). The Model Analysis Framework
An IDE for Static Model Analysis.
Saad, C. and Bauer, B. (2013). Model-driven engi-
neering languages and systems. Data-Flow Based
Model Analysis and Its Applications, pages 707–723.
Springer.
Seidl, R., Baumgartner, M., and Bucsics, T. (2011). Prax-
iswissen Testautomatisierung. Basiswissen Testau-
tomatisierung. dPunkt.
Vector Informatik GmbH (2013). Autosar configuration
process - how to handle 1000s of parameters.
MODELSWARD 2016 - 4th International Conference on Model-Driven Engineering and Software Development
662