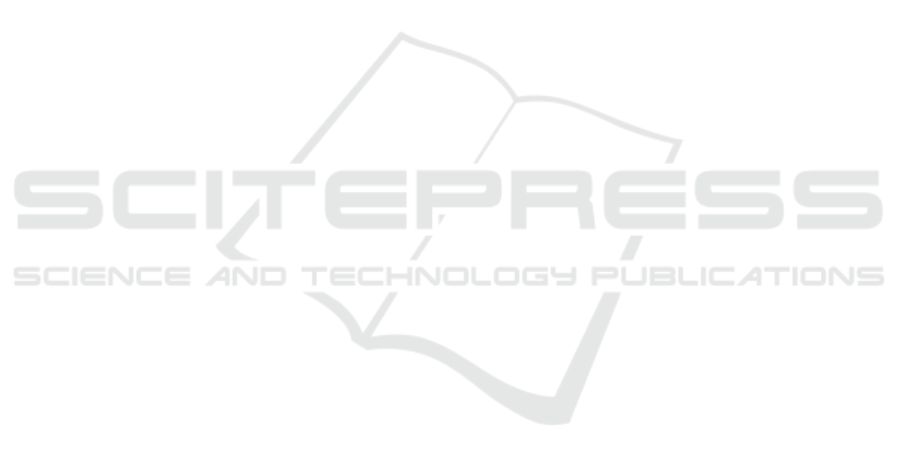
Bini, E. and Cervin, A. (2008). Delay-aware period as-
signment in control systems. In Proceedings of the
Real-Time Systems Symposium (RTSS), pages 291–
300, Barcelona, Spain. IEEE.
Cervin, A. (2003). Integrated Control and Real-Time
Scheduling. PhD thesis, Lund University.
Cervin, A. and Eker, J. (2000). Feedback scheduling of
control tasks. In Decision and Control, 2000. Pro-
ceedings of the 39th IEEE Conference on, volume 5,
pages 4871–4876 vol.5.
Cervin, A., Henriksson, D., Lincoln, B., Eker, J., and
˚
Arz
´
en,
K.-E. (2003). How does control timing affect perfor-
mance ? Analysis and simulation of timing using Jit-
terbug and TrueTime. IEEE Control Systems Maga-
zine, 23(3):16–30.
Crespo, A., Ripoll, I., and Albertos, P. (1999). Reducing
delays in rt control: the control action interval. In
Proceedings of the 14th IFAC World Congress, pages
257–262.
Gerber, R. and Hong, S. (1993). Semantics-based compiler
transformations for enhanced schedulability. Citeseer.
Gerber, R. and Hong, S. (1997). Slicing real-time pro-
grams for enhanced schedulability. ACM Transactions
on Programming Languages and Systems (TOPLAS),
19(3):525–555.
Henriksson, D. and
˚
Akesson, J. (2004). Flexible Imple-
mentation of Model Predictive Control Using Sub-
optimal Solutions. Institutionen f
¨
or reglerteknik,
Lunds tekniska h
¨
ogskola. Lund University.
Henriksson, D., Cervin, A.,
˚
Akesson, J., and
˚
Arz
´
en, K.-E.
(2002). On dynamic real-time scheduling of model
predictive controllers. In Proceedings of the 41st IEEE
Conference on Decision and Control, volume 2, pages
1325–1330, Las Vegas, NV.
Liu, C. L. and Layland, J. W. (1973). Scheduling algo-
rithms for multiprogramming in a hard-real-time en-
vironment. Journal of the ACM (JACM), 20(1):46–61.
Robert, D., Sename, O., and Simon, D. (2005). Sam-
pling period dependent RST controller used in con-
trol/scheduling co-design. In Proceedings of the 16th
International Federation of Automatic Control (IFAC)
World Conference, Czech Republic.
Robert, D., Sename, O., and Simon, D. (2010). An H
∞
LPV design for sampling varying controllers experi-
mentation with a T-inverted pendulum. IEEE Trans-
actions on Control Systems Technology,, 18(3):741–
749.
Ryu, M., Hong, S., and Saksena, M. (1997). Streamlining
real-time controller design : From performance spec-
ifications to end-to-end timing constraints. In Pro-
ceedings of the Third IEEE Real-Time Technology and
Applications Symposium (RTAS), pages 91–99, Mon-
treal, Canada.
Sahraoui, Z., Grolleau, E., Mehdi, D., Ahmed-Nacer, M.,
and Abdenour, L. (2016). Predictive-delay control
based on real-time feedback scheduling. to appear
in Simulation Modelling Practice and Theory under
DOI: 10.1016/j.simpat.2016.02.013.
Sahraoui, Z., Grolleau, E., Nacer, M. A., Mehdi, D., and
Bauer, H. (2014). Antinomy between schedulability
and quality of control using a feedback scheduler. In
Proceedings of the 22nd International Conference on
Real-Time Networks and Systems (RTNS), Versaille,
France, October 8-10, page 171. ACM.
Sename, O., Simon, D., and Ben Ga
¨
ıd, M. E. M. (2008).
A LPV approach to control and real-time scheduling
codesign : application to a robot-arm control. In Pro-
ceedings of the 47th IEEE Conference on Decision
and Control (CDC), pages 4891–4897, Cancun, Mex-
ico.
Seto, D., Lehoczky, J. P., Sha, L., and Shin, K. G. (1996).
On task schedulability in real-time control systems.
In Proceedings of the 17th IEEE Real-Time Systems
Symposium, pages 13–21, Washington, DC, USA.
Xia, F., Dai, X., Sun, Y., and Shou, J. (2006). Control ori-
ented direct feedback scheduling. International Jour-
nal of Information Technology, 12(3):21–32.
Xu, Y.,
˚
Arz
´
en, K.-E., Bini, E., and Cervin, A. (2014). Re-
sponse time driven design of control systems. In Pro-
ceedings of the 19th International Federation of Au-
tomatic Control (IFAC) World Congress, Cape Town,
South Africa.
Yepez, J., Fuertes, J., and Mart
´
ı, P. (2003). The large error
first (LEF) scheduling policy for real-time control sys-
tems. In Proceedings of the Real-Time Systems Sym-
posium WIP, pages 63–66, Cancun, Mexico.
Subtask Scheduling and Predictive-Delay Control - Comparison and Hybridization
109