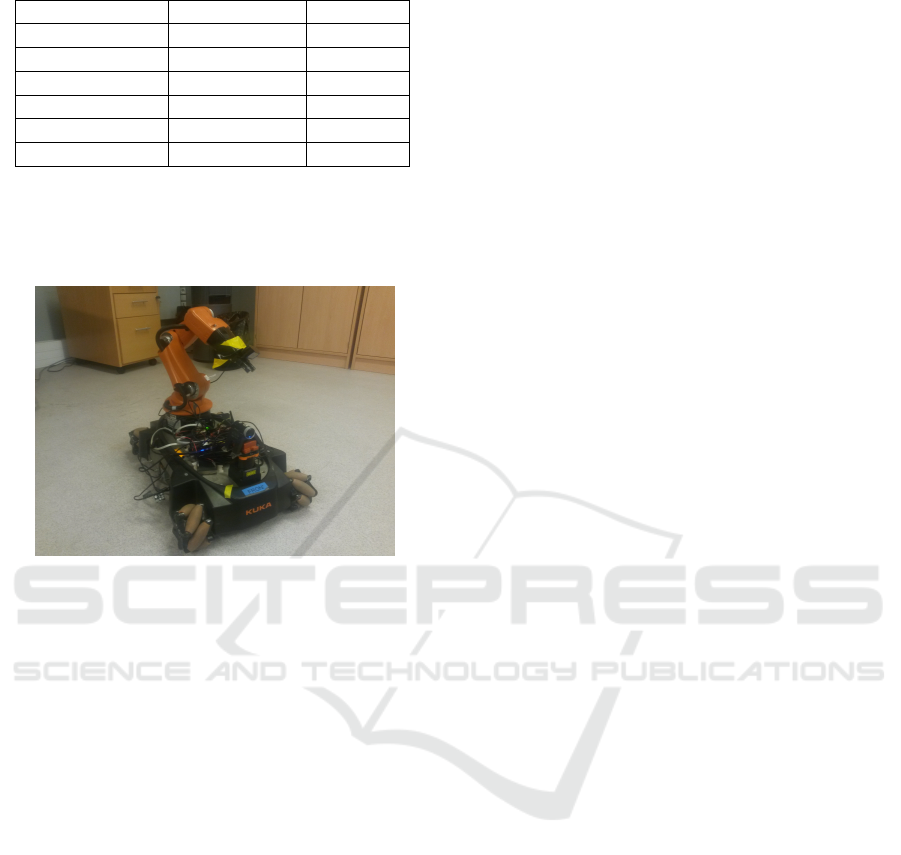
Table 3: Test 2 results.
Category # of collisions Best time
Expert 1 5’31”
Expert 0 4’20”
Project involved 3 6’51”
Project involved 6 5’45”
Entry level 3 8’46”
Entry level 8 10’29”
the joypad for the easiest part of the path, and they all
switched to the keyboard or the joypad for the most
difficult part.
Figure 7: The test platform used during the second test.
5 FUTURE WORK AND
CONCLUSIONS
In the future, more complex and precise feedbacks
have to be given to the operator. While operating a
robotic arm, it is extremely important to detect colli-
sions on the entire body of the arm: these feedbacks
can be reported visually to the operator, or physically,
actuating the haptic device or a sleeve equipped with
vibration buzzers can be worn by the operator.
Another important extension to the system is the
possibility to have a 3D view of the workspace: this
can be done using a depth camera mounted on the
robot. The collected information is then reported on
a 3D viewer. This will give to the operator the pos-
sibility to explore the workspace and to have multi-
ple views, which is not possible using only on board
cameras. Objects recognition and tracking could also
help the user in the grasping procedures and naviga-
tion (Mar
´
ın et al., 2002).
Above all, this paper showed that this preliminary
Graphical User Interface provides already an easy to
learn and easy to use environment. The feedbacks re-
ceived by the tester operators and their fast learning
time, as shown in the previous tables.
REFERENCES
C¸ avus¸o
˘
glu, M. C., Sherman, A., and Tendick, F. (2002).
Design of bilateral teleoperation controllers for hap-
tic exploration and telemanipulation of soft environ-
ments. Robotics and Automation, IEEE Transactions
on, 18(4):641–647.
Cohen, P. R., Johnston, M., McGee, D., Oviatt, S. L., Clow,
J., and Smith, I. A. (1998). The efficiency of multi-
modal interaction: a case study. In ICSLP.
Desbats, P., Garrec, P., Perrot, Y., Measson, Y., Geffard, F.,
David, O., Gargiulo, L., Idasiak, J.-M., and Piolain, G.
(2008). Overview of robotic technologies for nuclear
hazardous environments. In Proceedings of ANS Joint
topical meeting. Emergency Management & Robotics
for Hazardous Environments, March, pages 9–12.
Ferre, M. (1997). Interfaz Dise
˜
no de interfaces para robots
teleoperados. Desarrollo de un entorno de teleop-
eraci
´
on con caracter
´
ısticas multimedia. PhD thesis,
Tesis Doctoral. Universidad Polit
´
ecnica de Madrid.
1997. Madrid.
Keller, D., Perrot, Y., Gargiulo, L., Friconneau, J., Bruno,
V., Le, R., Soler, B., Tchah, M., Ponsort, D., Cham-
baud, P., et al. (2008). Demonstration of an iter rel-
evant remote handling equipment for tokamak close
inspection. In Intelligent Robots and Systems, 2008.
IROS 2008. IEEE/RSJ International Conference on,
pages 1495–1500. IEEE.
Kershaw, K., Feral, B., Grenard, J.-L., Feniet, T., De Man,
S., Hazelaar-Bal, C., Bertone, C., and Ingo, R. (2013).
Remote inspection, measurement and handling for
maintenance and operation at cern. International
Journal of Advanced Robotic Systems, 10.
Mar
´
ın, R., Sanchez, J., and Sanz, P. J. (2002). Object recog-
nition and incremental learning algorithms for a web-
based telerobotic system. In Robotics and Automa-
tion, 2002. Proceedings. ICRA’02. IEEE International
Conference on, volume 3, pages 2719–2724. IEEE.
Mar
´
ın, R., Sanz, P. J., Nebot, P., and Wirz, R. (2005). A
multimodal interface to control a robot arm via the
web: a case study on remote programming. Industrial
Electronics, IEEE Transactions on, 52(6):1506–1520.
Rolfe, A. (2007). A perspective on fusion relevant remote
handling techniques. Fusion Engineering and Design,
82(15):1917–1923.
Rolfe, A., Brown, P., Carter, P., Cusack, R., Gaberscik, A.,
Galbiati, L., Haist, B., Horn, R., Irving, M., Locke,
D., et al. (1999). A report on the first remote han-
dling operations at jet. Fusion engineering and design,
46(2):299–306.
Tian, G.-S., Tian, Y.-C., and Fidge, C. (2008). High-
precision relative clock synchronization using time
stamp counters. In Engineering of Complex Com-
puter Systems, 2008. ICECCS 2008. 13th IEEE Inter-
national Conference on, pages 69–78. IEEE.
An Advanced, Adaptive and Multimodal Graphical User Interface for Human-robot Teleoperation in Radioactive Scenarios
231