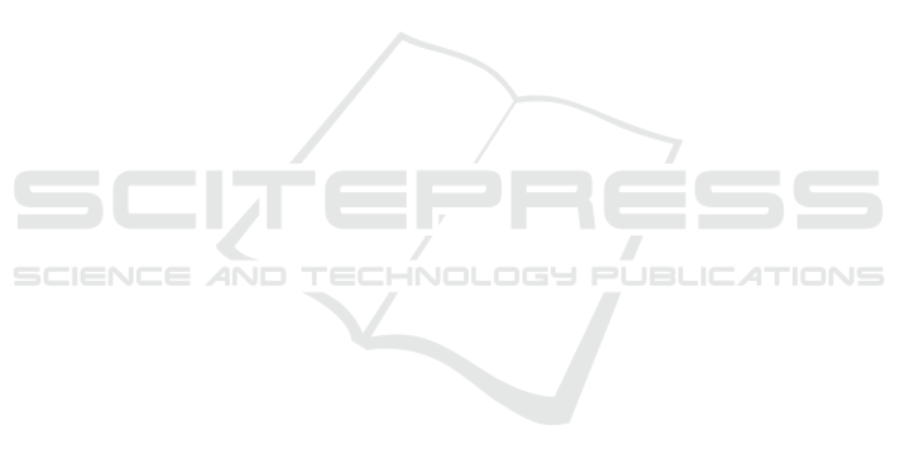
REFERENCES
Barrow, H., Tenenbaum, J., Bolles, R., and Wolf, H. (1977).
Parametric correspondence and chamfer matching:
two new techniques for image matching. In Proceed-
ings of the 5th international joint conference on Arti-
ficial intelligence-Volume 2, pages 659–663. Morgan
Kaufmann Publishers Inc.
Bay, H., Tuytelaars, T., and Van Gool, L. (2006). Surf:
Speeded up robust features. In Computer vision–
ECCV 2006, pages 404–417. Springer.
Choi, C., Taguchi, Y., Tuzel, O., Liu, M.-Y., and Rama-
lingam, S. (2012). Voting-based pose estimation for
robotic assembly using a 3d sensor. In Robotics and
Automation (ICRA), 2012 IEEE International Confer-
ence on, pages 1724–1731. IEEE.
C
´
ozar, J. R., Guil, N., and Zapata, E. L. (2001). Detection
of arbitrary planar shapes with 3d pose. Image and
Vision Computing, 19(14):1057–1070.
Drost, B., Ulrich, M., Navab, N., and Ilic, S. (2010). Model
globally, match locally: Efficient and robust 3d object
recognition. In 2010 IEEE Computer Society Confer-
ence on Computer Vision and Pattern Recognition.
Felzenszwalb, P. and Huttenlocher, D. (2004). Distance
transforms of sampled functions. Technical report,
Cornell University.
Hinterstoisser, S., Cagniart, C., Ilic, S., Sturm, P., Navab,
N., Fua, P., and Lepetit, V. (2012). Gradient re-
sponse maps for real-time detection of textureless ob-
jects. Pattern Analysis and Machine Intelligence,
IEEE Transactions on, 34(5):876–888.
Liu, M.-Y., Tuzel, O., Veeraraghavan, A., Taguchi, Y.,
Marks, T. K., and Chellappa, R. (2012). Fast ob-
ject localization and pose estimation in heavy clutter
for robotic bin picking. The International Journal of
Robotics Research, 31(8):951–973.
Lowe, D. G. (2004). Distinctive image features from scale-
invariant keypoints. International journal of computer
vision, 60(2):91–110.
Papazov, C., Haddadin, S., Parusel, S., Krieger, K., and
Burschka, D. (2012). Rigid 3d geometry matching
for grasping of known objects in cluttered scenes.
The International Journal of Robotics Research, page
0278364911436019.
Pretto, A., Tonello, S., and Menegatti, E. (2013). Flexi-
ble 3d localization of planar objects for industrial bin-
picking with monocamera vision system. In Automa-
tion Science and Engineering (CASE), 2013 IEEE In-
ternational Conference on, pages 168–175. IEEE.
Schnabel, R., Wessel, R., Wahl, R., and Klein, R. (2008).
Shape recognition in 3d point-clouds. In The 16-th
International Conference in Central Europe on Com-
puter Graphics, Visualization and Computer Vision,
volume 8. Citeseer.
Shotton, J., Blake, A., and Cipolla, R. (2008). Mul-
tiscale categorical object recognition using contour
fragments. Pattern Analysis and Machine Intelligence,
IEEE Transactions on, 30(7):1270–1281.
Skotheim, Ø., Lind, M., Ystgaard, P., and Fjerdingen, S. A.
(2012). A flexible 3d object localization system for
industrial part handling. In Intelligent Robots and
Systems (IROS), 2012 IEEE/RSJ International Con-
ference on, pages 3326–3333. IEEE.
S
¨
oderberg, R., Nordberg, K., and Granlund, G. (2005). An
invariant and compact representation for unrestricted
pose estimation. In Pattern Recognition and Image
Analysis, pages 3–10. Springer.
Steger, C. (2002). Occlusion, clutter, and illumination in-
variant object recognition. International Archives of
Photogrammetry Remote Sensing and Spatial Infor-
mation Sciences, 34(3/A):345–350.
Ulrich, M., Wiedemann, C., and Steger, C. (2009). Cad-
based recognition of 3d objects in monocular images.
In ICRA, volume 9, pages 1191–1198.
von Gioi, R. G., Jakubowicz, J., Morel, J.-M., and Randall,
G. (2008). Lsd: A fast line segment detector with a
false detection control. IEEE Transactions on Pattern
Analysis & Machine Intelligence, (4):722–732.
Zhang, Z. (1994). Iterative point matching for registration
of free-form curves and surfaces. International jour-
nal of computer vision, 13(2):119–152.
Model based Detection and 3D Localization of Planar Objects for Industrial Setups
367