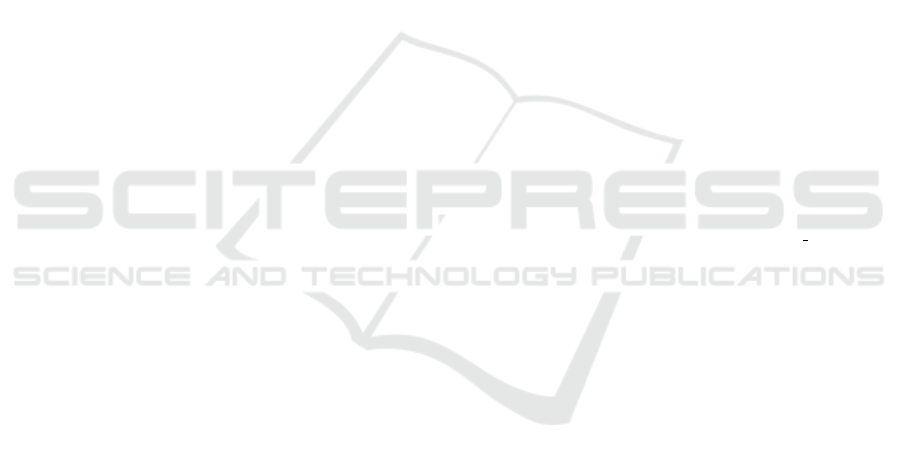
ures and breakdowns. More specialised processes
allowing controlled fork/join are also required.
• identification of model parameters easing the
manual (and later optimised) exploration of risk
mitigation strategies.
• availability of a company library of specific risks
and related probes
• produce specific reporting (e.g. business continu-
ity plans). We have already explored some work
in this direction (Arenas et al., 2015).
• possibly support model refinements and granular-
ity of simulation. However our aim is not to cap-
ture the full reality but what will help assessing
identified risks.
• parallelisation in case of need of faster simulation
times. This is easy to implement.
Our framework combining usability, expressive-
ness and efficiency is an important milestone in our
work to raise the awareness of companies, especially
of smaller size, w.r.t. the need to evaluate their pro-
curement risks and elaborate their supplying policies
in the most optimal way. We believe it can be used to
manage more general risks. Our design ideas can also
be used to improve other risk management tools. Our
framework is available online (SimQRi, 2015) and is
planned for Open Source release.
ACKNOWLEDGEMENTS
This research was conducted under the SimQRi
research project (ERA-NET CORNET, Grant No.
1318172). The CORNET promotion plan of the Re-
search Community for Management Cybernetics e.V.
(IfU) has been funded by the German Federation of
Industrial Research Associations (AiF), based on an
enactment of the German Bundestag.
REFERENCES
Almeder, C., Preusser, M., and Hartl, R. F. (2009). Simula-
tion and optimization of supply chains: alternative or
complementary approaches? In G
¨
unther, H. O. and
Meyr, H., editors, Supply Chain Planning. Springer-
Verlag.
AnyLogic (2015). AnyLogic Multimethod Simulation Soft-
ware. http://www.anylogic.com.
Arenas, A. E., Massonet, P., and Ponsard, C. (2015). Goal-
oriented requirement engineering support for business
continuity planning. In Proceedings of MReBA’15,
Stockholm, Sweden.
Artikis, C. and Artikis, P. (2015). Probability Distributions
in Risk Management Operations. Springer, London.
Brailsford, S., Churilov, L., and Dangerfield, B. (2014).
Discrete-Event Simulation and Systems Dynamics for
Management Decision Making. Wiley.
Byong-Kyu, C. and Donghun, K. (2013). Modeling and
Simulation of Discrete-Event Systems. Wiley.
Deleris, L. and Erhun, F. (2005). Risk management in sup-
ply networks using Monte-Carlo simulation. In 2005
Winter Simulation Conference, Orlando, USA.
Finke, G. R., Schmitt, A., and Singh, M. (2010). Modeling
and simulating supply chain schedule risk. In 2010
Winter Simulation Conference, Baltimore, USA.
Gleißner, W. (2012). Quantitative methods for risk manage-
ment in the real estate development industry. In Jour-
nal of Property Investment & Finance, volume 30(6),
pages 612–630.
Klimov, R. A. and Merkuyev, Y. A. (2006). Simulation-
based risk measurement in supply chains. In 20th
European Conference on Modelling and Simulation
(ECMS 2006), Bonn, Germany.
OscaR (2012). OscaR: Scala in OR.
https://bitbucket.org/oscarlib/oscar.
Printz, S., von Cube, J. P., Vossen, R., Schmitt, R.,
and Jeschke, S. (2015a). Ein kybernetisches mod-
ell beschaffungsinduzierter st
¨
org
¨
oßen. In Exploring
Cybernetics - Kybernetik im interdisziplinren Diskurs.
Springer Spektrum.
Printz, S., von Cube, P., and Ponsard, C.
(2015b). Management of procurement risks
on manufacturing processes - survey results.
http://simqri.com/uploads/media/Survey Results.pdf.
Rockwell Automation (2015). Arena Simulation Software.
https://www.arenasimulation.com.
Romeike, F. (2004). Der prozess der risikosteuerung und -
kontrolle. In Romeike, F., editor, Erfolgsfaktor Risiko-
Management, pages 236–243. Gabler, Wiesbaden.
Schmitt, A. and Singh, M. (2009). Quantifying supply chain
disruption risk using Monte Carlo and discrete-event
simulation. In 2009 Winter Simulation Conference,
Austin, USA.
Siemens (2015). Plant Simulator.
http://goo.gl/NK7yWg.
Siepermann, M. (2008). Risikokostenrechnung: Erfolgre-
iche Informationsversorgung und Risikopr
¨
avention.
Erich Schmidt, Berlin.
SimQRi (2015). Online SimQRi tool.
https://simqri.cetic.be.
Sutton, I. (2015). Process Risk and Reliability Management.
Elsevier, second edition.
von Cube, J. P., Abbas, B., Schmitt, R., and Jeschke, S.
(2014). A monetary approach of risk management in
procurement. In 7th Int. Conf. on Production Research
Americas’ 2014, pages 35–40, Lima, Peru.
Zio, E. (2013). The Monte Carlo Simulation Method for
System Reliability and Risk Analysis. Springer, Lon-
don.
Zsidisin, G. A. and Ritchie, B. (2009). Supply Chain Risk:
A Handbook of Assessment, Management, and Perfor-
mance. Springer.
ICORES 2016 - 5th International Conference on Operations Research and Enterprise Systems
322