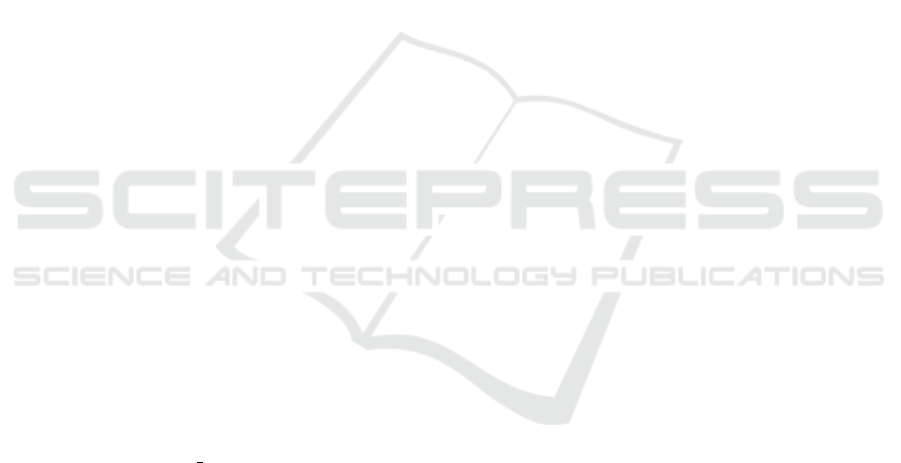
3.1 Idleness Detection
To perform idleness detection the system must have
the following features: (I) Inclusion of Places; (II)
Sensors Inclusion; (III) Passage Registration; (IV) In-
sertion of Event Logs; (V) Idleness Detection Core;
(VI) Detection of Groupings. In functionality (I),
based on the company’s building, each of its environ-
ments (rooms or departments) can be included as a
place and a type must be chosen for this place, which
can be a kitchen, restroom, meeting room, worksta-
tion, corridor, recreation room, warehouse or spare
room. Functionality (II) allows RFID readers to be
linked to the companies environments, reading the
employee’s location and gathering information that
can be used by the passage registration system. The
functionality (III) is responsible for whenever an em-
ployee passes by a sensor, the system checks which
place the sensor belongs to and stores both the time
and position in the database.
The functionality (IV) allows to add a log if there
are situations where the employee must be out of
his/her workstation (for a meeting, for example), so
not characterizing an idleness situation. The function-
ality (V) assumes that whenever the system identify
an employee out of his workstation for longer than
the time limit, must register a possible idleness in the
system. Finally, the functionality (VI) assumes that
whenever the system detects a stationary employee
out of his workstation for longer than the time limit,
you should check whether there are other employees
in the same place. When detected the existence of
two or more employees in the same place for longer
than the time limit set, the system starts to record the
possible grouping in the database, giving information
about the place, duration and employees.
The idleness detection algorithm starts at the end
of each working day. After the processing of all
employees by the IDAC IdlenessAnalyser module, it
does a search in the database to see if there is any
record of a Pass that has not been processed, these
records consists of: place, employee, incoming, out-
going, elapsed time and a flag that defines if it has
been processed or not. If all the markings have al-
ready been processed, the system stays in standby
state and repeats the procedure after a certain period
of time, but, if there is an unprocessed Pass marking,
the system gets the employee information and gathers
all his markings for that working day, sorting by the
incoming time. With all the employee’s Pass mark-
ings, the system starts a time counter that stores how
long the employee was out of his working station, so
this counter is incremented based on the difference
between the incoming and outgoing timestamps. The
algorithm goes into a loop that runs through the list
calculating the idleness period for all the Pass mark-
ings in which the employee was out of his working
station. The minimum time interval for which the
pass is considered idleness is defined by the Manager.
The process of verification of groupings consists
in the search for the passages of an employee for a cer-
tain environment that has last longer than defined by
the Manager. If the employee has a passage over the
time set as the minimum to check for groupings, the
system searches for registered groupings at that time
and place. If there is a grouping record, the employee
is registered as a participant of that group, otherwise it
searches in the database for other employees who re-
ported idleness in the same place and time, if positive
a new grouping record is created and both employees
are recorded.
3.2 Clocking Markings
For the system to perform clocking, it must have
the following features: Insertion of Marking Sen-
sors (I); Clocking record (II); Lunch Time Validation
(III); Time validation (IV); Extra and Negative Time
Record (V); Record Checking (VI); The functionality
(I) allows, based on loaded Places, RFID readers to
be linked to one of the possible entrances of the com-
pany, in order to record the entry and exit of employ-
ees. The functionality (II) assumes that whenever an
employee go through a marking sensor (a tag is read
by a reader), the system must store the time informa-
tion in the database as a Clocking Marking.
The functionality (III) assumes that at the end of
the workday the system should analyze how the em-
ployee spent his time in order to find longer than an
hour and less than two hours intervals and treat them
as lunch breaks. Functionality (IV) states that at the
end of the day the system should add the time spent
at the company for an employee in order to get actu-
ally worked time. Functionality (V), the system after
the marking and sum of total work time, check the in-
cidence of extra or negative hours of the employee,
recording it separately to enable the manager to treat
it correctly. The functionality (VI) assumes that the
application should be able to show the markings of
employees for themselves and, if there is any incor-
rect information, they can force a manual clocking
marking (Forced Marking) describing a justification
for it.
3.3 Management Tool
For the employees, the management tool should be
able to display the registered Clocking Markings, al-
lowing the inclusion of markings under justification,
RAIBS 2016 - Special Session on Recent Advancement in IoT, Big Data and Security
482