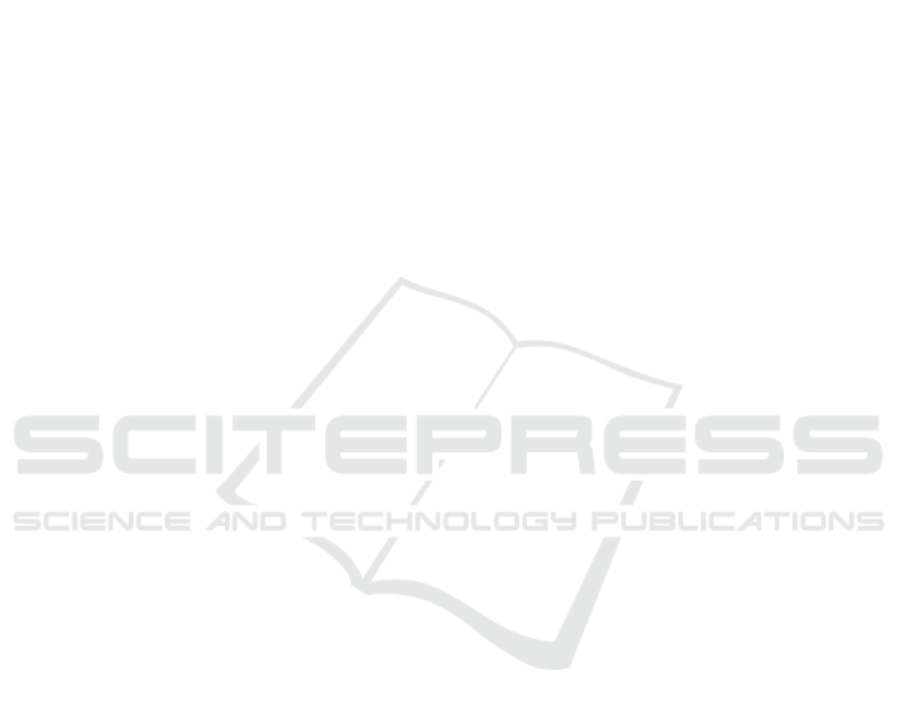
A Multi Finger Haptic Hand with Force Feedback
Mina R. Ramzy
1
, Emam F. Mohamed
2
, H. E. A. Ibrahim
2
and Yehia H. Hossamel-deen
3
1
Mechatronics Department, Higher Technological Institute, Tenth of Ramadan, Egypt
2
Electrical and Control Engineering Dept., Arab Academy for Science, Technology and Maritime Transport, Cairo, Egypt
3
Mechatronics Department, Future University in Egypt, Cairo, Egypt
Keywords: Robotic Hand, Glove Control, Haptic, Force Feedback.
Abstract: This paper presents a proposal for a twelve degrees of freedom robotic hand system controlled via haptic
technology with force control and force feedback. This robotic hand can be used in hazardous environment,
deserted places, or aerospace. To achieve this goal, an experimental set up in addition to a computer simulation
of this robotic hand system have been carefully designed and built. The experimental set up consists of three
main modules which are: the control Glove, the robotic hand, and a microcontroller. An integral controller
algorithm is applied to make the robotic hand track and follow the position and movement of the haptic glove
with force feedback. Three modes for force limitation are considered according to the application, which are
suitable for grasping of: brittle, elastic, and hard components. For computer simulation of the system, a
mathematical model has been derived considering a 3 DOF for each finger. To be compatible with robot hand
used in the experimental work, only four fingers are considered i.e. total 12 DOF. The experimental work
shows good gripping abilities following the glove movement and acceptable force feedback to the user hand,
while the simulation results give a qualitative agreement with the experimental ones.
1 INTRODUCTION
The word haptics is derived from the Greek word
haptikos that means “to be able to come into contact
with”. The study of haptics came from advances in
virtual reality. It is a form of human and computer
interaction that provides an environment that one can
explore through direct interaction with their senses.
For this project we are using a user at one end
(master) and a robot on the other (slave).
There must be feedback to interact with the
environment. That feedback is called haptic feedback
and also known as force feedback. As regards some
robotic tasks, a higher degree of precision is required,
which cannot be obtained from visual feedback only.
This adds a new dimension of control to help make
tasks more realistic. For example, the user should be
capable to feel the response from an object that she/he
touches at one end. Only the user at the control side
who can feel the response.
Haptics includes both kinesthetic and force
information that make the users to be able to feel the
texture of surfaces, temperature and vibration, etc.
and cutaneous (tactile) information that the skin feels
and do not necessarily need movement but rely
mainly on the skin receptors like the feel of forces
pushing on their skin and respond to them. The
feedback must be both accurate and fast enough to
meet the system requirements specified according to
the type of tasks that will be performed. (Adrian et al.,
2004).
A haptic system consists of two main parts: the
human part and the machine part. Both parts will be
provided with the necessary sensors, processors and
actuators. In the case of the human system, nerve
receptors implement sensing, brain implement
processing and muscles implement actuation of the
motion performed by the hand while in the case of the
machine part, the functions mentioned are performed
by the sensors, computer and motors; respectively.
(Rangoonwala et al., 2011).
The main objectives of this paper is to design and
implement a four finger robotic hand for grasping
objects of different shapes, sizes and material. This
hand is to be controlled by a glove. It follows the
movement of the user hand wearing the glove and at
the same time it gives the user a feel of how hard the
robotic hand is gripping the object by the force
feedback mechanism fixed to the glove. This project
has a variety of applications in the places where the
178
Ramzy, M., Mohamed, E., Ibrahim, H. and Hossamel-deen, Y.
A Multi Finger Haptic Hand with Force Feedback.
DOI: 10.5220/0005959401780184
In Proceedings of the 13th Inter national Conference on Informatics in Control, Automation and Robotics (ICINCO 2016) - Volume 2, pages 178-184
ISBN: 978-989-758-198-4
Copyright
c
2016 by SCITEPRESS – Science and Technology Publications, Lda. All rights reserved