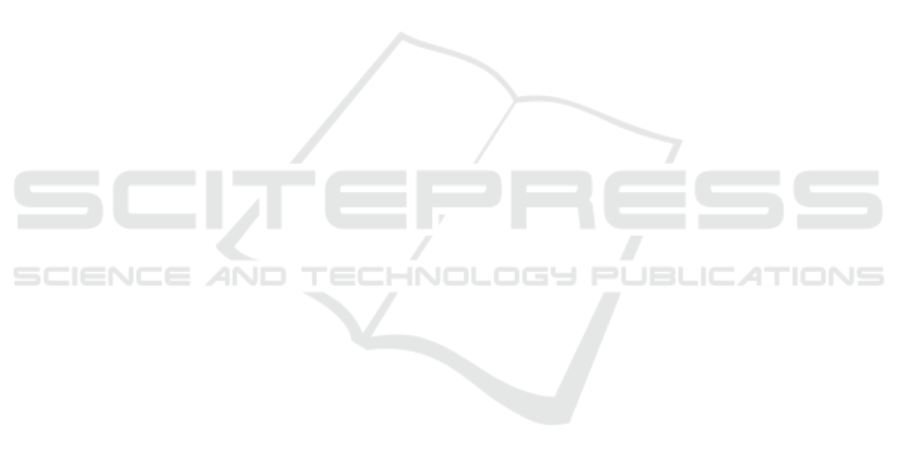
Ennigrou, M. and Ghedira, K. (2008). New local diver-
sification techniques for flexible job shop schedul-
ing problem with a multi-agent approach. In
In Autonomous Agents and Multi-Agent Systems,
vol.17(2),270-287.
Gajpal, Y.and Rajendran, C. and Ziegler, H. (2006). . an
ant colony algorithm for scheduling in flowshops with
sequence-dependent setup times of jobs. In Int J of
Advanced Manufacturing Technology 30 (5-6), 416-
424.
Garey, M. R., Johnson, D. S., and Stockmeyer, L. (1976).
Some simplified np-complete graph problems. In The-
oretical computer science, 1(3), 237-267.
Gonz
´
alez, M.
´
A.and Rodr
´
ıguez Vela, C. and Varela, R.
(2013). An efficient memetic algorithm for the flex-
ible job shop with setup times. In InTwenty-Third In-
ternational Conference on Automated Planning and
Scheduling pp 91-99.
Holland, J. (1975). Adaptation in natural and artificial sys-
tem. In MIT University of Michigan Press, Ann Arbor.
Hurink, J., Jurisch, B., and Thole, M. (1994). Tabu search
for the job-shop scheduling problem with multi-
purpose machines. In Operations-Research-Spektrum,
15(4), 205-215.
Imanipour, N. (2006). Modeling & solving flexible job shop
problem with sequence dependent setup times. In In-
ternational Conference on Service Systems and Ser-
vice Management (Vol. 2, pp. 1205-1210). IEEE.
Kacem, I.and Hammadi, S. and Borne, P. (2002). Approach
by localization and multiobjective evolutionary opti-
mization for flexible job-shop scheduling problems. In
Syst IEEE Syst Man Cybern 32(1):1-13.
Kaweegitbundit, P. (2011). Comparison of heuristic for flow
shop scheduling problems with sequence dependent
setup time. In Advanced Materials Research 339 (1),
332-335.
Kim, S. C. and Bobrowski, P. M. (1994). Impact of
sequence-dependent setup time on job shop schedul-
ing performance. In The International Journal of Pro-
duction Research, 32(7), 1503-1520.
Li, X. and Zhang, Y. (2012). Adaptive hybrid algorithms for
the sequence-dependent setup time permutation flow
shop scheduling problem. In IEEE Transactions on
Automation Science and Engineering 9(3), 578-595.
Mirabi, M. (2011). Ant colony optimization technique for
the sequence-dependent flowshop scheduling prob-
lem. In Int J of Advanced Manufacturing Technology
55 (1-4), 317-326.
Mirabi, M. (2014). A novel hybrid genetic algorithm to
solve the sequence-dependent permutation flow-shop
scheduling problem. In International Journal of Ad-
vanced Manufacturing Technology 74 (1-4), 429-437.
Moghaddas, R. and Houshmand, M. (2008). Job-shop
scheduling problem with sequence dependent setup
times. In Proceedings of the International MultiCon-
ference of Engineers and Computer Scientists, Vol II.
Mousakhani, M. (2013). Sequence-dependent setup time
flexible job shop scheduling problem to minimise to-
tal tardiness. In International Journal of Production
Research, 51(12), 3476-3487.
Naderi, B.and Zandieh, M. and Ghomi, S. F. (2009).
Scheduling sequence-dependent setup time job shops
with preventive maintenance. In The Interna-
tional Journal of Advanced Manufacturing Technol-
ogy, 43(1-2), 170-181.
Nuijten, W. P. and Aarts, E. H. (1996). A computational
study of constraint satisfaction for multiple capaci-
tated job shop scheduling. In European Journal of
Operational Research, 90(2), 269-284.
Oddi, A., Rasconi, R., Cesta, A., and Smith, S. (2011).
Applying iterative flattening search to the job shop
scheduling problem with alternative resources and se-
quence dependent setup times. In In COPLAS 2011
Proceedings of the Workshopon Constraint Satisfac-
tion Techniques for Planning and Scheduling Prob-
lems.
Pezzella, F., Morganti, G., and Ciaschetti, G. (2008). A
genetic algorithm for the flexible job-shop schedul-
ing problem. In Computers & Operations Re-
search,35(10), 3202-3212.
Rossi, A. (2014). Flexible job shop scheduling with
sequence-dependent setup and transportation times by
ant colony with reinforced pheromone relationships.
In International Journal of Pro-duction Economics,
153, 253-267.
Sadrzadeh, A. (2013). Development of both the ais and
pso for solving the flexible job shop scheduling prob-
lem. In Arabian Journal for Science and Engineering,
38(12), 3593-3604.
Saidi-Mehrabad, M. and Fattahi, P. (2007). Flexible job
shop scheduling with tabu search algorithms. In
The International Journal of Advanced Manufactur-
ing Technology, 32(5-6), 563-570.
Santos, N., Rebelo, R., and Pedroso, J. (2014). A tabu
search for the permutation flow shop problem with se-
quence dependent setup times. In International Jour-
nal of Data Analysis Tech-niques and Strategies 6 (3),
275-285.
Turkyllmaz, A. and Bulkan, S. (2014). A hybrid algorithm
for total tardiness minimisation in flexible job shop:
genetic algorithm with parallel vns execution. In In-
ternational Journal of Production Research, 53(6),
1832-1848.
Varmazyar, M. and Salmasi, N. (2012). Minimizing the
number of tardy jobs in flow shop sequence dependent
setup times scheduling problem. In Applied Mechan-
ics and Materials 110-116, 4063-4069.
Zhang, G., Gao, L., and Shi, Y. (2011). An effective genetic
algorithm for the flexible job-shop scheduling prob-
lem. In Expert Syst. Appl. 38(4)3563-3573.
Zhou, Y., Beizhi, L., and Yang, J. (2006). Study on job shop
scheduling with sequence-dependent setup times us-
ing biological immune algorithm. In Int J Adv Manuf
Technol 30:105-111.
Ziaee, M. (2014). A heuristic algorithm for solving flexi-
ble job shop scheduling problem. In Int Adv Manuf
Technol 71: 519.
Flexible Job-shop Scheduling Problem with Sequence-dependent Setup Times using Genetic Algorithm
53