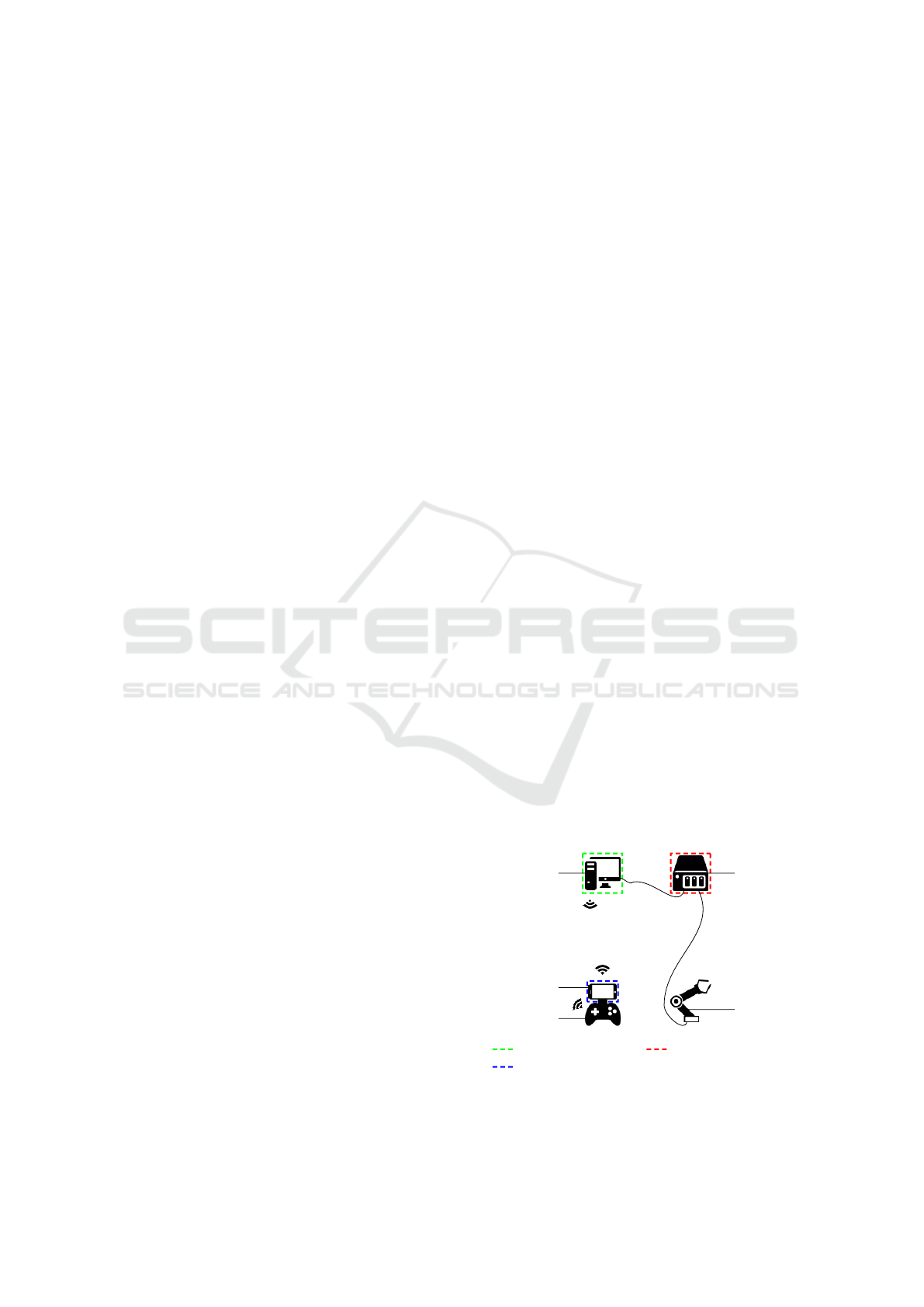
Another method for moving the robot is the man-
ual hand guidance. With this method the program is
taught by positioning the robot to the desired place
by hand. Modern lightweight robots offer such a
function, but with larger robots, this is not yet avail-
able. For heavier robots the movement can be sup-
ported by the robot motors, as shown by Colombo et
al. (Colombo et al., 2006). The robot has a force
and torque sensor that recognizes an outer force and
moves to the desired position accordingly.
Guiding a robot by vocal input has been realized
by Pires (Pires, 2005). The user has a fixed set of
commands to guide the industrial robot through tasks.
The operator uses his voice and tells the robot when to
stop, open or close the gripper or start welding. The
huge advantage of this interface is the natural commu-
nication since it is the same interface humans use to
exchange information. Secondly, it is easy to change
from one robot to another by simply saying the appro-
priate command. Furthermore, it reduces complexity
as the set of existing commands is smaller.
Hand gesture and face recognition has gathered a
lot of interest lately and many different approaches
of gestures can be recognized. Some approaches uti-
lize color information of camera images, as shown by
Br
`
ethes et al. (Br
`
ethes et al., 2004) and by Malima
et al. (Malima et al., 2006). The identification of
body parts based on depth sequence data is consid-
ered by Liu and Fujimura (Liu and Fujimura, 2004).
The main problem in the context of gesture recogni-
tion is the gesture spotting, which means when a ges-
ture command is starting or ending.
Modern motion control devices like the Nintendo
Wii Remote have also been used successfully for the
guidance of an industrial robot, shown by Neto et al.
(Neto et al., 2010). It provides a user easy means to
control a robot without expert robot knowledge and a
wireless and intuitive way to deal with common in-
dustrial tasks such as pick and place. This approach
has been compared to the manual guidance of a robot
and showed, that the manual guidance was faster in
completing given applications.
Some gamepad controls for robots have already
been realized. Especially for mobile robots the game-
pad is a popular control device, e.g. used by Caccamo
et al. (Caccamo et al., 2015). Colombo et al. used
a gamepad for an industrial robot arm, but there is
no approach and no further investigation explained
(Colombo et al., 2006).
2.2 Gamepad
Gamepads were first developed within the video gam-
ing industry (Cummings, 2007). The first gamepads
consisted a D-pad and two buttons. The D-pad is a
plus shaped button, which can be tilted in four (up,
down, left and right) or eight (plus the diagonals) di-
rections. Thus, it is ideal for simple movement con-
trols. As the possibilities within games became more
complex, the movement control within the game had
to be easier and more intuitive. When the videogames
started to become three-dimensional the D-pad was
starting to lose its meaning. In order to give the user
more control, the analog stick was introduced. Its
sensitivity and intuitiveness as well as the possibility
to choose between more orientations made it popular
and the analog stick became the dominant control for
three-dimensional problems.
3 APPROACH
In this approach a gamepad is used for the control
of an industrial robot. Usually, directly controlling
the robot from an external device is not offered by
the robot manufacturer. Thus, further components are
necessary for the communication (cf. Figure 1). One
part of the system is the robot arm connected with its
controller. Furthermore, the gamepad is connected to
the control computer. A wireless connection is pre-
ferred to improve the movability of the user. In addi-
tion, there is a smartphone attached to the gamepad to
show information to the user. It is used as a display
and also connected wirelessly to the control computer
by Wi-Fi. The control computer and the robot con-
troller are also connected to each other.
The main software part of this approach runs on
the control computer. The control software continu-
ously receives the state of the gamepad (cf. Figure 2).
All changes of the state—the pressing of a button or
the deflection of an analog stick—are processed fur-
Control
computer
Smartphone
Gamepad
Robot
controller
Robot arm
Control software
Visualization app
Interpreter program
Figure 1: System overview for the gamepad control for in-
dustrial robots.
Gamepad Control for Industrial Robots - New Ideas for the Improvement of Existing Control Devices
369