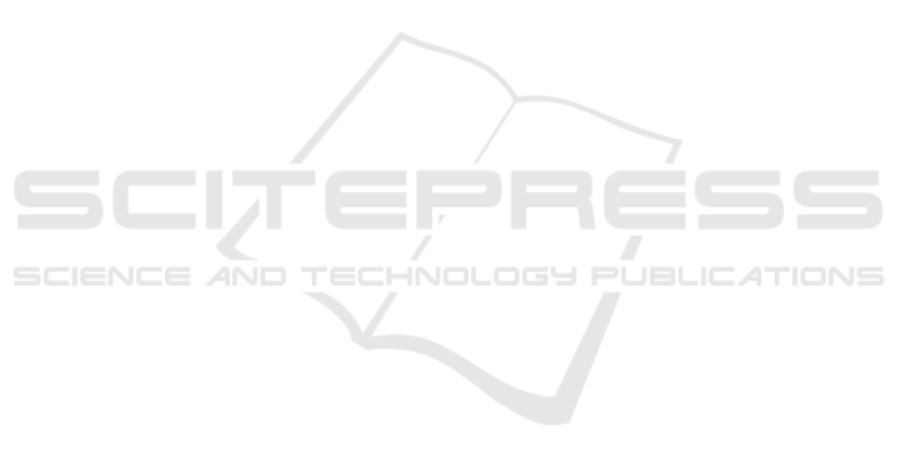
The main contributions of this paper are:
• provide an overview of thermal storage simulation
models
• develop models for prediction of the state of
charge and charging power consumption
• validate accuracy of model predictions with ex-
perimental data
This paper is structured as follows: Section 2 dis-
cusses related work on mathematical models for pre-
diction of storage state of charge. Section 3 describes
the model and validation experiments. A comparison
of model prediction and experimental results is shown
and discussed in Section 4, in which also results of a
case study are presented which demonstrates applica-
tion of the model. Finally, Section 5 draws conclu-
sions and introduces future work.
2 RELATED WORK
The behavior of a thermal storage during standstill,
charging and discharging is studied by numerous au-
thors. One of most important aspects of a thermal
storage is thermal stratification, as this leads to max-
imum exergy utilization (Rosen, 2001). An overview
of research into thermal stratification is reported by
(Han et al., 2009), while (Fan and Furbo, 2012) re-
ports on the influence of heat loss on thermal stratifi-
cation.
Predictive modeling for the temperature distribution
within a thermal storage in relation to inlet and out-
let flows is a well investigated area. This concerns
mainly one-dimensional models, e.g. the lumped ca-
pacitance multi-node approximation (Kleinbach et al.,
1993) which is implemented in simulation software
like TRNSYS. Good results are obtained by approx-
imating the thermal storage with at least 15 nodes
or uniform temperature layers. An even more de-
tailed approach of temperature distribution and flow
patterns within the storage is possible with a two-
dimensional, finite volume model which includes
natural and mixed convection boundary conditions
(Oliveski et al., 2003). The one and two-dimensional
approaches are computationally expensive mainly be-
cause of the small time intervals, e.g. seconds to min-
utes required for simulation. For smart control of
the storage and heat pump, such a detailed knowl-
edge of the temperature distribution is not required.
Also, time intervals used in smart control are much
larger, e.g. 15 minutes to 1 hour. (Halvgaard et al.,
2012) uses a lumped capacitance single node model
of a thermal storage for model predictions as part of
a smart control system. This model essentially de-
scribes energy content of the storage and is also in-
troduced by others (Kriett and Salani, 2012), (Henze
et al., 2004). This model is straightforward to apply
for model predictions as part of smart control, how-
ever the relation between heat pump performance and
lower temperatures within the bottom part of a ther-
mally stratified storage is lost. Hence, prediction of
electricity consumption in time, one of the most im-
portant goals of the predictions, is less accurate.
A grey-box model with system identification
method is proposed by (De Ridder and Coomans,
2014). The model is the same one-dimensional multi-
node approximation discussed earlier but in this case,
5 nodes are proposed together with a parameter iden-
tification method based on the Markov-chain Monte-
Carlo method. Although the results of this method
are reasonable, we foresee two problems in our ap-
plications: (1) such identification algorithms are dif-
ficult to apply within low cost embedded device con-
trollers with limited available memory and computa-
tional power, (2) even with only 5 nodes, for accuracy
reasons, evaluation of the model prediction involves
time intervals in the order of minutes rather than 15
minutes to 1 hour.
An iterative model which approximates the stor-
age into two layers, one hot layer at the top and one
mixed layer with an average temperature below that
is reported in (Baeten et al., 2015). This approach is
promising and is partly the basis for the present paper.
Our model predicts without iterations both the storage
state of charge and heat pump electric consumption of
a future charging cycle in a one step calculation, based
on available data of the inlet/outlet flows.
3 METHODS
A general and widely applicable model for the supply
from a thermal storage or electric battery is based on
energy conservation which states:
∆S
t
= ∆C
t
− ∆D
t
− ∆L
t
(1)
In which the term ∆S
t
signifies the change of stored
energy, ∆C
t
the charged energy, ∆D
t
the demand and
∆L
t
the energy loss, all within a time interval ∆t which
in discrete time is the interval (t −1, t). In the follow-
ing, the terms in Equation 1 will be discussed.
3.1 Type of Thermal Storage
A common storage configuration for domestic hot
water supply is shown in Figure 1 for which the
mathematical notations are explained in Table 1.
Cold water flows in at the bottom, hot water is drawn
A Predictive Model for Smart Control of a Domestic Heat Pump and Thermal Storage
137