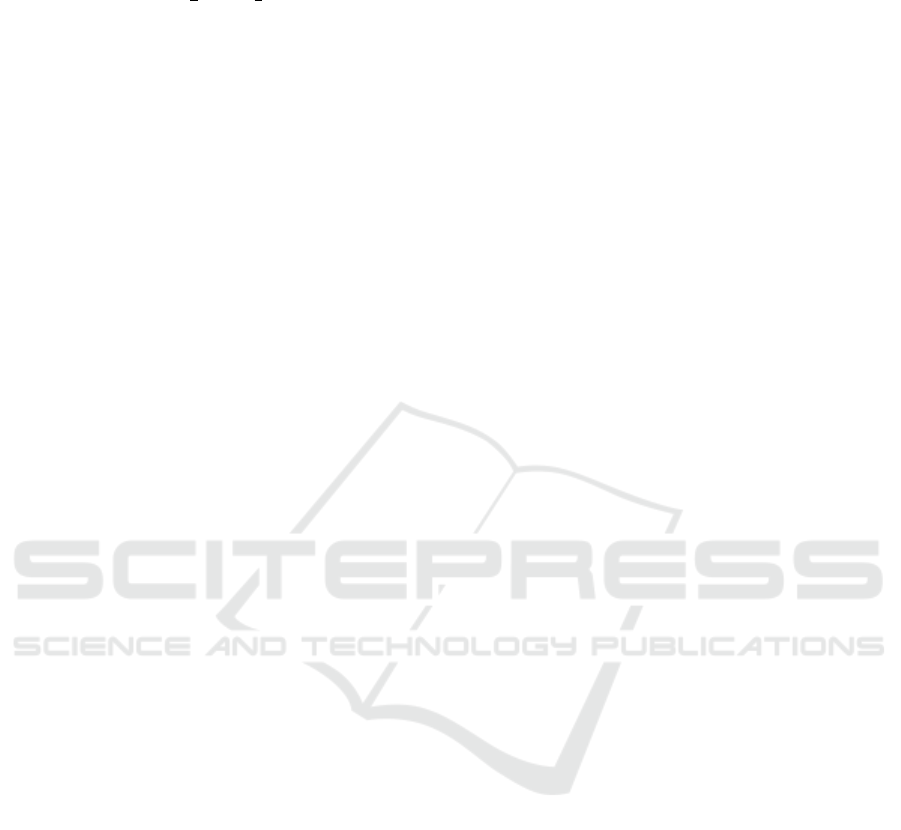
We choose the following Lyapunov function:
V (x) =
1
2
S
T
S +
1
2
T
r
( ˜w
T
˜w)
˙
V (x) = S
T
˙
S + T
r
( ˜w
T
˙
˜w)
˙
V (x) = S
T
˙
S + T
r
( ˜w
T
˙
˜w)
(11)
˙
V (x) = (S
θ
S
φ
S
ψ
)
˙
S
θ
˙
S
φ
˙
S
ψ
+ T
r
((
˜
θ
˜
φ
˜
ψ)
˙
˜
θ
˙
˜
φ
˙
˜
ψ
)
(12)
• Equation resolution for obtaining the estimated
variables θ, φ et ψ;
Stability condition:
˙
V (x) ≤ 0 (13)
(S
θ
S
φ
S
ψ
)
˙
S
θ
˙
S
φ
˙
S
ψ
+ T
r
((
˜
θ
˜
φ
˜
ψ)
−
˙
ˆ
θ
−
˙
ˆ
φ
−
˙
ˆ
ψ
) ≤ 0
(14)
The problem posed is to appear
ˆ
θ
ˆ
φ
ˆ
ψ
in the equa-
tions that govern the accelerations, but unfortu-
nately we managed to do it only for 2 variable
from 3. That return us to think about another type
of observation, or downright invites us to recon-
sider our equations.
6 VALIDATION
To determine the reliability of the model we have de-
veloped, we rely on Prosper OKTAL software used
by the world’s leading players in the transport sec-
tor as your: AIRBUS, ENAC, RENAULT, PSA, DGA,
VALEO, SNCF, KEOLIS, RATP, ALSTOM or BOM-
BARDIER. About this tool as an expertise which
refers more and more academic and scientific com-
munity.
7 CONCLUSIONS
This work deals with the topic of modeling and esti-
mating the state of the vehicle subsystems. First, we
looked at different knowledge models and dynamics
of vehicle behavior in the literature. These models
are then used throughout this work based on the prob-
lematic of the study.
The modeling of motor vehicles was developed to
understand their dynamic behavior. Indeed, such a
study has allowed us to understand the complexity of
the various phenomena that interfere in this area.
As regards the aspects of vehicle dynamics; we re-
alized that the most comprehensible way for the study
of vehicle behavior is to split the various dynamics in
parts. In this case, the chassis model, the aerodynamic
forces, gravity, suspension and wheel.
REFERENCES
www.ifsttar.fr.
Boualem, B. (2009). Caracterisation du comportement non
lineaire en dynamique du vehicule. PhD thesis, Uni-
versit de technologie de Belfort Montbeliard, Ecole
Doctoral Sciences pour L’Ingenieur et Microtech-
niques.
Hamadi, N. (2009). Modlisation d’un vehicule en prsence
des forces de contact roues/sol. PhD thesis, Universite
EL-Hadj Lakhdar Batna Algerie.
Hanane, B. (2013). Observateur non lineaire mode glis-
sant. PhD thesis, Universite FERHAT ABBAS Setif
Algerie.
Hichem, A., Salim, H., Lamri, N., Rene J V, B., and
Stephane, E. (2010). From design to experiments of a
2 dof vehicle driving simulator. IEE.
Imine, H. (2003). Observation d’etats d’un vehicule pour
l’estimation du profil dans les traces de roulement.
PhD thesis, Universite de Versailles Saint Quentin en
Yvelines.
Jaballah, B. (2011). Observateur robustes pour le diagnos-
tic et la dynamique des vehicules. PhD thesis, Uni-
versite Paul Cezanne Aix-Marseille III et l’Ecole Na-
tionale d’Ingenieurs de Monastir.
Maakaroun, S. (2011). Modelisation et simulation dy-
namique d’un vehicule urbain innovant en utilisant le
formalisme de la robotique. PhD thesis, Universite de
nantes, Ecole Doctoral de l’ecole des mines de nantes.
Nadji, M. (2007). Adequation De La Dynamique De Ve-
hicule a La Geometrie Des Virages Routiers, Apport
a La Securite Routiere. PhD thesis, Institut National
Des Sciences Appliquees Insa De Lyon.
Ouahi, M. (2011). Observation de systemes e entrees incon-
nues, applications a la dynamique automobile. PhD
thesis, Universite de Limoges Ecole Doctorale ED521
Sciences et Ingenierie pour l’information.
S, E., R, B., P, S., P, P., H, A., S, B., and D, D. (2009). Sim-
ulateur de detection des alterations du comportement
de conduite liees l’attention et la vigilance (vigisim).
Samuel, G.-B. (2006). Etude d’un systeme de controle
pour suspension automobile. PhD thesis, Universite
du Quebec.
Sleiman, H. (2010). Systemes de suspension semi-active a
base de fluide magnetorheologique pour l’automobile.
PhD thesis, Paris Tech, Ecole Nationale Superieure
d’Arts et Metiers.
Venture, G. (2003). Identification des parametres dy-
namiques d’une voiture. PhD thesis, Universite de
nantes, Ecole Doctoral de Nantes.
ICINCO 2016 - 13th International Conference on Informatics in Control, Automation and Robotics
526