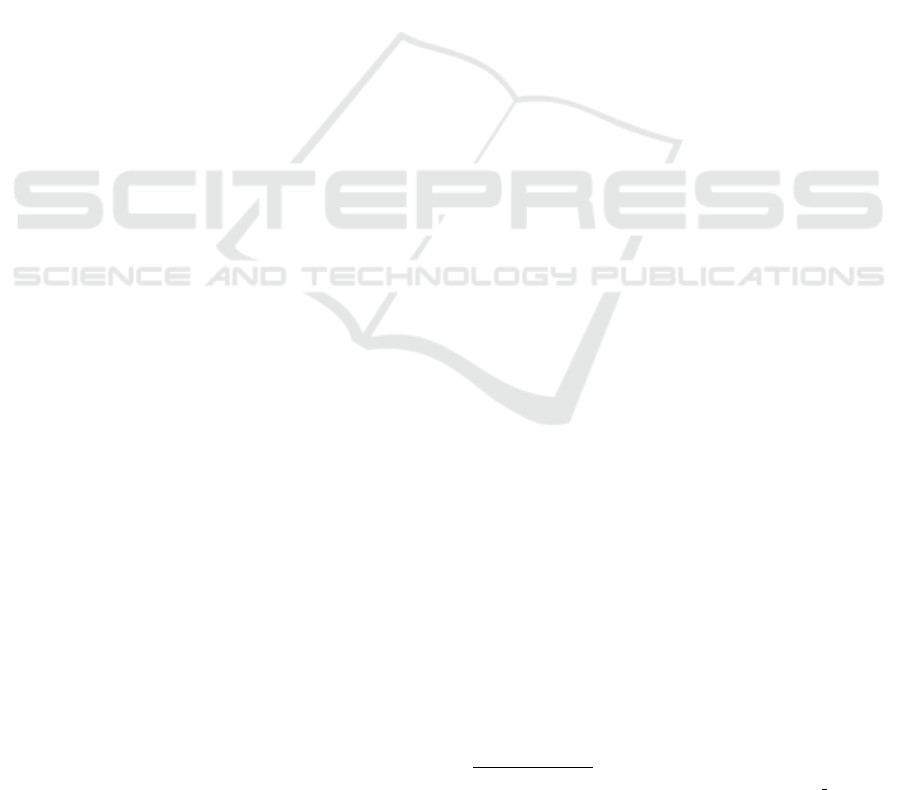
and leading to more than 70% reduction of develop-
ment effort and field claims (Clements and Northrop,
2001; Flores et al., 2013). GM’s Software Product-
line is probably one of the most complex product-
lines with tens of concurrent development streams for
approximately 300 hierarchical subsystems with over
3000 engineers contributing to the development.
The main challenge facing automotive OEMs is to
bring new complex vehicle features quickly into mar-
ket, ahead of the competition while meeting the ex-
pected standards of reliability, dependency, security,
and cost. While similar challenges exist in other in-
dustries as well (e.g. Aerospace), what distinguishes
the automotive industry is its (mostly) high volumes,
the huge number of variants, the very stringent cost
constraints, and the cut-throat competition. In or-
der to address this challenge, the industry as a whole
and GM in particular, have been adopting a variety of
strategies. These include a strong focus and rigorous
documentation of system and feature requirements,
model-based development of driver-facing features,
the product-line approach to software development,
a system engineering approach to safety and relia-
bility, the adoption of a standardized Software Ar-
chitecture platform (based upon AUTOSAR - AU-
Tomotive Open System ARchitecture (AUTOSAR,
2003)), traceability across different life-cycle arte-
facts and extensive verification and validation at dif-
ferent stages of development. In addition, GM is also
looking at methodologies, methods, and tools for the
early assessment and optimization of the E/E archi-
tecture platforms that are optimized for cost and other
metrics to support the features being developed.
The management and development of such com-
plex systems must be handled with appropriate
methodologies, methods and tools. A few strategies
that have yielded good amount of success to GM
and other auto companies are model-based design of
features, a product line engineering approach to E/E
design, and virtual development and integration of
E/E architectures. These methodologies and related
modeling and tool technologies are different in focus
and maturity. Model-based design of features is sup-
ported by mature tools like Mathworks’s Simulink/SF
(www.mathworks.com), dSpace’s Hardware-in-Loop
(HIL) simulation (www.dpsace.com) and has be-
come quite main stream in the automotive indus-
try. The product line approach is supported by
tools such as Gears from BigLever for variant man-
agement (www.biglever.com), and the IBM suite
of tools DOORS, RTC and Synergy for require-
ment capture, and configuration management(see
www.ibm.com for more details on these tools). This
approach is largely in the deployment and accep-
tance stage in the majority of the OEMs. The
Virtual Development of Controls and Calibrations
strategy extends the simulation framework to phys-
ical plants, like Engine, Transmission and Chassis
units by making use of various plant modeling tools
like Saber (www.synopsis.com/prototyping/saber),
GT Power (www.gtisoft.com), AmeSim
1
, CarSim
(www.carsim.com), and Software in the loop (SIL)
for control modeling. This strategy targets the vehicle
level and sub-system level modeling and simulation
for the purpose of software development for control
functions and their related calibrations. The objec-
tive is to reduce the usage of expensive mule vehicles
for the development and verification and validation
of software rich controls and calibrations. Because
of the potentially high overhead of vehicle and sub-
system level simulations, large scale multidisciplinary
simulation environments are emerging, e.g., Cosimate
(www.cosimate.com), and Functional Mockup Inter-
faces (FMI) (see www.fmi-standard.org for more de-
tails) enable the deployment of component simula-
tions on several hosts and guaranteeing the physical
(timing) synchronization between the different simu-
lators.
The Virtual Development and Integration of E/E
Architectures is in its early stages. This strategy
aims at supporting the architects in designing and
integrating system, sub-system, and ECU architec-
tures from the perspective of the execution platform
resources. This entails assessing the capacity re-
quirements of ECUs, serial data buses, core proces-
sors and the like, in order to support the require-
ments for controls, safety, security, etc. This strategy
is in the early stages from the perspective of a for-
mal and tool-based approach relying on formal mod-
els for the metrics of interest (e.g., a timing model),
and analysis and simulation tools that can help as-
sessing the best design candidate. Although it is in
its early stages, mature tools for software and mes-
sage timing analysis such as SymTA/S by Symtavi-
sion (www.symtavision.com), for software develop-
ment pre-silicon such as Virtualizer by Synopsys, and
for automated optimization driven design space ex-
ploration such as Model Center by Phoenix Integra-
tion (www.phoenix-int.com) exist. The virtual devel-
opment strategy also supports the current practice of
extensive validation steps starting from unit tests, do-
main bench testing and system level HIL testing be-
fore the final vehicle level testing.
In the rest of this paper, we elaborate on the var-
ious aspects of automotive E/E assets development
1
See www.plm.automation.siemens.com/en us under
their product lifecycle management products for more de-
tails.
Modeling and Analysis of Automotive Systems: Current Approaches and Future Trends
705