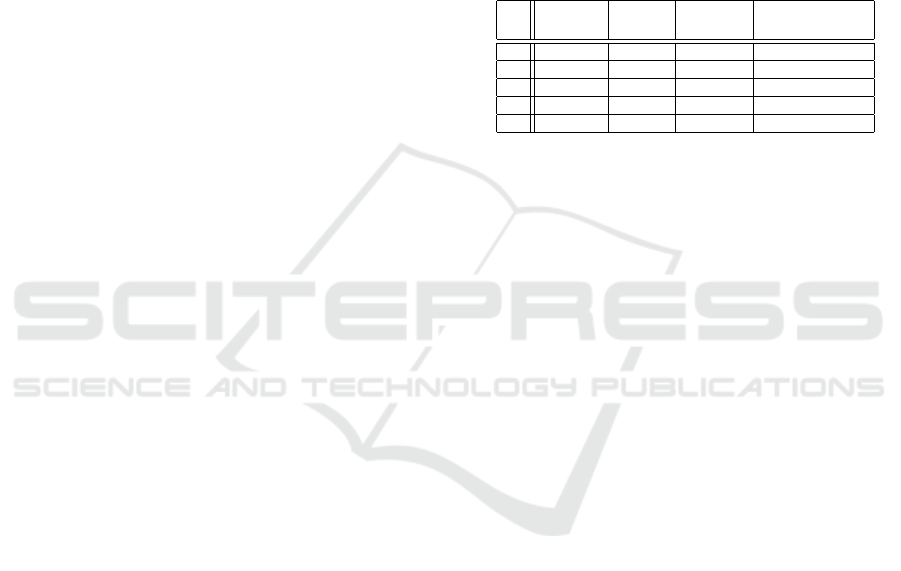
are coupled through a moving part that supports
a third 3 DOF serial chain. The first DOF of this
chain ensures the lateral rotation/medial rotation of
the shoulder. The fourth and fifth rotations ensure
the flexion/extension and the abduction/adduction
rotations of the elbow. The design of our device
was performed and validated under the SolidWorks
software.
2.3 Actuation, Transmission and
Reduction
The actuation, the reduction and the transmission are
closely coupled and must be designed together. They
are selected according to the requirements specified in
the last subsection. The type of the incorporated actu-
ators affects the overall weight of the device. In most
cases, a good actuator should be compact and light
as well as capable of producing the necessary power
to deliver necessary forces. There are tradeoffs be-
tween power, volume and weight since actuators ca-
pable of producing large forces are generally heavier
and are larger in size than those actuators capable of
smaller forces. The dimensioning procedure of the
actuator was performed under MotionWorks plug-in
of Solidworks, by applying dynamic forces on device
end-effector and then obtaining the required actuator
torques. We select brushed Maxon DC motors with
a low inertia and low friction, which are suitable for
this kind of devices. Maxon RE40 is used for the ab-
duction/adduction, flexion/extension rotations of the
shoulder and RE25 for the flexion/extension and the
abduction/adduction rotations of the elbow and the
lateral rotation/medial rotation of the shoulder.
In order to provide the highest amount of fidelity,
direct drive (absence of transmission of reduction) is
likely to be the best solution. However, this solu-
tion does not provide adequate forces/torques needed
for our application, which we saw earlier is criti-
cal. Among the other transmission and reduction
techniques such as the use of linkages, cables, steel
belts, shafts plus gears, this last one gives the worst
case (Hayward, 1995) since it causes high backlash
and high back-drive friction due to the gear gaps and
gear friction. Back-drive friction and backlash can be
reduced by using cable driven transmission systems.
Therefore, cable driven transmission technique (cap-
stan) was used in our design.
A solution consists of using a combined reduc-
tion (Planetary gear/capstan) in order to amplify the
torques developed by the actuators. We use plane-
tary gears reduction because it has fewer backlashes
and less friction, especially when the reduction ratio is
small (the reduction ratio are 4 for RE40 actuators and
19 for the RE25 actuators in this case). We have de-
signed capstan reduction mechanisms with a ratio of
20 for the abduction/adduction and flexion/extension
rotations of the shoulder and 10 for the lateral ro-
tation/medial rotation of the shoulder and the flex-
ion/extension and the abduction/adduction rotations
of the elbow. The resulting reduction ratios and the
maximal torque that could be generated for each axis
are presented in Table 2. This solution is able to pro-
vide additional torque for gravity and friction com-
pensation.
Table 2: Reduction ratio and maximal torque for each joint.
J Motor Total Resol. Max Torque
Ratio (N.m)
1 RE40 80 0.009
◦
14.5
2 RE40 80 0.009
◦
14.5
3 RE25 190 0.004
◦
5.6
4 RE25 12 0.06
◦
0.83
5 RE25 190 0.004
◦
5.6
As it was presented previousely, the exoskeleton
should include low inertia, no backlash, light weight
and negligible friction (Laycock and Day, 2003).
Therefore, a compromise has to be reached between
the various design goals. Obtaining negligible fric-
tion can be a problem, particularly when high stiffness
is required. High stiffness implies a stiff mechanical
interface which needs to be constructed from metal
which increase the friction and the overall weight of
the device. This provides a conflict between obtaining
high stiffness while keeping low friction (Baser et al.,
2006)(Laycock and Day, 2003). So that, the materials
used to construct such devices need to be considered
with additional costs. In our design:
• Aluminum was used in order to minimize the de-
flection due to the stiffness of the linkages.
• Cable driven transmission technique was used in
order to overcome backlash deflection.
• Stainless steel ball bearings and high precision
manufacturing methods were used in order to
overcome joint deflections.
The Computer Aided Design (CAD) model of the ex-
oskeleton is shown in Figure 2 and table 3.
2.4 Stress and Deflection Analysis
After the completion of the preliminary mechanical
design procedure, links shape and thickness must be
optimized to satisfy the design requirements men-
tioned before, such as the reduction of the inertia of
the device and the maximization of the stiffness. For
this structure, the links stress analysis is carried out
using COSMOSXpress plug-in of Solidworks. Static
ICINCO 2016 - 13th International Conference on Informatics in Control, Automation and Robotics
400