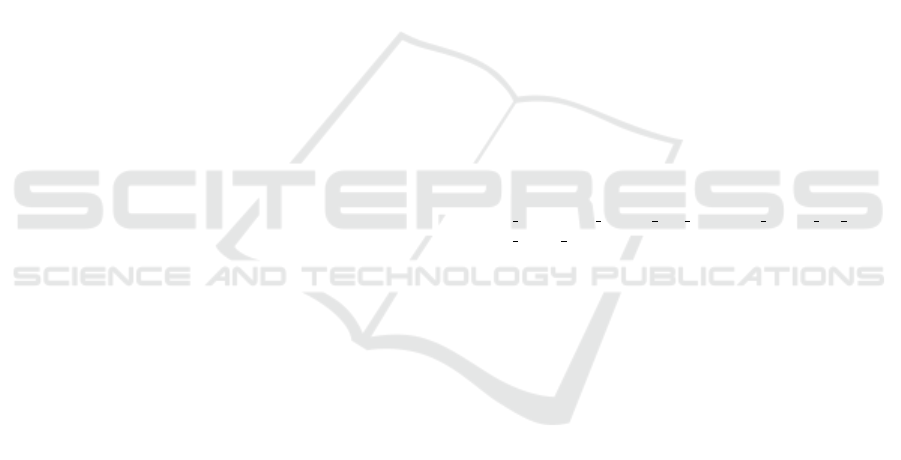
tion could be calculated by integrating the speed. Ad-
ditionally, optical markers on the ground of the pool
further improve the position estimate. The second
camera might be used for obstacle detection. With
this additional sensor information it would be possi-
ble to create a map of the area the AUV is moving
in.
As said before, the presented simplified model is
a good start. But e.g. the error in Figure 8, implies
that the system modell can be improved.
ACKNOWLEDGEMENTS
The project DAEDALUS is funded by the German
Space Agency (DLR, Grant number: 50NA1312)
with federal funds of the Federal Ministry of Eco-
nomics and Technology (BMWi) in accordance with
the Bundestag resolution of the German Parliament.
REFERENCES
Albiez, J., Gaudig, C., Hilljegerdes, J., and Kirchner, F.
(2015). FlatFish A compact subsea-resident inspec-
tion AUV. Unknown, 1(November).
Barngrover, C., Kastner, R., Denewiler, T., and Mills, G.
(2011). The stingray auv: A small and cost-effective
solution for ecological monitoring. In OCEANS 2011,
pages 1–8.
Bryant, S. (2002). Ice-embedded transceivers for europa
cryobot communications. IEEE Aerospace Confer-
ence Proceedings, 1(1):349–356.
Christensen, L., Kampmann, P., Hildebrandt, M., Albiez, J.,
and Kirchner, F. (2009). Hardware rov simulation fa-
cility for the evaluation of novel underwater manipula-
tion techniques. In OCEANS 2009 - EUROPE, pages
1–8.
Dowdeswell, J., Evans, J., Mugford, R., Griffiths, G.,
McPhail, S., Millard, N., Stevenson, P., Brandon, M.,
Banks, C., Heywood, K., Price, M., Dodd, P., Jenk-
ins, A., Nicholls, K., Hayes, D., Abrahamsen, E.,
Tyler, P., Bett, B., Jones, D., Wadhams, P., Wilkin-
son, J., Stansfield, K., and Ackley, S. (2008). In-
struments and methodsautonomous underwater vehi-
cles (auvs) and investigations of the ice/ocean inter-
face in antarctic and arctic waters. Journal of Glaciol-
ogy, 54(187):661–672.
Fechner, S., Kerdels, J., Albiez, J., and Kirchner, F. (2007).
Design of a uauv. In Autonomous Minirobots for Re-
search and Edutainment (AMiRE-2007). Proceedings
of the 4th International AMiRE Symposium (AMiRE-
2007), Heinz Nixdorf Institut Universit Paderborn,
pages 99-106.
Fossen, T. I. (2002). Marine control systems: guidance,
navigation and control of ships, rigs and underwater
vehicles. Marine Cybernetics AS.
Indiveri, G. (1998). Modelling and identification of under-
water robotic systems. Computer Science.
Kalman, R. E. (1960). A new approach to linear filtering
and prediction problems. Transactions of the ASME–
Journal of Basic Engineering, 82(Series D):35–45.
Leonessa, A. (2008). Underwater robots: Motion and
force control of vehicle-manipulator systems (g. an-
tonelli; 2006) [book review]. IEEE Control Systems,
28(5):138–139.
Meyer, B., Ehlers, K., Isokeit, C., and Maehle, E. (2014).
The development of the modular hard- and software
architecture of the autonomous underwater vehicle
monsun. In ISR/Robotik 2014; 41st International
Symposium on Robotics; Proceedings of, pages 1–6.
Mintchev, S., Donati, E., Marrazza, S., and Stefanini, C.
(2014). Mechatronic design of a miniature underwater
robot for swarm operations. In Robotics and Automa-
tion (ICRA), 2014 IEEE International Conference on,
pages 2938–2943.
Nicholson, J. and Healey, A. (2008). The present state
of autonomous underwater vehicle (auv) applications
and technologies. Marine Technology Society Journal,
42(1):44–51.
Ridao, P., Batlle, J., and Carreras, M. (2001). Model identi-
fication of a low-speed uuv. IFAC Conference Control
Applications in Marine Systems, Glasgow, Scotland.
Schmid, K. (2008). Embedded system and controller
design for a micro AUV Diploma thesis. The-
sis, University of Bremen, TU Hamburg Harburg.
https://www.researchgate.net/publication/299283880
Embedded system and controller design for a
micro AUV.
Yoerger, D. and Slotine, J.-J. (1991). Adaptive sliding
control of an experimental underwater vehicle. In
Robotics and Automation, 1991. Proceedings., 1991
IEEE International Conference on, pages 2746–2751
vol.3.
ICINCO 2016 - 13th International Conference on Informatics in Control, Automation and Robotics
196