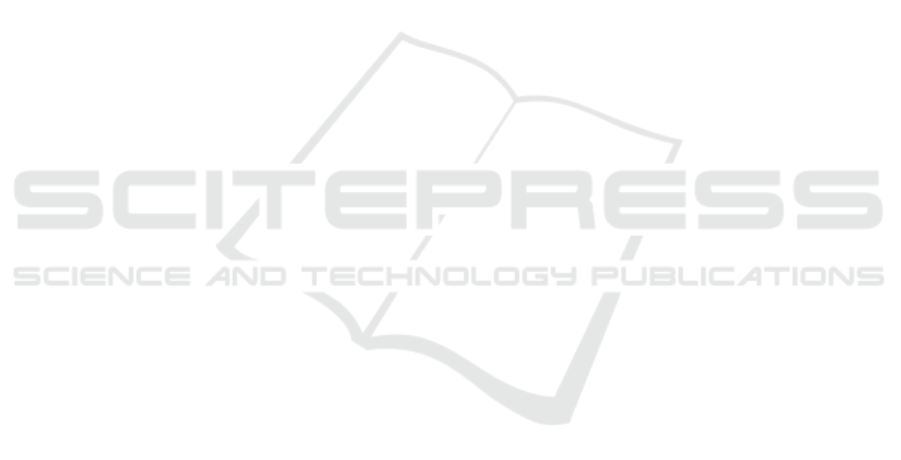
that implementation to the model.
ACKNOWLEDGEMENTS
A previous version of this paper appears in the first
author’s PhD thesis. The work described in this paper
was partially carried out in the context of the Danish
High Technology Foundation research project Off-
line and on-line logistics planning of harvesting pro-
cesses. We would like to thank all our colleagues on
the project for their valuable contributions and feed-
back, particularly Peter Gorm Larsen, Claus Grøn
Sørensen, Dionysis Bochtis and Morten Bilde. We
also thank Kun Zhou for his assistance with the har-
vest visualisation.
REFERENCES
Bochtis, D. and Sørensen, C. (2009). The vehicle routing
problem in field logistics part i. Biosystems Engineer-
ing, 104(4):447–457.
Broenink, J. F., Fitzgerald, J., Gamble, C., Ingram, C.,
Mader, A., Marincic, J., Ni, Y., Pierce, K., and Zhang,
X. (2012). Methodological guidelines 3. Technical
report, The DESTECS Project (INFSO-ICT-248134).
Edwards, G., Christiansen, M. P., Bochtis, D. D., and
Sørensen, C. G. (2013). A test platform for planned
field operations using lego mindstorms nxt. Robotics,
2(4):203–216.
Edwards, G., Jensen, M. A. F., and Bochtis, D. D. (2015).
Coverage planning for capacitated field operations un-
der spatial variability. International Journal of Sus-
tainable Agricultural Management and Informatics,
1(2):120–129.
Fitzgerald, J., Larsen, P. G., Mukherjee, P., Plat, N., and
Verhoef, M. (2005). Validated Designs for Object–
oriented Systems. Springer, New York.
Fitzgerald, J., Larsen, P. G., and Verhoef, M., editors
(2014). Collaborative Design for Embedded Systems
– Co-modelling and Co-simulation. Springer.
Gamma, E., Helm, R., Johnson, R., and Vlissides, R.
(1995). Design Patterns. Elements of Reusable
Object-Oriented Software. Addison-Wesley Profes-
sional Computing Series. Addison-Wesley Publishing
Company.
Hameed, I., Bochtis, D., Sørensen, C., Jensen, A. L., and
Larsen, R. (2013). Optimized driving direction based
on a three-dimensional field representation. Comput-
ers and electronics in agriculture, 91:145–153.
Jensen, M. A. F. (2014). Operations planning for agricul-
tural machinery under capacity constraints. PhD the-
sis, Aarhus University.
Jensen, M. A. F., Bochtis, D., Sørensen, C. G., Blas, M. R.,
and Lykkegaard, K. L. (2012). In-field and inter-field
path planning for agricultural transport units. Com-
puters & Industrial Engineering, 63(4):1054–1061.
Jin, J. and Tang, L. (2010). Optimal coverage path planning
for arable farming on 2d surfaces. Transactions of the
ASABE, 53(1):283.
Larsen, P. G., Lausdahl, K., and Battle, N. (2010). Combi-
natorial Testing for VDM. In Proceedings of the 2010
8th IEEE International Conference on Software Engi-
neering and Formal Methods, SEFM ’10, pages 278–
285, Washington, DC, USA. IEEE Computer Society.
ISBN 978-0-7695-4153-2.
Meyer, B. (1988). Object-oriented Software Construction.
Prentice-Hall International.
Nielsen, C. B., Lausdahl, K., and Larsen, P. G. (2012).
Combining VDM with Executable Code. In Derrick,
J., Fitzgerald, J., Gnesi, S., Khurshid, S., Leuschel,
M., Reeves, S., and Riccobene, E., editors, Abstract
State Machines, Alloy, B, VDM, and Z, volume 7316
of Lecture Notes in Computer Science, pages 266–
279, Berlin, Heidelberg. Springer-Verlag.
Oksanen, T. and Visala, A. (2009). Coverage path planning
algorithms for agricultural field machines. Journal of
Field Robotics, 26(8):651–668.
Scheuren, S., Stiene, S., Hartanto, R., Hertzberg, J., and
Reinecke, M. (2013). Spatio-temporally constrained
planning for cooperative vehicles in a harvesting sce-
nario. KI-K
¨
unstliche Intelligenz, 27(4):341–346.
Spekken, M. and de Bruin, S. (2013). Optimized routing
on agricultural fields by minimizing maneuvering and
servicing time. Precision agriculture, 14(2):224–244.
Tullberg, J. (2010). Tillage, traffic and sustainabilitya chal-
lenge for istro. Soil and Tillage Research, 111(1):26–
32.
Verhoef, M. (2009). Modeling and Validating Distributed
Embedded Real-Time Control Systems. PhD thesis,
Radboud University Nijmegen.
Zandonadi, R. S. (2012). Computational Tools for Improv-
ing Route Planning in Agricultural Field Operations.
PhD thesis, University of Kentucky.
SIMULTECH 2016 - 6th International Conference on Simulation and Modeling Methodologies, Technologies and Applications
32