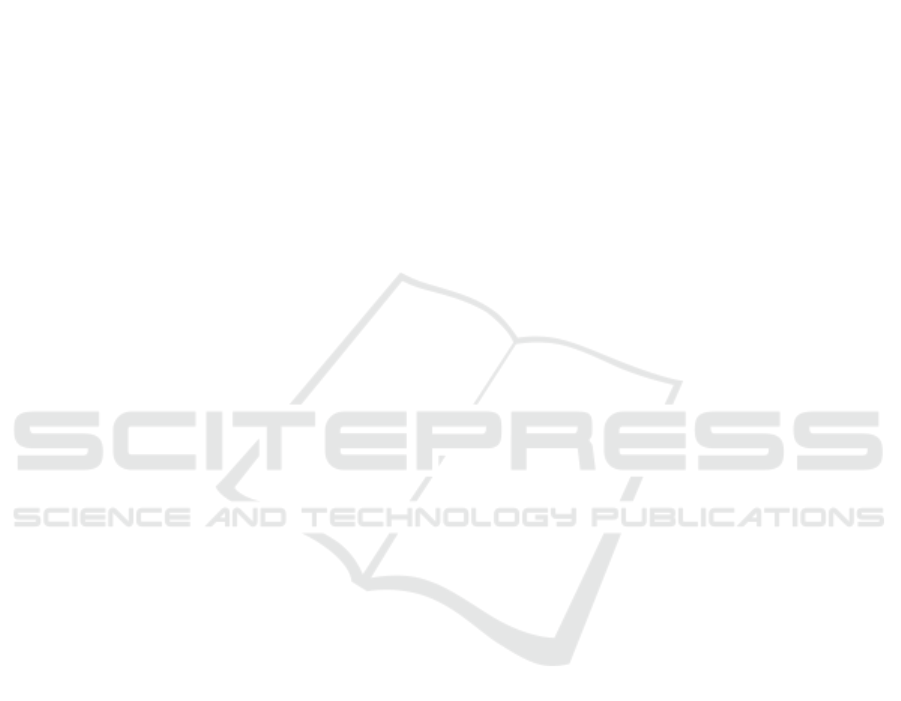
Researching Attitude-control Algorithm of Ejection Seats
based on Time-sharing Strategy
Minghuan Zhang
1
, Ming Wu
2
, Yu Su
1
and Cheng Zhang
1
1
School of Astronautics, Northwestern Polytechnical University, Xi’an, China
2
Aerospace Life-Support Industries, LTD, Xiangyang, China
Keywords: Ejection Seats, Attitude-control, Time-sharing Control, Minimum Safe Altitude, Optimization, Simulation.
Abstract: An attitude-control algorithm for ejection seats on “H” shaped motor is presented in this paper. The control
algorithm is based on time-sharing strategy, and the parameters in algorithm are optimized by using PSO
method. Through simulating under Matlab/Simulink in different ejection conditions, the infection of time-
sharing strategy in attitude-control is analyzed, and the minimum safe altitude is compared with K36D-
3.5A, ACES II and 120 ejection conditions in GJB 1800A-2007. The simulation results and analysis show
that this control algorithm on “H” shaped motor can improve escape performance at low-altitude and
adverse-attitude, thus proving the algorithm in this paper to be reliable and effective.
1 INTRODUCTION
Ejection seat is a key lifesaving appliance of modern
fighter in emergency (Wang, 2014), and its core
technology is attitude and trajectory control of the
seat after ejection. Most of ejection seats in service
at present are under the 3
rd
generation escape
system. To improve the pilot’s rescue, sequential
control technology (used in the 3
rd
generation) is
applied to make the seat for increasing the ejection
altitude (Miles, 2015 and Wang, 2014). Along with
high-tech of weapon, complexity of battlefield and
quicken of combat rhythm, pilot would be highly
possible to escape under low-altitude, adverse-
attitude conditions or at extremely high speed.
Therefore, it is imperative to achieve adaptive
control of ejection attitude. The 4
th
generation of
ejection seat is designed to solve the rescue problem
in low-altitude and adverse-attitude conditions
beyond the current generation, and its core is the
application of thrust vector continuous control
technology (Ma,2000 and Keller, 2008). By the fast
switching among thrust vector, the seat can gain
maximal lift as quick as possible. Thereby, the
safety is increased.
Technology on the 4
th
generation escape system
was start to study from 1970s, however, it has not
implemented for engineering application nowadays.
One of the main technical bottlenecks is the
application of thrust vector continuous control. U.S.
Air Force Research Lab proposed the structure of
the ejection seat under the 4
th
generation escape
system (Blairnald, 1998). The “H” shaped motor
installed on the seat so that the nozzles located at
four corners can obtain large moment arms for
attitude-control. It makes maintaining a constant
pressure become possible. (Feng, 2007) present a
safe altitude impact factor method under the 3
rd
generation. It analyzed infection of aircraft
parameters start from ejection to safe altitude.
Despite this work can improved escape performance
at medium-low-speed and lower-altitude somehow,
it only meet 44% of the minimum safe altitude in
GJB 1800-93. (Yuan, 2009) presents a nonlinear
inverse-dynamics method to design the control law
of the ejection seat under the 3
rd
generation. Results
under medium-low speed can be verified in 4
th
generation escape system, but the robustness of this
method need to be improved. Both of above two
methods are based on sequential control technology.
It can’t meet the requirement of the adaptive control
which is the symbol of the 4
th
generation.
We present a time-sharing attitude-control
algorithm based on thrust vector continuous control
technology. The parameters of controller is
optimized by Particle Swarm Optimization(PSO).
The experimental results and analysis show that this
algorithm can achieve fast robust attitude-control of
ejection seat. Moreoever, this strategy gives a new
262
Zhang, M., Wu, M., Su, Y. and Zhang, C.
Researching Attitude-control Algorithm of Ejection Seats based on Time-sharing Strategy.
DOI: 10.5220/0005975702620267
In Proceedings of the 13th International Conference on Informatics in Control, Automation and Robotics (ICINCO 2016) - Volume 2, pages 262-267
ISBN: 978-989-758-198-4
Copyright
c
2016 by SCITEPRESS – Science and Technology Publications, Lda. All rights reserved